Качество авиадвигателей проверят рентгеном

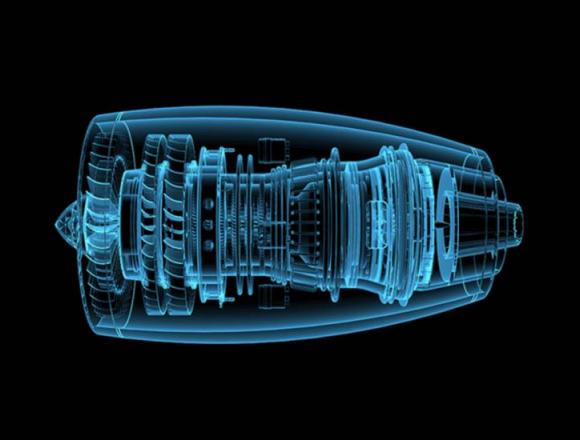
Фото: Пресс-служба Ростех
Проверка качества продукции проводится как на стадии производства, так и в ходе эксплуатации и ремонта с целью обнаружения дефектов или изменения свойств материалов. Рентгеновский контроль позволяет обнаружить внутренние дефекты деталей двигателей: трещины, поры и другие.
По словам главного инженера «Салюта» Юрия Нуртдинова, на предприятии введен в эксплуатацию уникальный аппарат, который применяется для решения задач контроля сварных швов деталей сложной формы. Его особенности заключаются в том, что он позволяет проводить проверку в тех случаях, когда геометрия изделия не позволяет производить съемку с расположением источника ионизирующего излучения с внешней стороны детали.
«Действие аппарата основано на регистрации и анализе ионизирующего излучения после его взаимодействия с объектом контроля. При помощи аппарата источник ионизирующего излучения вводится через отверстие внутрь детали, и проводится съемка, при этом кассета с пленкой остается снаружи. Результатом является снимок на рентгеновской пленке или цифровом носителе», - поясняется в сообщении.
Важным является наличие в этом аппарате специальной микрофокусной трубки, с помощью которой специалистам удалось решить одну из наиболее важных задач рентгеновского контроля – увеличение разрешающей способности. Данное оборудование позволяет гарантированно выявлять при малом фокусном расстоянии дефекты величиной порядка 0,1 мм.
Как отмечается в сообщении, применение аппарата позволило существенно снизить трудоемкость процесса контроля сварных швов изделий со сложной геометрией и тем самым значительно разгрузить производство: по сравнению процесса рентгеновского контроля детали «Барабан» с традиционным способом трудоемкость операции удалось снизить с 10 до 2 часов.
На предприятии оборудовано уже несколько участков рентгеноконтроля, где проверяются сложнейшие детали: крупногабаритные литые корпуса из титановых, магниевых и алюминиевых сплавов, пустотелые турбинные лопатки из жаропрочных никелевых сплавов, а также сварные соединения узлов со сложной геометрией. Напомним, что «Салют» занимается изготовлением и сервисным обслуживанием авиадвигателей для самолетов семейства Су-27, для учебно-боевого самолета Як-130, узлов двигателей для истребителей МиГ-29, а также участвует в широкой кооперации предприятий ОДК по производству двигателей семейства ТВ7-117, ВК-2500 и ПД-14.
- 18 апреля 2024 РЕДМЕТ-2024
- 25 марта 2024 В мире будет расти глобальная конкуренция за обладание редкоземельным сырьем — Андрей Шевченко
- 21 марта 2024 Ассоциация РМ и РЗМ и Национальная ассоциация производителей источников тока «РУСБАТ» заключили соглашение о сотрудничестве Новости 21 марта 2024
- 19 марта 2024 Руслан Димухамедов выступил на III отраслевой конференции «Редкие и редкоземельные металлы»
- 18 марта 2024 Журнал «Редкие земли» на заседании Горного совета Северо-Западного федерального округа
- 18 марта 2024 Горнорудный дивизион Росатома расширяет выпуск редкоземельной продукции. При участии СМЗ выплавлен первый слиток металлического тантала
- 15 марта 2024 Соликамск отметил день рождения магниевого завода
- 7 марта 2024 III Отраслевая конференция «Редкие и Редкоземельные металлы»
- 2 марта 2024 Владимир Путин поручил нацелить геологоразведку на поиск редкоземельных материалов и другого сырья для экономики
- 16 февраля 2024 Замминистра ответил на вопросы журнала Редкие земли
- 15 февраля 2024 Андрей Андрианов о запуске в России производства постоянных редкоземельных магнитов
- 15 февраля 2024 Ключевые успехи российской промышленности представили на выставке-форуме «Россия»
- 13 февраля 2024 Дойти до конца цепочки
- 12 февраля 2024 Журнал «Редкие земли» на Торжественном вечере, посвящённом 300-летию Российской академии наук
- 7 февраля 2024 «Нет ничего выше и прекраснее, чем давать счастье многим людям», — Людвиг ван Бетховен.