ОТ БЕЛОЙ ЗИМЫ - К ТОМТОРУ

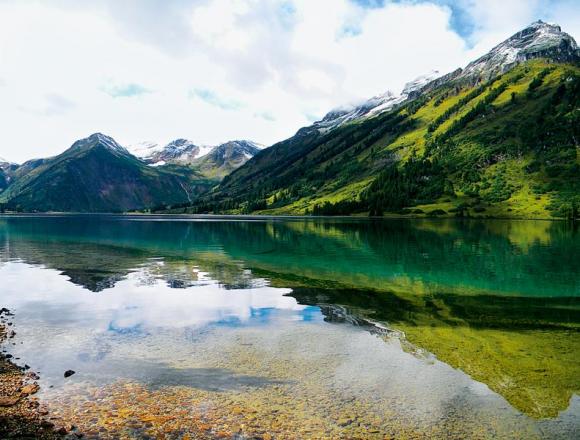
Более полувека назад, в 1961 г. была присуждена Ленинская премия за открытие и разведку первого в СССР Белозиминского месторождения фосфатно-ниобиевых карбонатитовых руд. Лауреатами стали 4 научных специалиста ВИМСа и 3 ведущих специалиста Иркутского геологоуправления Мингео СССР. Тем самым был осуществлен прорыв нашей страны в решении проблемы карбонатитовых месторождений Nb, Ta, TR, P, U и полиметаллов. Эти месторождения с начала 50-х годов открывались и вводились в эксплуатацию в Канаде, Бразилии и странах Африки. Примерно в это же время в Бразилии в течение нескольких лет было освоено месторождение пирохлоровых руд Араша, не имевшее до недавнего времени аналогов в мире как по запасам, так и по качеству ниобиевого сырья. Прямые инвестиции из США на стадии освоения месторождения, использование и постоянное совершенствование новейших технологий обогащения и переработки достаточно сложного поликомпонентного сырья позволили Бразилии за счет его эффективной эксплуатации не только оперативно рассчитаться с инвесторами, но и впервые в мире создать редкометалльно специализированный горно-химико-металлургический кластер и в течение 20 лет монополизировать мировой рынок феррониобия и ниобия. К сожалению, нашей Белой Зиме, первоначально оцененной в качестве потенциального промышленного источника ниобиевого сырья для производства феррониобия, была уготована, в отличие от своего бразильского «родственника» Араша, иная судьба, полная непредсказуемости и драматизма. До сих пор судьба этого месторождения не внушает оптимизма.
Белая зима - неоконченная история
Белозиминское месторождение фосфатно-ниобиевых карбонатитовых руд, включающее остаточные коры выветривания, после открытия более 60 лет назад продолжает оставаться в нераспределенном фонде в качестве крупного сырьевого источника ниобия (40% от разведанных в стране запасов) и фосфора (26 млн т Р2О5 по категории А + Б + С1 и 101 млн т Р2О5 по категории С2).
В 1959 г. месторождение, расположенное в таежных «дебрях», в 160 км севернее станции Тулун Транссибирской ж/д магистрали, посетила комиссия Госплана СССР, принявшая решение о составлении проекта на строительство ГОКа и одновременно — обогатительной фабрики до завершения разведки и утверждения запасов. Уже в то время Белая Зима рассматривалась не только как крупнейший в стране источник пирохлоровых концентратов для организации производства феррониобия — важнейшей легирующей добавки в стальные строительные конструкции и трубы для нефтегазопроводов, но и как источник попутного и, следовательно, наиболее дешевого апатитового концентрата.
В соответствии с решением этой комиссии в верховья р. Белая Зима по зимнику была доставлена партия заключенных, которая приступила к строительству. С этого момента контингент частично расконвоированных ЗК на долгие годы стал основной рабочей силой на строительстве, а затем и эксплуатации рудника и опытно-промышленной обогатительной фабрики, представляя собой и население рудничного поселка.
Не дремали и геологи-первооткрыватели и исследователи новых месторождений карбонатитовых руд в этом районе: Большетагнинского в 10 км к СЗ от Белой Зимы и Среднезиминского — в 18 км южнее [2]. В результате картирования Белозиминского месторождения было установлено, что коренные карбонатиты в основном представлены кальцитовыми разностями, которые на севере сменяются анкеритовыми. На карбонатитах развита остаточная кора выветривания мощностью от 10–20 до 70–100 м (в среднем 32 м) с содержаниями 0,5–1% N2O5 и 12–14% Р2О5.
В разрезе коры выветривания (снизу вверх) выделяются зоны карбонатной сыпучки и продуктивных охр (рис. 1). Продуктивный участок коры выветривания простирается вдоль долины р. Б. Зима на 4 км при ширине 0,5–1,2 км. В охристом горизонте сосредоточена подавляющая часть запасов фосфатного сырья (апатит с примесью франколита в верхних горизонтах). Максимальная продуктивность коры выветривания на ниобий (пирохлор) и фосфат (апатит) была установлена в южной части месторождения — в 2–2,5 раза выше, чем в коренных рудах. Технология обогащения белозиминских коровых руд первоначально была разработана специалистами ВИМСа совместно с ГИРЕДМЕТом [1-2]. Запасы ниобиевого и апатитового сырья по Белой Зиме впервые были утверждены ГКЗ в 1961 г.
Комплексный фосфатно-ниобиевый характер белозиминского сырья обусловил необходимость долевого финансирования 2-го этапа работ со стороны Минцветмета (ниобий) и Минхимпрома (фосфат) СССР. Ведомственная разобщенность интересов обусловила торможение организации и проведения как детальной разведки, так и решения сложных задач обогащения руд традиционными физико-механическими способами. В детальную разведку были вовлечены руды коры выветривания и южный участок месторождения, обогащенный ниобием. Однако реализовать результаты разведки, включая вторично утвержденные в ГКЗ запасы, удалось только организацией обогащения руд в небольших объемах на опытной обогатительной фабрике (ОФ). Здесь выпускался черновой пирохлоровый концентрат, который транспортировался на Урал, где на Вишневогорском ГОКе осуществлялась его доводка, а затем на Ключевском заводе передел на феррониобий. Кроме того, Белозиминская ОФ выпускала попутный апатитовый концентрат, а в послевоенные годы своего существования и ниобиевую лигатуру (40,65% Nb; 1,39% Р; 10,11% Al).
В Белозиминском поселке были построены брусовые дома на 500 чел., протянута ЛЭП, налажено снабжение со ст. Тулун по насыпной дороге и самолетом АН -2 в периоды ее размыва. На этом и закончилось задуман- ное строительство крупного ГОКа, способного обеспечить потребности СССР в феррониобии и сибирской его части — в фосфатных удобрениях. В середине 90-х годов Белозиминская фабрика прекратила свое существование, т.к. рухнула ЛЭП, а дизельное топливо поднялось в цене до уровней, недоступных небольшому производству и таежному поселению.
Однако главная причина крушения Белозиминского проекта заключалась в отсутствии в то время технологий, способных обеспечить эффективное получение 2-х дефицитных минеральных концентратов и конечных продуктов их переделов — феррониобия и фосфатных удобрений. На опытной фабрике достигнутое извлечение пирохлора в черновой концентрат не превышало 30% с соответствующими потерями в шламах, а его переработка в небольших объемах на феррониобий требовала дальних перевозок. Мало кто задумывался в советское время и о радиоэкологической безопасности горнопромышленных производств. Между тем в белозиминском пирохлоровом концентрате содержания урана составляют 47–880 г/т и тория — до 47 г/т, а в апатитовом, соответственно, 30 г/т и 100 г/т. В рудах в переменных количествах присутствуют и собственные минералы-концентраторы этих естественных радионуклидов. В то же время Белозиминский поселок был построен непосредственно на урансодержащей рудной залежи, щебнем которой были отсыпаны местные дороги, площадь аэропорта и все стройплощадки.
В 1991 г. группой сотрудников иркутской организации «Сосновгеология» были обнаружены опасные концентрации радона в жилых домах поселка: были выявлены аномалии, превышающие норму в 200 беккерелей/м3, в десятки раз! Не случайно долина р. Белая Зима была названа бурятами Харанты — черное, гиблое место. Как бы то ни было, а радоновая опасность послужила веским основанием для переселения в 2001 г. жителей заброшенного поселка в безопасное место, т.е. почему-то 10 лет спустя после обнаружения недопустимых радоновых аномалий. Уместно заметить, что бывший главный геолог Сосновской экспедиции, а затем 1-й замминистра Мингео СССР М.Д. Пельменёв незадолго до «перестройки» разослал директивное письмо о необходимости оценки радиационной безопасности разведуемых, эксплуатируемых и резервных месторождений, включая такие, как Ловозерское, Белозиминское и другие. Решение этой задачи заключается в выявлении закономерностей распределения в рудах урана и тория, соотношений между ними и минеральных форм концентрации. Сложнее решаются задачи устранения радиоактивных компонентов из технологических процессов и выпускаемой продукции [3]. Более того, при термической переработке сырья может происходить перераспределение радионуклидов и повышение их концентраций — в продуктах и отходах (твердых, жидких и газообразных).
Примечательно, что разведка Белозиминского месторождения осуществлялась с перерывами с 1956 по 1987 г., т.е. более 30 лет.
В 70–80-х годах всё еще обсуждались возможные варианты промышленного освоения Белозиминского месторождения. С использованием данных разведки были оконтурены 6 участков локализации богатых ниобием руд коры выветривания, рекомендованные специалистами ВИМСа для первоочередного освоения. При этом 90% запасов сосредоточено в пределах основного участка со средним содержанием 0,56% Nb2O5; максимальные содержания — 1,39% Nb2O5 установлены в рудах уч. Ягодного, который практически отработан. Даже при эксплуатации этого наиболее богатого рудного участка в 1971–1991 гг. технология обогащения, принятая на опытной ОФ, позволяла получать пирохлоровый концентрат с содержанием не более 30% Nb2O5 при извлечении от 3 до 40%.
Неслучайно в свое время зав. отделом редкометалльного сырья в ВИМСе А.И. Гинзбург неоднократно отмечал, что содержание ниобия в пирохлоровых рудах канадского месторождения Сент-Оноре соответствует его содержаниям в отходах обогащения руд Араша, а уровни его концентрации в рудах Белой Зимы еще ниже и примерно соответствуют отходам обогащения руд Сент-Оноре. Кроме апатито-пирохлоровых руд на месторождении выявлены редкоземельные паризит-монацитовые руды, приуроченные к центральной части крупного тела анкеритовых карбонатитов, скрытый штокверк Pb-Zn-х руд галенит-сфалеритовых руд с кальцитовыми. На юге месторождения по данным магнитометрии прогнозируется крупная залежь магнетитовых или титаномагнетитовых руд. Кроме того, в Зиминском рудном районе оценены запасы комплексного фосфатно-редкоземельно-редкометалльного сырья Большетагнинского и Среднезиминского месторождений. В целом эти результаты научно-производственных работ позволяют в перспективе рассчитывать на создание в этом районе фосфатно-редкоземельно-редкометалльного горнопромышленного кластера. Суммарная стоимость разведанного здесь сырья оценивается в 50 млрд долл. Однако во многом нерешенными остаются задачи создания эффективных обогатительно-передельных технологий глубокой переработки рассматриваемых видов минерального сырья, представленного как различными рудами коренных карбонатитов, так и корами их выветривания.
Химический состав охристых руд коры
выветривания месторождения Белая Зима
Минеральный состав фосфатно-редкометалльных руд месторождения Белая Зима
Специфика охристых руд коры выветривания белозиминских карбонатитов и их обогатимость
На месторождении Белая Зима промышленные типы руд представлены кальцитовой и высокожелезистой анкеритовой охрой и охристыми суглинками, которые составляют в объеме рудных тел 70, 10 и 20%. Содержание кварца, апатита, слюд и гидрослюд в типах руд составляет 2–5%, 12–50%, 12–27% соответственно; основное различие заключается в содержаниях гидрооксидов и оксидов железа: 55% в кальцитовой охре, 68% — в анкеритовой и 28% в суглинках. Охристые суглинки в качестве сырья для переработки не рассматриваются.
Химический состав руд, приведенный в табл. 1, свидетельствует о том, что главными компонентами руд являются оксиды фосфора, кремния, железа и кальция; ниобий и редкие земли содержатся в количестве 1–1,5%. Остальные компоненты — оксиды алюминия, марганца, магния, стронция, титана и щелочи промышленного значения не имеют. Основными минералами в рудах месторождения Белая Зима являются апатит и гидрооксиды железа, при этом фосфор на 82% связан в составе апатита, на 16% в составе шламов и только на 1% в составе второстепенных монацита и паризита. Концентраторами ниобия являются второстепенные в количественном отношении пирохлор, колумбит и гатчеттолит. В значительном количестве в рудах присутствуют силикаты и алюмосиликаты (табл. 2).
В то же время одни и те же компоненты входят в состав различных минералов, что является одним из серьезных препятствий для получения концентратов кондиционного качества (рис. 2).
Обогатимость охристых руд Белозиминского месторождения изучали специалисты таких авторитетных организаций, как ВИМС, ГИРЕДМЕТ, ИР ГИРЕДМЕТ, ГИГХС [4-7]. Основополагающей была определена магнитно-флотационная схема. Она предполагала дезинтеграцию руды и вывод в отвал бедной по содержанию ценных компонентов фракции крупнее 16 мм и так называемых первичных шламов. Фракция мельче 16 мм направлялась на доизмельчение до крупности меньше 0,2 мм. Суспензия измельченной руды после ее гидроциклонного обесшламливания по классу 20 мкм подвергалась магнитной сепарации. Полученную при этом немагнитную фракцию направляли затем на операцию флотации, при которой в пенный продукт выделяли фосфорсодержащий минерал — апатит. Сложность селективного разделения минералов при магнитной сепарации и флотации была связана с тем, что основной в количественном отношении минерал охристой руды — гидрогетит — покрывает пленками практически все минеральные зерна. Значительные потери ниобия, редких земель, фосфора при обогащении руды были связаны с фракцией мельче 20 мкм, с так называемыми вторичными шламами, направляемыми в отвал. Выход тонкодисперсных шламов, с которыми теряется 15% ниобия, 26% редких земель, 20% фосфора и 48% железа, превышал 30%. В этой связи сложилось пессимистическое убеждение, что извлечь ценные компоненты из материала такой крупности физическими методами невозможно и их потери являются неизбежными. Поэтому с начала 80-х годов разрабатывались физико-химические методы глубокой переработки белозиминского сырья — пирохимические и гидрохимические [4-7].
Химический состав минералов кальцитовой охры (Чистов Л. Б. 1986)
Рис. 2. Распределение химических компонентов между минералами руд коры выветривания месторождения Белая Зима
Однако такие шламы вполне могут быть переработаны в конечную продукцию по принципиально новой технологии ликвационной плавки силикатно-фосфатного сырья и тем самым потери ниобия, редких земель, фосфора и железа будут сведены к минимуму.
В ОИВТ РАН поставлена задача по разработке технологии комплексной переработки фосфатно-редкоземельно-редкометалльних руд месторождений коры выветривания, которая включает в себя физические методы обогащения (магнитная сепарация, флотация) и ликвационную плавку низкосортного фосфатно-редкометалльного сырья (бедных руд, шламов, хвостов и т.п.).
Химический состав минералов анкеритовой охры
На относительно небольшой пробе охристой руды Белозиминского месторождения, содержавшей 18,83% Р2О5, 0,92% Nb2O5, 26,5% Fe2O3 и 7,6% нерастворимого остатка и измельченной до крупности меньше 160 мкм (рис. 3) осуществлен поиск режимов обогащения без операции обесшламливания. Это позволило существенно повысить извлечение ценных компонентов и улучшить экономические показатели технологии обогащения.
Рис. 3. Высокожелезистая, шламистая охра месторождения Белая Зима
Эффективность отделения железосодержащих минералов (гидрогётита, гидрослюд) и тем самым повышения содержания апатита в немагнитной фракции, направляемой на флотацию, проверялась на валковом магнитном сепараторе СЭМ (производство института «Механобр») для сухой сепарации и на полиградиентном магнитном сепараторе «Рапид» (производство фирмы «Боксмаг-Рапид», Англия), работающем в мокром режиме. Более высокие показатели разделения были получены в сепараторе «Рапид» при магнитной индукции в рабочей зоне 1,65 Тесла. Зоной разделения магнитных и немагнитных частиц является кассета с помещенной в ней сеткой из прутков из нержавеющей стали. Магнитный продукт (Fe концентрат), полученный из охристой руды, содержит 44,8% Fe2O3, 1,55% Nb2O5 и 16,0% Р2О5 (рис. 4). После его обработки раствором азотной кислоты и полного растворения апатита содержание Fe2O3 увеличивается до 58,3%, а Nb2O5 до 2,02%. Продукт такого качества практически не содержит фосфора и может быть использован для производства феррониобия по карботермической технологии.
Благодаря выделению в магнитный продукт значительной части железосодержащих минералов, в первую очередь слабомагнитного гидрогётита, удается повысить содержание Р2О5 с 18,83% до 23,5% в немагнитной фракции, являющейся исходным материалом для последующей флотации апатита (рис. 4).
Рис. 4. Магнитная Фракция (Fe-концентрат) на Nd-Fe-B магните
Флотация апатита из немагнитной фракции в товарный концентрат
При поиске режимов флотации необесшламленной немагнитной фракции учитывался опыт, полученный при исследовании обогатимости рыхлых апатитовых руд. Экспериментальные исследования проводили во флотационной механической машине с емкостью камеры 0,5 литра при отношении твердого к жидкому 1:5. В качестве депрессора исползовалось жидкое стекло (расход 1,5 кг/т), а в качестве гидрофобизатора частиц апатита — смесь жирных кислот талловых масел с керосином (соотношение 1:1), к которой добавляли регулятор пенообразования в соотношении к собирательной смеси 0,5. Суммарный расход трехкомпонентной смеси, которая подавалась дробно, составил 750 г/т. После подачи воздуха во флотокамеру осуществляли съем пены, нагруженной в основном частицами апатита и частично минералами пустой породы. Основная флотация проводилась в течение 7 минут до «истощения» пены по минеральным частицам. Камерный продукт (хвосты флотации) имел выход 13,3% и содержал 7,2% Р2О5; 1,68% ниобия и 31,5% Fe2O3.
Черновой апатитовый концентрат подвергался трехкратной операции перечистки с целью возможно полного удаления примесей и концентрирования апатита. В результате этих операций был получен окончательный (готовый) апатитовый концентрат и три так называемых промежуточных продукта. Последние были объединены и проанализированы, также как и готовый концентрат, на содержание основных компонентов. Из результатов анализа, представленных на рис. 5, следует, что готовый концентрат содержит 36,85% Р2О5; 4,04% Fe2O3 и всего лишь 0,15% ниобия.
Извлечение апатита в концентрат от его содержания в исходной пробе составило 67,0% (от операции флотации 79,7%), что превышает показатели, полученные в предшествующих исследованиях при удалении вторичных шламов в отвал. В объединенный промпродукт извлекается 15,2% ниобия при его содержании 0,7%. Полученный готовый концентрат по содержанию апатита и железа пригоден для азотно-кислотной переработки на удобрения.
Азотнокислотная переработка апатитового концентрата с получением комплексных удобрений
Принципиальная схема азотнокислотной технологии переработки апатитового концентрата приведена на рис. 6. Апатитовый концентрат поступает на разложение 30%-м раствором HNO3 при температуре 80о С, продолжительности 2 часа и отношении Т:Ж в пульпе 1:2. Апатит на 99,9% разлагается в растворе азотной кислоты. Пульпа подвергается фильтрации, после чего фильтрат, представляющий собой азотно-фосфорнокислый раствор с содержанием 140–160 г/л Н3РО 4 и растворенным в нее азотнокислым кальцием нейтрализуется два раза. На первой стадии раствором аммиака до рН=1,7 с осаждением редкоземельных шламов, выход которых составляет ~ 6%. После сгущения редкоземельного осадка и вывода его из процесса фильтрат нейтрализуется второй раз известковым молоком (или раствором аммиака) с получением комплексных азотно-фосфорно-кальциевых удобрений типа нитроаммофоса (рис. 6), содержание Р2О5 в которых в лимоннорастворимой форме составляет не менее 98–99%. Нерастворимый остаток обогащается ниобием. Поскольку он практически не содержит фосфора, его можно подмешивать к магнитной фракции и использовать для получения феррониобия.
Для повышения извлечения апатита была испытана другая смесь флотационных реагентов, где в качестве собирателя флотации подавали жирные кислоты талловых масел, к которому добавлялся реагент регулятор пенообразования (соотношение реагентов составило 1:0,5; расход смеси при дробной подаче 750 г/т). Время основной флотации, как и в первом случае, составило 7 минут. Полученный черновой концентрат, как и в первом опыте, подвергался трехкратной перечистке. Полученный готовый концентрат при выходе 41,9% от исходного питания имел содержание 35,4% Р2О5, 3,91% Fe2O3 и 2,71% нерастворимого остатка.
Рис. 5. Технологическая схема обогащения высокожелезистой охры месторождения Белая Зима: мф - магнитная фракция, нмф - немагнитная фракция, к-т - концентрат, пр/пр - промпродукт, хвосты осн. фл. - хвосты основной флотации
1 - выход, %
2 - массовая доля Р2О5, %
3 - извлечение Р2О5, %
4 - массовая доля Fe2О3, %
5 - массовая доля н. о., %
6 - массовая доля н. о., %
7 - извлечение н. о., %
8 - массовая доля Nb2O5, %
9 - извлечение Nb2O5, %
Продукт такого качества отвечает требованиям азотнокислотной переработки его в удобрения. Извлечение апатита при таком реагентном режиме составило 78,8% от содержания в исходной пробе, или 93,7% от операции.
Сопоставление результатов этих испытаний показывает, что во втором реагентном режиме при некотором снижении качества апатитового концентрата (на 1,45%) извлечение апатита в концентрат от операции флотации оказалось на 14% выше.
Выполненные поисково-технологические исследования свидетельствуют о том, что результаты обогащения охристых апатитсодержащих руд Белозиминского месторождения по магнитно-флотационной технологии могут быть существенно улучшены за счет исключения операции обесшламливания перед магнитной сепарацией и флотацией.
Рис. 6. Принципиальная схема азотнокислотной переработки апатитового концентрата
Рис. 7. Образец азотно-фосфорно-кальциевого удобрения (преципитата)
Ликвационная плавка отходов обогащения: эффект одностадийного разделения ниобия и РЗМ фосфора
Хвосты флотации, промпродукты, нерастворимый остаток азотнокислотной переработки апатитового концентрата шихтуются и подвергаются ликвационной плавке, в процессе которой в соответствии с [4, 5] образуются два несмешивающихся расплава: силикатный железистониобиевый и фосфатно-солевой редкоземельный (рис. 8). Извлечение редких металлов в соответствующие расплавы высокое и составляет 80–85%. По своему качеству силикатный расплав пригоден для карботермической переработки на феррониобий, а фосфатно-солевой — для азотнокислотного вскрытия и получения преципитата, основной фосфатной фазой в котором является брушит (CaHPO4×2H2O).
Химический состав удобрительных фосфатов, полученных из азотно-кальциево-фосфатных растворов
Рис. 8. Ликвационная плавка отходов обогащения охристой руды Белой Зимы: С - силикатный расплав - концентратор ниобия; Ф - фосфатно-солевой расплав расплав - концентратор редких земель
Новые горизонты и перспективы: вектор Томтора
В настоящее время первоочередным объектом ускоренного промышленного освоения в России является уникальное месторождение высококомплексного железорудно-фосфатно-редкометалльного сырья Томтор на СЗ Республики Саха (Якутия). В пределах первого разведанного участка Буранный выделены три главных типа руд, сменяющие друг друга в вертикальном диапазоне: коренные карбонатитовые, остаточной коры выветривания и переотложенной коры выветривания. Наиболее богатыми полезными компонентами являются коры выветривания: остаточные мощностью 300–400 м представлены тремя разновидностями фосфатно-ниобиево-железорудного сырья, в то время как переотложенные средней мощностью 10 м представляют собой богатое редкометалльно-редкоземельное сырье, оцениваемое в качестве природных минерально-химических концентратов. По масштабам разведанных и потенциальных запасов, а также по уровням концентрации ниобия, редкоземельных металлов, включая среднетяжелую иттриевоземельную группу, иттрий и скандий Томтора превосходит Араша в Бразилии. В то же время, несмотря на целый ряд преимуществ Томтора, в том числе перед единственным в новой России действующим промышленным источником РЗМ, ниобия и тантала — Ловозерским месторождением, обращают на себя внимание два фактора, осложняющих его промышленное освоение: крайне неравномерное пространственное распределение разновидностей редкометалльно-редкоземельных руд в объеме месторождения и тонкодисперсный характер их глинистой матрицы, включая основные промышленно-ценные минералы, представленные пирохлором, монацитом и тремя алюмофосфатами (группой крандаллита). В частности, примечательно, что формы аномальных концентраций скандия до сих пор не установлены. Эти обстоятельства обусловливают невозможность выделения традиционными методами обогащения товарных минеральных концентратов и составления поминеральных балансов распределения в рудах профилирующих редких металлов и главных лимитируемых микрокомпонентов (1,5 кг/т Th, 50 г/т U и др.). Поэтому в процессе разведки уч. Буранный специалистами ВИМСа, ИХХТСО РАН (г. Красноярск) и др. была разработана гидрометаллургическая схема переработки редкоземельно-редкометалльной руды, предусматривающая ее вывоз с Томтора в г. Красноярск и извлечение редких земель на Железногорском горно-химическом комбинате. Однако по совокупности причин эта схема вызывает много вопросов. В частности, ее использование исключает получение феррониобия, равноценного по своей значимости выпуску редкоземельных продуктов. Производство химической ниобиевой продукции традиционно осуществляется из ловозерского лопарита и может быть существенно увеличено после технической модернизации действующего Соликамского ХМЗ. В то же время Томтор предоставляет уникальные возможности организации производства феррониобия на месте путем пирометаллургической переработки фосфатно-ниобиевожелезорудного сырья остаточной коры выветривания с применением ликвационной плавки, позволяющей эффективно разделять ниобий и фосфор за одну операцию. При этом может быть успешно адаптирована пирометаллургическая технология Араша, которая, в частности, позволяет проводить дезактивацию конечной продукции [8].
С этих позиций авторами в ОИВТ РАН в рамках Программы Президиума РАН №27 организованы специальные исследования богатых и рядовых пирохлор-монацит-крандаллитовых руд Томтора (уч. Буранный), результаты которых планируется опубликовать в следующем выпуске журнала.
ОТ РЕДАКЦИИ «РЗ»:
Одному из авторов настоящей статьи, эксперту нашего журнала Мелентьеву Г.Б. довелось в 70-х годах на месте ознакомиться с ситуацией, сложившейся на Белой Зиме в период отработки уч. Ягодного, в качестве куратора ИМГРЭ Мингео СССР по ниобию и танталу, в сопровождении химика-технолога и экономистов института. Добирались спецрейсом АН-2 над «зеленым морем тайги», поселились в одноэтажном деревянном гостиничном домике Минцветмета, где уже проживала бригада командированных специалистов ГИРЕДМЕТА, и для начала, рано утром, стали свидетелями образования гигантской карстовой воронки в 30–50 м от гостиницы, которая могла стать братской могилой для обеих групп научных специалистов. Выяснилось, что в технологию получения пирохлорового концентрата оказалась «встроенной» белозиминская специфика: при попытке очистить его от фосфора использовали 20 т соляной кислоты, которую сбросили на рельеф. В результате это спровоцировало развитие карста в карбонатных породах и привело к исчезновению рыбы в реке, давшей название месторождению, опытному производству и таежному поселку.
Было странно видеть крупнокристаллический темно-коричневый пирохлор в белом карбонатном щебне, которым были отсыпаны местные дороги на болотистых почвах и, казалось бы, полное его отсутствие в охристых рудах коры выветривания, добываемых в карьере и перерабатываемых на фабрике. Проблема их радиоактивности в те годы не обсуждалась. Зато были выслушаны истории о пожарах, инициированных расконвоированными ЗК на фабрике, о попытках захвата ими власти на фабрике и поселке, о специфике продовольственного снабжения авиарейсами, когда шампанское при распределении к праздникам не доставалось тем, у кого была своя корова, и т.д. К запаху тайги и ее дарам заметно примешивалась эйфория относительной свободы и равноправия расконвоированных в этом удаленном «от материка» и его администрации уголке необъятной Сибири.
Вернулись в Москву с добытой о белозиминском опытном производстве информацией и, главное, пробами охристых фосфатно-ниобиевых руд, которые не поддавались традиционному обогащению. Тогда и возникла впервые идея о возможности их обогащения путем плавления рудной шихты с добавками-флюсами, которые снижали температуру плавления до технологически приемлемых уровней и одновременно обеспечивали расслаивание расплава на несмешивающиеся жидкие фазы (слои), в которых избирательно концентрировались фосфор и ниобий. Эта идея была впервые реализована в начале 80-х годов Г.Б. Мелентьевым и Н.Ф. Давыдовым в ИМГРЭ и опубликована в целях внедрения в серии публикаций с одновременным оформлением авторского свидетельства на изобретение. Однако отсутствие у руководства ИМГРЭ заинтересованности в развитии нетрадиционных пирохимических технологий переработки труднообогатимого сырья, а затем и известная ситуация, в которой оказалась отечественная наука в условиях переходного периода, приостановили развитие этого инновационного перспективного направления в химической технологии до настоящего времени. Примечательно, что единомыслие соавторов публикуемой статьи обусловило успешное проведение в те же годы подобных поисково-технологических исследований в ГИГХСе на пробах фосфатно-ниобиевой коры выветривания Ново-Полтавского месторождения на Украине, результаты которого также остаются невостребованными.
Текст: Делицын Л. М., Рябов Ю. В., Мелентьев Г. Б.
Федеральное государственное бюджетное учреждение науки
Объединенный институт высоких температур РАН
Литература
1. Пожарицкая Л.К., Самойлов В.С. Петрология, минералогия и геохимия карбонатитов Восточной Сибири. — М: Наука, 1972. — с. 267.
2. Фролов А.А., Белов С.В. Комплексные карбонатитовые месторождения Зиминского рудного района (Восточный Саян, Россия). Геология рудных месторождений, т. 41, №2, 1999. С. 109-130.
3. Мелентьев Г.Б. Уровни концентрации и закономерности распределения естественных радионуклидов в природных и техногенных источниках редкоземельных металлов и их роль в оценке перспектив использования сырья. В сб. Технологическая минералогия в оптимизации процессов рудоподготовки и обогащения минерального сырья, VIII Росс. семинар Комиссии РМО по технологической минералогии, 23-24 апреля 2013 г. — С.-Петербург: ГИ КарНЦ РАН , 2014. С. 27-51.
4. Мелентьев Г.Б., Делицын Л.М., Лебедева Г.Г. и др. Перспективы пирохимической переработки комплексного фосфатно-редкометалльного сырья В сб. «Редкие элементы в нетрадиционном сырье и перспективы их попутного производства» — М: ИМГРЭ, 1987. С. 18-31.
5. Мелентьев Г.Б., Давыдов Н.Ф. Перспективы развития пирохимической технологии и связанных с ней минералого-геохимических исследований. В межведомственном сб. Проблемы направленного изменения технологических и технических свойств минералов. Под ред. проф. Ревнивцева В.И. — Л: Механобр, 1985. С. 17-34.
6. Рябов Ю.В., Делицын Л.М., Мелентьев Б.Н. и др. Перспективные разработки пирохимических способов получения фосфатных продуктов и удобрений из эндогенных источников сырья. Тезисы докл. II Всесоюзн. конф. по комплексному использованию руд и концентратов. Ч. III. — М: ИМЕТ АН ССС Р, 1983.
7. Лихнекевич Е.Г., Петрова Н.В., Михайлова Н.С. и др. Комплексная переработка ниобий-редкоземельно-фосфатных руд гидрометаллургическим способом. Разведка и охрана недр, №1, 1999. С. 42-43.
8. Мелентьев Г.Б., Самонов А.Е. Кому и зачем нужен Томтор? Стратегия развития. В международн. химич. ж. Химия и Бизнес, № 2(98). С. 17-21; №3-4(99-100). С. 49-54, №6(102). С. 52-57; 2009.
9. Мелентьев Г.Б., Самонов А.Е. Продвижение Томтора. В ж. Редкие Zемли, вып. 3, 2014. С. 34-39.
- 18 апреля 2024 РЕДМЕТ-2024
- 25 марта 2024 В мире будет расти глобальная конкуренция за обладание редкоземельным сырьем — Андрей Шевченко
- 21 марта 2024 Ассоциация РМ и РЗМ и Национальная ассоциация производителей источников тока «РУСБАТ» заключили соглашение о сотрудничестве Новости 21 марта 2024
- 19 марта 2024 Руслан Димухамедов выступил на III отраслевой конференции «Редкие и редкоземельные металлы»
- 18 марта 2024 Журнал «Редкие земли» на заседании Горного совета Северо-Западного федерального округа
- 18 марта 2024 Горнорудный дивизион Росатома расширяет выпуск редкоземельной продукции. При участии СМЗ выплавлен первый слиток металлического тантала
- 15 марта 2024 Соликамск отметил день рождения магниевого завода
- 7 марта 2024 III Отраслевая конференция «Редкие и Редкоземельные металлы»
- 2 марта 2024 Владимир Путин поручил нацелить геологоразведку на поиск редкоземельных материалов и другого сырья для экономики
- 16 февраля 2024 Замминистра ответил на вопросы журнала Редкие земли
- 15 февраля 2024 Андрей Андрианов о запуске в России производства постоянных редкоземельных магнитов
- 15 февраля 2024 Ключевые успехи российской промышленности представили на выставке-форуме «Россия»
- 13 февраля 2024 Дойти до конца цепочки
- 12 февраля 2024 Журнал «Редкие земли» на Торжественном вечере, посвящённом 300-летию Российской академии наук
- 7 февраля 2024 «Нет ничего выше и прекраснее, чем давать счастье многим людям», — Людвиг ван Бетховен.