Аддитивные технологии - индикатор развития государства

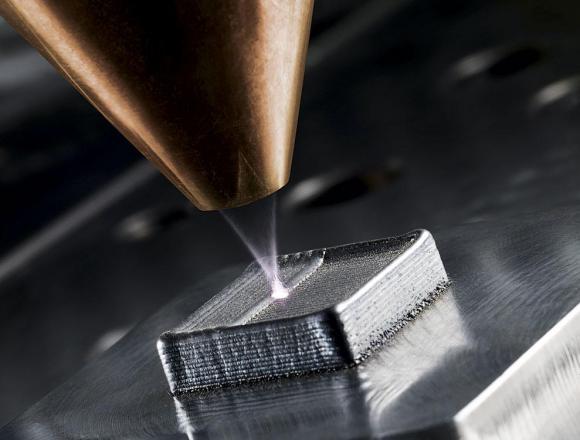
Аддитивные технологии с полным основанием относят к технологиям XXI века. Они имеют огромный потенциал в деле снижения энергетических затрат на создание самых разнообразных видов продукции. Степень их использования в промышленном производстве является верным индикатором индустриальной мощи государства и его инновационного развития. На данный момент российские предприятия используют импортные металлические порошки. Серийного производства порошковых материалов для аддитивных технологий в России нет.
Исследовательская группа «Инфомайн»
Основана в 1993 году. Специализируется на изучении рынков промышленной продукции в России и странах СНГ. Основными направлениями исследований являются: минеральное сырье, металлы и химические продукты. За прошедшие годы специалистами компании подготовлено свыше 1000 обзоров. Клиентами «Инфомайн» являются более 500 производственных, торговых, консалтинговых компаний, банков и научных организаций из 37 стран мира. Среди них: «Газпром», «Лукойл», ТНК-ВР, АФК «Система», ГМК «Норильский никель», «Евраз Груп С. А.», Объединенная компания «Русал» и др. Профессионализм компании подтверждается многочисленными публикациями в научных и научно-популярных журналах, а также выступлениями на конференциях различного уровня.
Металлические порошки обладают уникальными химико-металлургическими свойствами, что позволяет использовать их в различных областях. С появлением аддитивных технологий порошковая металлургия получила новые перспективы развития. Порошковая металлургия является наиболее экономичным методом изготовления изделий, она характеризуется низким уровнем отходов по сравнению с традиционными технологиями (литьем, механической обработкой, холодной и горячей обработкой давлением) и минимальным количеством операций для получения изделий с размерами, близкими к окончательным. Другая особенность порошковой металлургии — возможность производства материалов и изделий, которые невозможно получить традиционными металлургическими методами. С помощью аддитивных технологий упрощаются производственные процессы в авиационной промышленности, энергомашиностроении, приборостроении — везде, где есть потребность в изделиях сложной геометрии и «выращивании» металлических деталей. В настоящее время с точки зрения внедрения аддитивных технологий Россия отстает от ведущих стран мира. По-прежнему российские потребители зависят как от поставок импортных высококачественных металлических порошков, так и от импорта самих 3D-принтеров.
Состояние аддитивных технологий в мире
Технология трехмерной печати (3D) начала развиваться в конце 80-х годов прошлого века. Пионером в этой области является компания 3D Systems, которая в 1986 году разработала первый стереолитографический аппарат. Первые лазерные машины — стереолитографические (SLA) и затем порошковые (SLS-машины) — отличались очень высокой стоимостью, выбор материалов был достаточно узкий, и до середины 1990-х годов они использовались главным образом в научно-исследовательской и опытно-конструкторской деятельности, связанной с оборонной промышленностью. В дальнейшем, после широкого распространения цифровых технологий в области проектирования, моделирования и механообработки, 3D-технологии начали бурно развиваться. Для 3D-технологий в настоящее время рекомендован термин Additive Manufacturing (AM). По данным Wohlers Associates, мировой рынок АМ-технологий в 2014 году составил около 3 млрд долларов при средних темпах роста на уровне 20–30%. Прогнозируется, что к 2020 году объем рынка может достичь 16 млрд долларов. Рынок аддитивных технологий стремительно меняется, происходит слияние и поглощение компаний-производителей машин, возникают новые центры оказания услуг в области AM-технологий, эти центры объединяются в европейскую, а теперь уже и в глобальную сеть. 63% всех аддитивных машин в мире производится в США. Наиболее заметно внедрение АМ-технологий в таких отраслях, как авиационная промышленность, судостроение, энергетическое машиностроение, а также стоматология и восстановительная хирургия. Главными заказчиками и потребителями AM-продукции являются авиационная и автомобильная отрасли США и Европы. Эти технологии привлекают крупные промышленные компании: Boeing, Mersedes, General Electric, Lockheed Martin, Mitsubishi, General Motors. Например, компания Boeing в последние годы значительно увеличила номенклатуру деталей, изготавливаемых по AM-технологиям. Сейчас таким образом изготавливается более 22 тысяч деталей 300 наименований для 10 типов военных и коммерческих самолетов, включая Dreamliner. Отказ от производства цельнометаллического листа в пользу спекания порошков при формировании каркасов ряда моделей Boeing позволил компании перейти на принципиально новый уровень производства. По мнению специалистов General Electric, через 10 лет примерно половина деталей энергетических турбин и авиационных двигателей будет изготавливаться с помощью AM-технологий. Активно применяются аддитивные технологии в бытовой электронике и медицине, в том числе в стоматологии. По словам представителей компании Arcam, произведенные ими устройства были использованы для создания более 30 000 титановых имплантатов для реконструкции тазобедренных суставов. Основным отличием АМ-технологий является то, что они применяются для формирования детали при помощи наращивания материала, в отличие от удаления в случае механической обработки. Использование аддитивных технологий позволяет изготавливать детали с характеристиками, недоступными для других методов обработки (например, с криволинейными отверстиями или внутренними пустотами). Послойный метод построения детали дает абсолютно новые возможности, например изготовление «деталь в детали», деталей с переменными по толщине свойствами материала (так называемые градиентные материалы), выпуск сетчатых конструкций, которые невозможно получить ни литьем, ни механообработкой. Значительные перспективы для 3D-технологий открываются в аэрокосмической отрасли. Это связано с тем, что с их помощью стало возможным кардинально уменьшить отношение массы материала, необходимого для выпуска детали, к массе конечной детали. Для большинства деталей, изготавливаемых традиционным способом, это соотношение может достигать 20:1, при использовании аддитивных технологий этот показатель составляет в худшем случае 2:1.
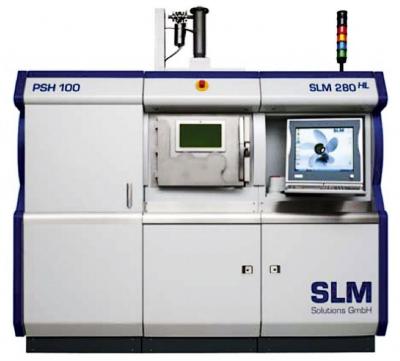
Рис. 1. Аппарат селективного лазерного сплавления SLM 280 компании SLM Solutions (Германия)
Почти все компании, использующие лазер, по-разному называют свои технологии. Это сделано для того, чтобы отличить себя от конкурентов, но по технической сути все они являются технологиями селективного лазерного сплавления — SLM-технологиями. Однако это название негласно закреплено за компанией SLM Solutions. Компания SLM Solutions (Германия) является одним из мировых лидеров в области технологий лазерного синтеза. SLM Solutions активно сотрудничает с компанией FILT. В результате этого сотрудничества появилась наиболее «продвинутая» на сегодняшний день машина SLM 280 (рис. 1). Этот аппарат отличается наличием двух лазеров: внешний контур детали и тонкие стенки обрабатывает первый лазер мощностью 400 Вт, основное тело детали — второй, более мощный лазер (1000 Вт). Сочетание двух лазеров разной мощности позволяет выпускать детали с толщиной отдельных фрагментов до 0,3 мм. Это также придает аппарату существенные преимущества: увеличивается скорость построения детали (до 5 раз), улучшается внутренняя структура материала и чистота внешней поверхности.
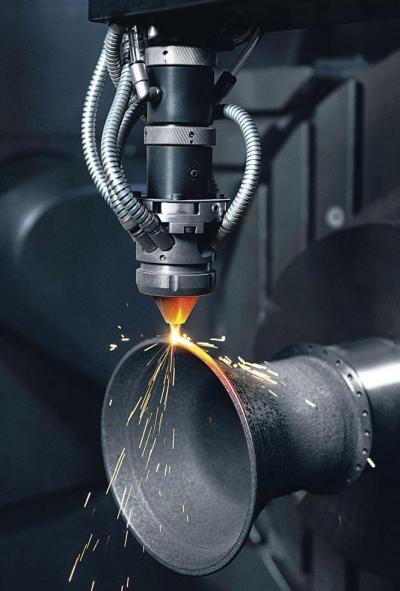
Виды аддитивных технологий
По методам формирования слоя принципиально отличаются два вида аддитивных технологий. Технология Bed Deposition предполагает на первом этапе формирование слоя порошка с последующей выборочной (селективной) обработкой сформированного слоя лазером или иным способом. Этой технологии достаточно точно соответствует термин «селективный синтез» или «селективное лазерное спекание» (SLS — Selective Laser Sintering), если «отверждающим» инструментом является лазер, который в данном случае, в отличие от лазерной стереолитографии (SLA-технологии), является источником тепла, а не ультрафиолетового излучения. Второй вид Direct Deposition — прямое, или непосредственное, осаждение материала, т. е. непосредственно в точку, куда подводится энергия и где в данный момент происходит построение фрагмента детали. Наиболее широко на рынке представлены модели группы Bed Deposition. Большая часть компаний — производителей таких аппаратов использует в своих машинах лазер в качестве источника энергии для соединения частиц металлопорошковых композиций. К ним относятся: Arcam (Швеция), Concept Laser (Германия), EOS (Германия), Phenix Systems (Франция), Realizes (Германия), Renishaw (Великобритания), SLM Solutions (Германия), Systems (США). В 2012 году в эту группу вошли китайские компании Beijing Long Yuan Automated Fabrication Systems и Trump Precision Machinery. Ко второй группе машин (Direct Deposition) относятся аппараты компаний POM Group, Optomec, Sciaky (США), Irepa Laser (Франция), InssTek (Ю. Корея). В России отсутствует серийное производство АМ-машин, которые используют в качестве материала металлические порошки. Вместе с тем целый ряд организаций занимается разработкой и созданием опытных образцов подобного типа аппаратов. Например, ОАО «Электромеханика» (Тверская область) в рамках совместной работы с ФГБОУ ВПО «МГТУ «СТАНКИН» изготовило автоматизированную 3D-установку для выращивания в вакууме точных титановых заготовок сложных деталей методом послойного синтеза электронным лучом из металлического мелкодисперсного порошка. ОАО «ТВЭЛ» совместно с научными организациями Уральского отделения РАН ведет разработку и организацию производства установок УрАМ-550 для селективного лазерного сплавления металлических порошков с размером рабочей камеры 500×500×500 мм. «Росатом» в кооперации с Минобрнауки планирует создать опытный образец 3D-принтера для изготовления металлических изделий на базе НПО «ЦНИИТМАШ». Специалистами ОАО «Национальный институт авиационных технологий» разработаны несколько типов экспериментальных лазерных установок послойного синтеза. Разработки аппаратов для лазерного послойного синтеза ведутся также Институтом проблем лазерных и информационных технологий (ИПЛИТ).
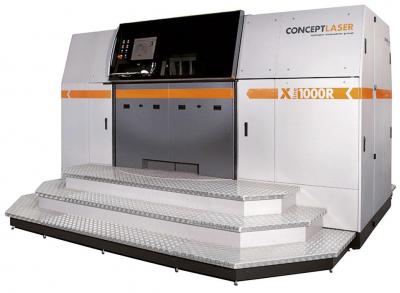
Рис. 2. АM-машина X line 1000R компании Concept Laser
До недавнего времени самой большой AM-машиной компании считалась X line 1000R (рис. 2) с размерами зоны построения 630×400×500 мм. Она была разработана совместно с Фраунхоферским институтом лазерных технологий (FILT) при участии Daimler AG и вышла на рынок в 2013 году. Первая такая машина установлена на Daimler AG для выращивания автомобильных компонентов из алюминия. К этой модели недавно была добавлена модификация X line 2000R, оснащенная двумя лазерами мощностью по 1000 Вт. Область построения увеличена до 800×400×500 мм. Компания пошла навстречу требованиям клиентов из аэрокосмической и автомобильной отраслей, повысив скорость построения изделий.
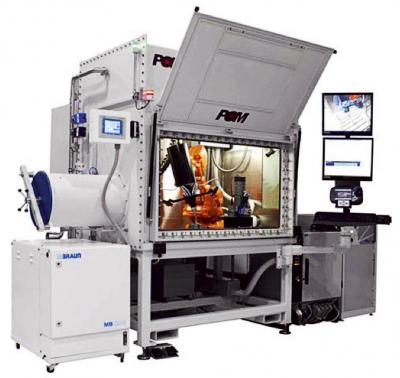
Рис. 3. Аппарат DMD IC106 компании POM
Компания POM (Precision Optical Manufacturing) является разработчиком DMD-технологии и держателем патентов на оригинальные технические решения по лазерным системам и системам управления с обратной связью с одновременным регулированием в режиме реального времени основных параметров построения детали: объема подачи материала, скорости перемещения головки и мощности лазера, которые обеспечивают стабильность и качество рабочего процесса (рис. 3). Эта технология позволяет производить параллельную или последовательную подачу двух видов материала с различными физико-химическими свойствами и таким образом создавать биметаллические компоненты, например формы для литья пластмасс (тело формы из меди, рабочая часть — из инструментальной стали), или наносить специальные покрытия, например на гильзы цилиндров, поршневые кольца, кулачковые валы, седла клапанов.
Технологии производства металлических порошков
В настоящее время не существует общих требований к металлопорошковым композициям, применяемым в AM-технологиях. Разные компании — производители AM-машин предписывают работу с определенным перечнем материалов, обычно поставляемых самой этой компанией. Общим требованием к порошкам для AM-машин является сферическая форма частиц. Это связано с необходимостью компактного укладывания в определенный объем и обеспечения «текучести» порошковой композиции в системах подачи материала с минимальным сопротивлением. На рынке представлены десятки видов разнообразных композиций: от обычных конструкционных сталей до жаропрочных сплавов и драгметаллов. Сфера их применения уже в настоящее время крайне разнообразна — от стоматологии до ювелирной промышленности. Основными технологиями получения порошков для AM-машин являются газовая атомизация, вакуумная атомизация и центробежная атомизация. Согласно технологии газовой атомизации металл расплавляют в плавильной камере (обычно в вакууме или инертной среде) и затем сливают в управляемом режиме через специальное устройство-распылитель, где производится разрушение потока жидкого металла струей инертного газа под давлением. В Европе три компании — ALD (Голландия), PSI — Phoenix Scientific Industries Ltd. (Великобритания) и Atomising Systems (Великобритания) — производят атомайзеры в качестве товарной продукции. При вакуумной атомизации процесс происходит за счет растворенного в расплаве газа. Атомайзер состоит из двух камер — плавильной и распылительной. В плавильной камере создают избыточное давление газа (водород, гелий, азот), который растворяется в расплаве. Во время атомизации металл под действием давления в плавильной камере поступает вверх к сопловому аппарату, выходящему в распылительную камеру, где создают вакуум. Возникающий перепад давлений побуждает растворенный газ к выходу на поверхность капель расплава и «взрывает» капли изнутри, обеспечивая при этом сферическую форму и мелкодисперсную структуру порошка. Технологии центробежной атомизации весьма разнообразны, но наибольший интерес представляют те, которые позволяют получать порошки наиболее ценных для аддитивных технологий сплавов — реактивных и тугоплавких металлов. Единственным сдерживающим фактором развития аддитивных технологий является высокая стоимость расходных материалов (металлических порошков). В настоящее время рядом компаний ведутся работы по внедрению менее затратных технологий производства порошков (в том числе титановых). Прорыв в этом направлении приведет к значительному росту спроса на 3D-устройства, способные воспроизводить металлические модели.
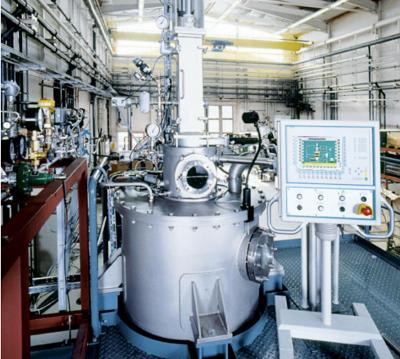
Рис. 4. Атомайзер EIGA 50 компании ALD (Голландия)
Мировым лидером в производстве оборудования для газовой атомизации является компания ALD (в настоящее время входит в группу AMG Advanced Metallurgical Group). Она имеет в своей производственной линейке атомайзеры как лабораторного (объем тигля 1,0–2,0 л), так и индустриального назначения с производительностью до 500 кг за одну плавку и более. Компания ALD является также изготовителем атомайзеров для получения порошковых композиций по технологии EIGA — индукционная плавка с распылением инертным газом. Базовые модели EIGA 50 и EIGA 100 отличаются размерами применяемого фидстока — прутка соответственно 50 и 100 мм. Машины EIGA (рис. 4) имеют невысокую скорость распыления — около 0,5 кг/с, однако позволяют распылять достаточно большой объем материала в течение одной плавки — от единиц до десятков килограммов.
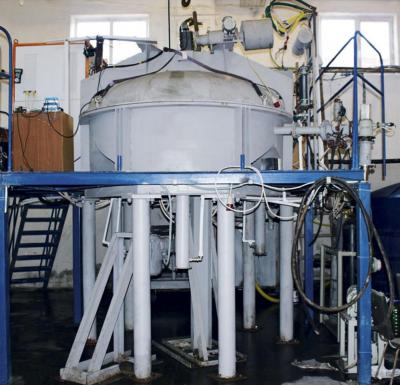
Рис. 5. Установка центробежного распыления расплава ООО «Сферамет»
В России имеется опыт получения порошковых материалов методом центробежного распыления с торца прутковой заготовки, оплавляемой плазменной дугой. Метод был разработан в 1970-х годах в ВИЛСе. В последние годы этот метод получил дальнейшее развитие в работах OOO «Сферамет» (Московская область). ООО «Сферамет» является разработчиком оборудования и технологий нового поколения для получения сферических гранул металлов и сплавов методом центробежного распыления расплава. Исходным материалом для получения гранул на разработанной установке УЦР-6 (рис. 5) служат литые цилиндрические заготовки диаметром 76-80 мм и длиной 700 мм. На этой установке были получены гранулы дисперсностью 50 мкм.
Выпуск металлических порошков для аддитивных технологий в России
Интенсивное использование аддитивных технологий в России сдерживается как отсутствием АМ-машин, так и отсутствием мелкодисперсных металлических порошков. В настоящее время российские предприятия используют импортные порошки, поставляемые в основном компаниями — производителями установок. Серийное производство металлических порошков для аддитивных технологий в России отсутствует. ФГУП «Всероссийский институт авиационных материалов» (ВИАМ, Москва) производит в относительно небольших количествах металлопорошковые композиции для аддитивных технологий. В ближайшее время здесь планируются запуск современного промышленного оборудования и коммерческий выпуск порошков. По мнению генерального директора ВИАМ академика Е.Н. Каблова, для имеющегося российского парка установок аддитивного производства необходимо около 20 тонн порошков в год. По оценкам компании «Инфомайн», этот объем завышен, и общая емкость рынка порошков для работающих установок аддитивных технологий в России составляет на начало 2016 года не более 6–7 тонн. Целый ряд российских компаний занимаются в настоящее время вопросами производства металлических порошков для аддитивных технологий. По оценкам экспертов, уже в 2016 году на отечественном рынке могут появиться прошедшие сертификацию коммерческие металлопорошковые композиции различных марок. В настоящее время ВИАМ самостоятельно обеспечивает себя порошками, однако мощности небольшие (до 2 тонн в год). Движение ВИАМ к производству порошков для аддитивных технологий началось с организации производства припоев для высокотемпературной вакуумной пайки. Требования к порошковым припоям близки к аналогичным требованиям, предъявляемым к металлопорошковым композициям, используемым при аддитивных технологиях, в том числе по сочетанию фракций разного размера. С 2010 года ВИАМ активно ведет работы по созданию производства мелкодисперсных металлических порошков распылением расплава инертным газом на установке ERMIGA10/100VI. Разработаны и освоены технологии получения порошков более 10 марок никелевых и титановых припоев (10–200 мкм). Были начаты серийные поставки припоев моторным заводам. Ведутся работы по получению мелкодисперсных порошков для аддитивных технологий. Порошки для лазерной LMD-наплавки (40–80 мкм) поставляются в ОАО «Авиадвигатель», на котором проводятся работы по отработке технологий наплавки бородок бандажных полок лопаток ТВД. Ведутся работы по получению порошков для селективного лазерного сплавления (20–40, 10–50 мкм).
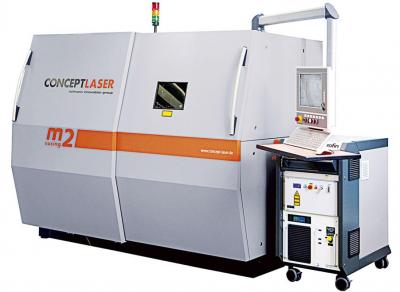
Рис. 6. Установка послойного лазерного сплавления M2 Cusing компании Concept Laser
В 2014 году ВИАМ приобрел установку для селективного лазерного сплавления металлических порошков Concept Laser M2 Cusing (рис. 6), позволяющую получать детали практически любой сложности внутреннего строения напрямую из металлических порошков без использования оснастки. Начаты исследования в области получения деталей по полному циклу, что обеспечит в дальнейшем ускорение внедрения аддитивных технологий в производство. Также в ФГУП «ВИАМ» методом послойного лазерного сплавления на установке M2 Cusing фирмы Concept Laser из порошка ЭП648-ВИ (ВХ4Л) начато изготовление завихрителей для двигателей 100-07, 100-08, 100-09. В рамках НИР по заказу Федерального космического агентства проведены работы, показавшие возможность получения порошков (гранул) на основе никеля и титана для проведения селективного лазерного сплавления.
Аддитивные технологии в «росатоме»: цикл от порошков до применения
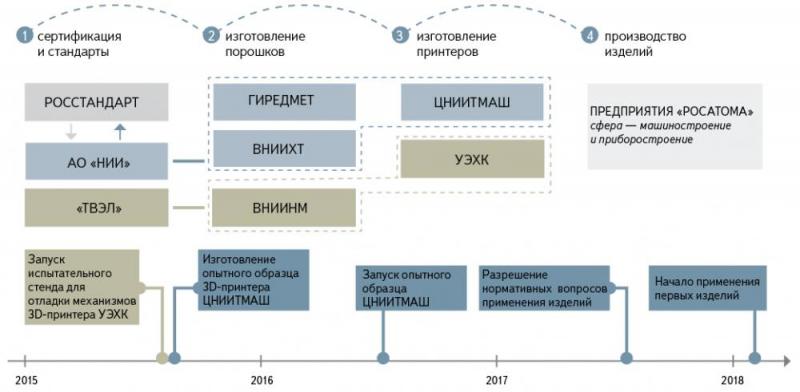
Рис. 7. Дорожная карта развития аддитивных технологий «Росатома»
Импорт в Россию аппаратов для аддитивных технологий
Россия удовлетворяет потребности в 3D-принтерах, работающих на металлических порошках, за счет импорта этой продукции. По данным «Инфомайн», Россия импортировала в 2009–2015 годах 29 установок для аддитивных технологий на металлических порошках на сумму около 12 млн долларов. При этом характерным является тренд на рост импортных поставок (рис. 10). Как видно, 2014 и 2015 годы характеризовались наивысшим уровнем поставок на сумму свыше 200 тыс. долларов.
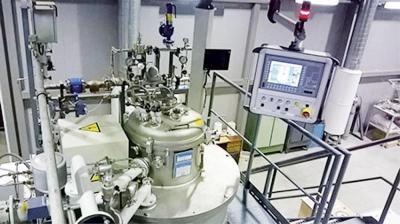
Рис. 8. Атомайзер ALD VIGA-2B
Научный центр порошкового материаловедения (НЦПМ) при Пермском научно-исследовательском политехническом университете (ПНИПУ) приобрел в 2011 году атомайзер ALD VIGA-2B (рис. 8). В апреле 2014 года АМ-машина была запущена. Установка предназначена для исследований и получения небольших экспериментальных партий порошков. Она позволяет распылять все нетугоплавкие металлы и сплавы с температурой плавления до 1700 °C. По словам специалистов Научного центра, порошки получаются сферические, но неоднород-ные — крупностью от 0,5 до 100 мкм.
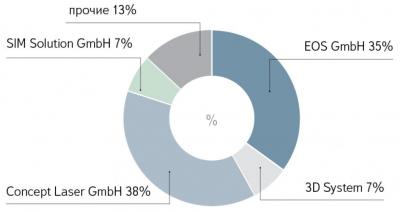
Рис. 9. Структура поставки в РФ 3D-принтеров основными зарубежными производителями в 2009–2015 гг., %
(Источник: «Инфомайн» на основе данных таможенной статистики РФ)
Импорт в Россию металлических порошков для аддитивных технологий
Россия удовлетворяет потребности в металлических порошках для 3D-принтеров за счет импорта этой продукции. По данным компании «Инфомайн», Россия импортировала в 2009–2015 годах 5 тонн металлических порошков на сумму около 1 млн долларов (рис. 11). Преимущественные поставки в натуральном выражении приходились на железные порошки (около 40%). В стоимостном выражении в структуре поставок превалируют титановые порошки — 42%. География поставок ограничена 6 странами, среди которых по объему лидируют Германия и Великобритания.
Основные компании — потребители металлических порошков для аддитивных технологий в России
ОАО «Авиадвигатель» (Пермь) — конструкторское бюро по разработке газотурбинных двигателей для авиации, а также промышленных газотурбинных установок и электростанций на базе авиационных технологий. Предприятие входит в состав ОАО «Объединенная двигателестроительная корпорация» (ОВД). Впервые технологию селективного лазерного спекания (SLS) в компании применили в 2010 году для изготовления литых деталей по выжигаемым полистирольным моделям. В 2013 году началось освоение выращивания металлических деталей по технологии селективного лазерного плавления (SLM). ПАО «НПО «Сатурн» — двигателестроительная компания, специализирующаяся на разработке, производстве, маркетинге, продажах и послепродажном обслуживании газотурбинных двигателей (ГТД) для гражданской и военной авиации, энергогенерирующих и газоперекачивающих установок, кораблей и судов. Предприятие входит в состав АО «Объединенная двигателестроительная корпорация» (ОДК). В 2008 году НПО «Сатурн» приступило к созданию центра аддитивных технологий (ЦАТ), был построен лабораторно-производственный комплекс. С 2014 года ЦАТ осуществляет внедрение аддитивных технологий на предприятии. Совместно с ВИАМ на период с 2016 по 2019 год запланирована разработка коррозионностойких высокотемпературных материалов и масштабируемой технологии полного цикла изготовления ключевых сложнопрофильных высокопрочных деталей ГТД. ЗАО «Новомет-Пермь». Компания создана в 1991 году, ее первой продукцией были ступени погружных центробежных насосов для добычи нефти, впервые изготовляемые по новой для нефтяной отрасли порошковой технологии, обеспечивающей ряд преимуществ по сравнению с традиционными методами. В настоящее время предприятие является одним из крупнейших в России производителей нефтепогружного оборудования. На установках лазерного спекания изготавливают объемные модели основных частей погружных насосов (рабочее колесо и направляющий аппарат). «Центр технологической компетенции аддитивных технологий» (ЦТКАТ, Воронеж) был создан в 2013 году на базе ООО «Воронежсельмаш» при поддержке Министерства экономического развития РФ и Правительства Воронежской области. С помощью федеральных субсидий был приобретен парк 3D-принтеров. Оборудование ЦТКАТ позволяет создавать прототипы, функциональные модели, готовые изделия для аэрокосмической промышленности, радиоэлектроники, медицины, ювелирного производства, легкой и тяжелой промышленности. Центр оказывает услуги по 3D-печати на промышленных аппаратах.
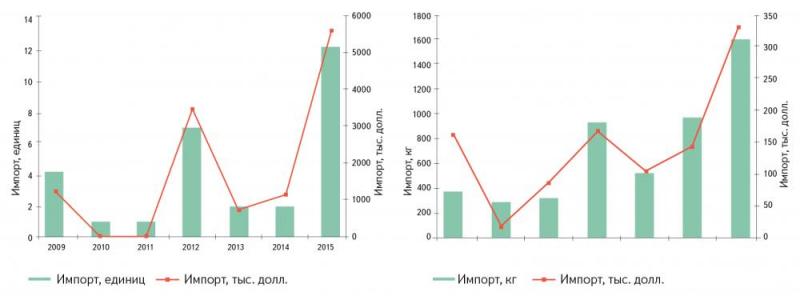
Рис. 10. Динамика импорта в РФ 3D-принтеров для металлических порошков
в 2009–2015 гг.
Рис. 11. Динамика импорта в РФ металлических порошков для аддитивных технологий
в 2009–2015 гг.
(Источник: «Инфомайн» на основе данных таможенной статистики РФ)
Перспективы аддитивных технологий в России
Перспективы рынка аддитивных технологий в России, по оценке экспертов, представляются значительными. Потребность в 3D-принтерах авиастроения, космической техники, судостроения, энергетики и других отраслей оценивается на уровне 300 машин. При этом наиболее востребованы технологии лазерного сплавления/спекания в авиастроении (потенциал рынка — до 240 аппаратов). Наибольшие перспективы в авиационной отрасли имеют селективное сплавление металлических порошков (SLS), лазерная наплавка металлических порошков (LMD), спекание высокотемпературных пластиковых материалов, изготовление деталей из керамических порошков. Технология LMD востребована как для ремонта и упрочнения поверхности детали, так и для создания принципиально новых градиентных материалов/деталей с внутренними силовыми элементами и внешними износо- или жаростойкими покрытиями. Аддитивные технологии могут стать платформой для получения новых прорывных материалов и технологий для перспективных двигателей военной и гражданской авиации, поскольку многие современные сплавы, например для лопаток и дисков ГТД, подошли к пику своего развития. Целый ряд предприятий авиакосмической отрасли достаточно активно применяют аддитивные технологии. Вместе с тем выявлены и систематизированы проблемы развития аддитивных технологий в России. Это отсутствие широкого положительного опыта проектирования изделий и внедрения их в промышленности, отсутствие разработанных и годных к промышленному применению отечественных материалов, начальный уровень разработки отечественного оборудования и программного обеспечения, кадровый вопрос, отсутствие стандартов. Необходима кооперация конечных заказчиков (двигателестроительных, авиастроительных, ракетостроительных компаний), производителей материалов и отечественных производителей серийного технологического оборудования.
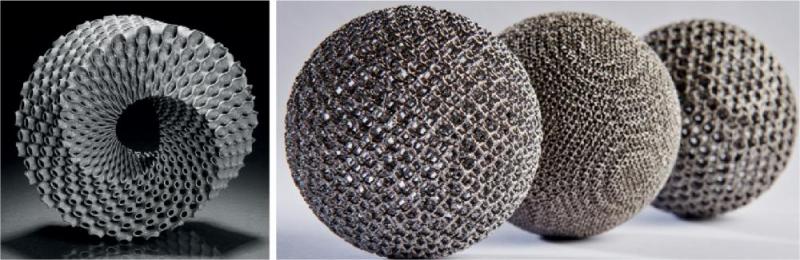
Отдельным направлением является применение лазерных аддитивных технологий для микроэлектроники и приборостроения. По мнению специалистов, в последние годы интерес в западных странах направлен именно в эту сторону, которая представляется направлением будущего роста. Разработкой дорожной карты развития аддитивных технологий занимается специальная межведомственная рабочая группа, которую возглавил руководитель ВИАМ, академик Евгений Каблов. По словам Е.Н. Каблова, «несмотря на все сложности, у отечественной науки и промышленности есть все предпосылки для развития данного направления». Широкое внедрение аддитивных процессов может привести к инновационному развитию и кардинальной трансформации традиционных машиностроительных секторов экономики России, даст толчок новым исследованиям в различных отраслях экономики. В марте 2016 года в ВИАМ прошла Вторая Международная конференция «Аддитивные технологии: настоящее и будущее», где встретились потребители продукции аддитивного производства, пользователи и разработчики принтеров и порошков.
________________________________________
Материал для публикации подготовлен Исследовательской группой «Инфомайн» на основе отчета «Обзор рынка металлических порошков для аддитивных технологий в России»
- 23 апреля 2025 ОТ «ОБОРОНКИ» ДО СПОРТА: КАК СКАНДИЙ МОЖЕТ ПЕРЕВЕРНУТЬ РОССИЙСКУЮ ПРОМЫШЛЕННОСТЬ
- 18 апреля 2025 ОТ ХАЙПА К ДЕЛУ: КАК РАЗВИВАТЬ РЗМ-ИНДУСТРИЮ В РОССИИ
- 9 апреля 2025 ВЫИГРАТЬ ВСУХУЮ: О НОВЫХ ПОДХОДАХ И ТЕХНОЛОГИЯХ В ОБОГАЩЕНИИ ПОЛЕЗНЫХ ИСКОПАЕМЫХ В ЯКУТИИ
- 26 марта 2025 Арктическое пророчество
- 26 февраля 2025 ПОЯВЛЕНИЕ ЖУРНАЛА “РЕДКИЕ ЗЕМЛИ” ОПЕРЕДИЛО ВРЕМЯ НА 10 ЛЕТ - АКАДЕМИК РАН ВЛАДИСЛАВ ПАНЧЕНКО
- 14 февраля 2025 Редким землям России нужен ТРАМПлин
- 6 февраля 2025 РЕДКИЕ ЗЕМЛИ ЗА СТОЛОМ ПЕРЕГОВОРОВ
- 3 февраля 2025 РАЗДЕЛЯЙ И ЗАРЯЖАЙ
- 26 января 2025 ВЛАДИМИР ВЕРХОВЦЕВ ОТМЕЧАЕТ 70-ЛЕТИЕ
- 27 декабря 2024 МЕЖДУ МИРОМ И ВОЙНОЙ: ЯДЕРНОЕ ОРУЖИЕ ДЛЯ РАЗРУШЕНИЯ И СОЗИДАНИЯ
- 27 октября 2024 ДЛЯ ГЛАВНОЙ НАУКИ БУДУЩЕГО ЧЕЛОВЕЧЕСТВО ДАЖЕ НЕ ПРИДУМАЛО НАЗВАНИЕ
- 13 октября 2024 Форум «Микроэлектроника 2024» – без высокочистых редких металлов никуда
- 23 сентября 2024 ОТ ВОЗРОЖДЕНИЯ МАГНИТНОГО ПРОИЗВОДСТВА К СОЗДАНИЮ НОВОЙ ИНДУСТРИИ В РФ
- 14 сентября 2024 "Задачи будут решены" – О беспилотниках из первых рук
- 31 августа 2024 ВИКТОР САДОВНИЧИЙ: «ЕСЛИ БЫ НЕ МОСКОВСКИЙ УНИВЕРСИТЕТ, РОССИЯ БЫЛА БЫ ДРУГОЙ»