Редкоземельные новости России

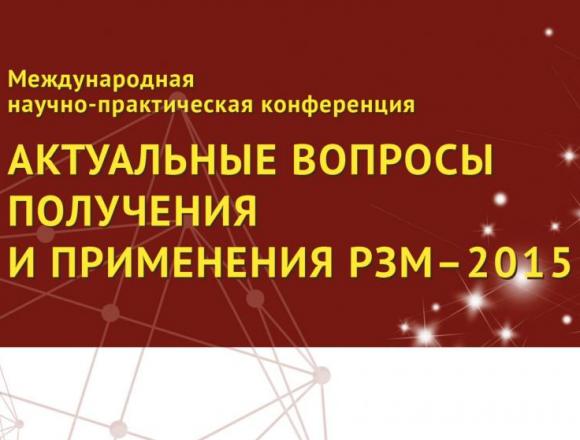
С приветствием к участникам обратились: председатель конференции профессор А.В. Тарасов, генеральный директор «РТ-глобальные ресурсы» А.В. Коробов и начальник отдела развития цветной металлургии и промышленности редких и редкоземельных металлов Минпромторга России С.И. Гришаев. Проведение конференции было поддержано Минпромторгом РФ и Госкорпорацией «Ростех». Информационными партнерами выступали журналы «Редкие земли», «Цветная металлургия», «Цветные металлы» и другие специализированные издания. Структура конференции 2015 года отличалась: 1) анализом мировых цен на РЗМ по различным зарубежным источникам и прогнозом их изменения на перспективу до 2020 года; 2) преобладанием информационных докладов о технологических способах и реализуемых схемах глубокой переработки реальных видов природного и техногенного редкометально-редкоземельного сырья с получением индивидуальных РЗМ; 3) оценками основных направлений и масштабов применения РЗМ в металлургии. В меньшей степени было уделено внимание нетрадиционным источникам РЗМ, аналитическим методам и возможностям извлечения скандия как спутника иттрия
из различных сырьевых источников.

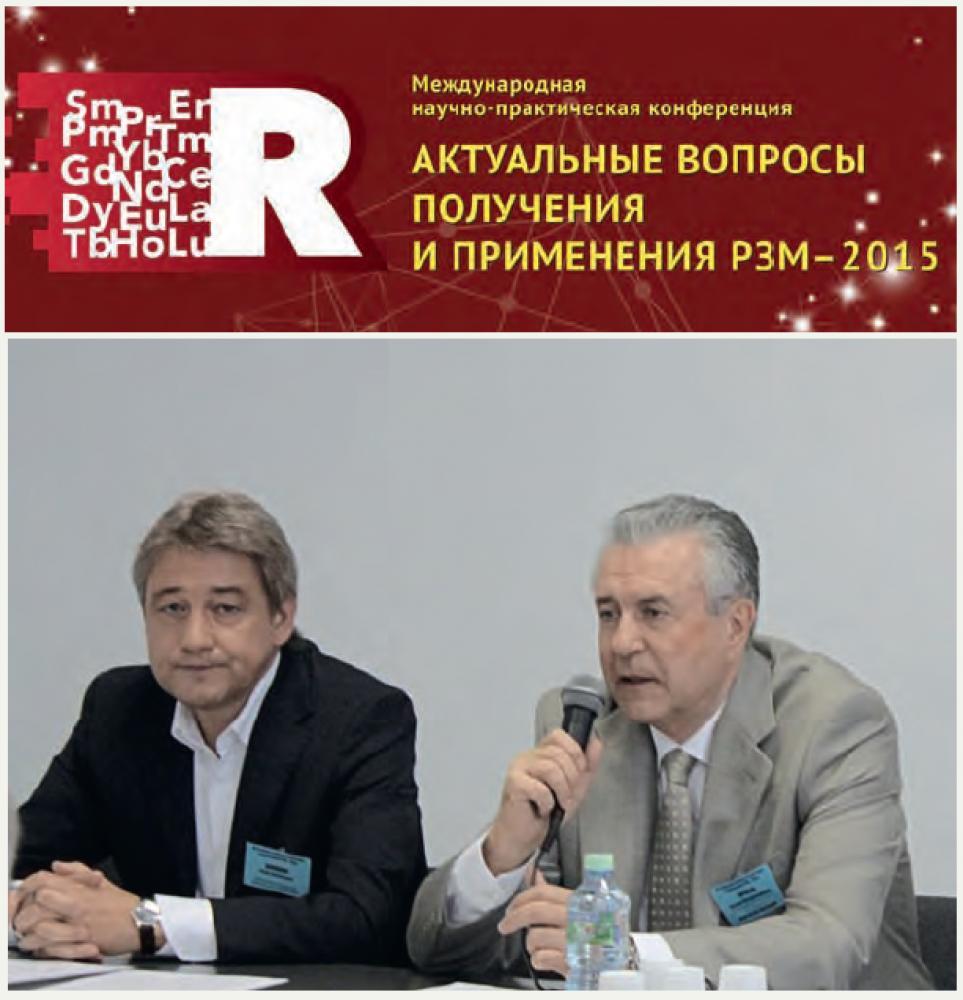
Структура мирового производства, потребления и цен РЗМ
В докладах фирм «Инфомайн» и «Металлургические исследования» показаны существенные различия в стоимости легких и среднетяжелых РЗМ. Преобладающее производство и потребление первых из них обусловливает низкие биржевые цены (долл./кг) на оксиды церия (4,4) и лантана (4,8) более высокие цены на их спутники — Nd (59) и Pr (175), в то время как цены на Dy (340), Tb (600) и Eu (680) несоизмеримо выше. Эти различия обусловлены как высокой себестоимостью производства иттриевоземельных лантаноидов, так и повышенным спросом на них со стороны инновационных высокотехнологичных отраслей промышленности. Заметим, что церий выпускается преимущественно в виде карбоната (65%), лантан — в виде оксида (75%), а Nd, Dy, Sm — в виде металлов.
Потребление церия в мире составляет 45 тыс. т, лантана — 30 тыс. т, неодима — 20 тыс. т и иттрия — 12 тыс. т, что в сумме составляет 87–88% от общего потребления РЗМ в мире. В последние годы резко (на 23%) увеличилось использование Nd, Pr, Dy в производстве магнитов. Обращает на себя внимание стоимость наиболее дорогих оксидов иттриевых лантаноидов, иттрия и особенно скандия, что определяет необходимость геохимической оценки содержаний последнего во всех видах иттрийсодержащего сырья.
На волне интереса к редкоземельным металлам в Лондоне в 2012 году открылась биржа Rare Earth Metal Exchange Ltd. В том же году в Баотоу — китайском редкоземельном центре — была создана первая в Китае биржа по торговле РЗМ. Цены китайской биржи приведены в таблице 1.
Согласно прогнозным оценкам исследовательской группы «Инфомайн», мировое потребление РЗМ к 2020 году достигнет 180 тыс. т, из них 120 тыс. т будет потребляться в самом Китае и лишь 2,7% — в России. С учетом необходимости импортозамещения в производстве и потреблении РЗМ и инновационного развития экономики в нашей стране указанные объемы использования РЗМ в выпуске магнитов, автокатализаторов, поляритов, стекольно-керамических производствах (таблица 2) и особенно в металлургии не могут считаться достаточными для обеспечения ее экономической и национальной безопасности. Тем более что пока горнотехнологическим комплексом «Ловозеро — Соликамск» выпускаются только карбонаты и хлориды РЗМ, что требует решения важнейшей задачи технической модернизации производств этого действующего комплекса под эгидой Госкорпорации «Ростех».
В настоящее время согласно мировой практике ценность редкоземельного сырья преимущественно определяется соотношением в нем цериевых и иттриевых лантаноидов: в рудах Актюза, например, это соотношение является оптимальным (1:1), а в остальных ≥ 4:1. Дефицитность иттриевоземельного сырья на мировом рынке обусловливает необходимость его поисков, оценки и ускоренного промышленного освоения, а также существенные различия в стоимости конечной химико-металлургической продукции.
Редкие земли в металлургии
Эффективная роль редкоземельных элементов в качественном совершенствовании металлургических процессов и выпуска металлопродукции, включая чугуны, стали, сплавы и лигатуры, широко используется за рубежом (США, Япония, Германия) и в значительно меньшей степени — в нашей стране. В то же время доклады специалистов Института ферросплавов и техногенного сырья им. академика Н.П. Лякишева при ФГУП «ЦНИИчермет им. И.П. Бардина» свидетельствуют о существенном вкладе российских ученых в решение технологических проблем внедрения РЗМ в металлургию. Применение РЗМ обеспечивает значительное увеличение глубины раскисления сталей и улучшение их технологических, физико-механических и эксплуатационных свойств.
В частности, исследовано положительное влияние РЗМ на свойства высокопрочных конструкционных сталей за счет их сверхглубокой десульфидизации до уровня содержания серы 0,0005%. Установлено, что по сродству к сере РЗМ превосходят все традиционные раскислители (Ba, Sr, Ca). В настоящее время лимитируемые содержания серы в сталях составляют не более 0,001%, азота — 0,005%, водорода — 2 ppm. Микролегирование редкоземельными металлами оказывает положительное влияние на свойства жаропрочных сталей и сплавов, применяемых в теплоэнергетических установках нового поколения, в производстве быстрорежущей стали, повышает жидкотекучесть нержавеющей стали при увеличении ее плотности и пластичности, обеспечивает эффективность электросварки и т. д. Модифицирование церием, ферроцерием или мишметаллом легированных (например алюминиевых и высокохромистых) чугунов повышает их прочность и износостойкость. Введение лантановых, цериевых и иттриевых лигатур в количестве 3–5 кг/т приводит к перерождению структуры белого чугуна в структуру, характерную для карбидных сталей. При этом износостойкость модифицированного чугуна в абразивной среде повышается в 2–3 раза.
К сожалению, объем применения РЗМ в качественной черной металлургии России пока остается ниже показателей зарубежных стран, включая Китай. Улучшение сложившейся ситуации представляется возможным, в частности, за счет замены редкоземельных добавок-модификаторов технической чистоты, получаемых дорогим электрохимическим методом, дешевыми лигатурами с широким диапазоном составов, содержащих, помимо РЗМ и кремния, Ca, Mg, Al, Cu, B, Zr, V и другие легирующие компоненты. При этом усвоение РЗМ в жидкий металл из лигатур в 2–3,5 раза выше, чем при модифицировании его сплавами электрохимического производства.
В полупромышленных условиях в ЦНИИчермет им. И.П. Бардина получены лигатуры с содержаниями до 40% индивидуальных РЗМ — La, Ce, Nd, Pr, Sm, Gd, Y и др. при извлечении этих металлов и ∑TR до 80%. Для выплавки редкоземельных лигатур разработана двухстадийная металлотермическая плавка с использованием в качестве восстановителей силикокальция марки СК30 и ферросилиция марки ФС75 в смеси с алюминием. На первой стадии осуществляется плавка оксидного сырья (концентрата цериевой группы) с известью, а на второй — восстановление металла из жидкого шлака, содержащего 20% РЗМ. Извлечение в сплав составило 50–60%. Инновационная безотходная технология, разработанная в ЦНИИчермет им. И.П. Бардина, позволяет получать комплексные сплавы РЗМ из отвальных шлаков путем их довосстановления. Разрабатываются технологии введения РЗМ в сталь в виде порошков, безопасной разливки, измельчения, сплавов РЗМ и т. д. Изыскиваются способы повышения экономической эффективности использования РЗМ в металлургии.
Использование РЗМ может обеспечить уникальность получения и применения новой металлопродукции как в черной, так и цветной металлургии, что должно учитываться в расчетах и прогнозах ожидаемой потребности России в РЗМ на ближайшую перспективу и на 2020–2030 годы, в том числе с учетом сложившихся конкурентных преимуществ Китая, Японии и других стран Юго-Восточной Азии в производстве РЗМ и высокотехнологичной продукции.
Инновационные технологии извлечения РЗМ из природного и техногенного сырья
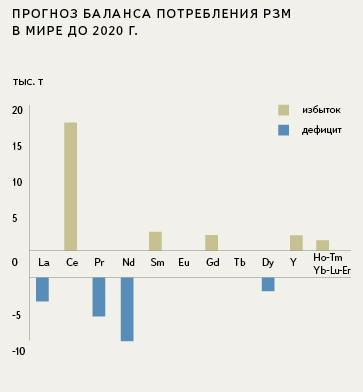
Несомненным лидером в разработке инновационной экстракционно-каскадной технологии переработки фосфогипса с извлечением индивидуальных РЗМ среднетяжелой группы и получением обезвреженного техногенного гипса как дефицитного компонента стройматериалов является ООО «ЛИТ» группы компаний «Скайград». За период после предыдущей конференции, где были доложены результаты создания технологической линии с автоматизированным управлением и демонстрировались опытные образцы полученной конечной продукции, специалисты ООО «ЛИТ» расширили диапазон своих НИР и НИОКР включением в них задач по извлечению Nd, Sm, Eu, Gd, Tb, Dy, Ho, Eb и иттрия из растворов группового редкоземельного концентрата (ГРЗК) среднетяжелой группы, получаемого ОАО «СМЗ», а также из раствора переработки (рециклинга) магнитов. Была изучена эффективность использования различных экстрагентов, среди которых наиболее продуктивным оказался Cyanex-572 (США). Его смесь с ГБФ и разбавителем (нефтяной жидкостью РЭД-ЗМ) обеспечила максимальные коэффициенты разделения Dy-Sm (6,4) и Dy-Gd (4,8) при концентрации HNO3 в исходном растворе ph-1 и составе экстрагентов (%, об.) 30 Cyanex-572 + 70 РЭД-ЗМ. Изотермические параметры процессов экстракции и реэкстракции позволили рассчитать разделительный каскад для среднетяжелых РЗМ для Tb/Gd, состоящий из 53 ступеней, включая 16 экстракционных, 17 — промывки, 10 — реэкстракции, 10 — регенерации экстрагента. В течение 25 часов работы каскада содержание тяжелых РЗМ в рафинате экстракции снизилось с 5,57 до 0,1%. Экстракционная фосфорная кислота, в отличие от фосфогипса, обеднена La и Ce, но обогащена Nd и Pr и, главное, иттриевыми лантаноидами СТГ — Sm, Eu, Gd, Tb, Dy, Er (в 2–3 раза) и иттрием (в 5,5 раза).
В докладе от Национального минерально-сырьевого университета «Горный» (Санкт-Петербург) приведены результаты определений в лабораторных условиях коэффициентов разделения Nd и Er — 334,3, Nd и Yb — 1965,5, Er и Yb —5,9 из растворов ЭФК концентрацией 5,780 моль/кг. Такие высокие коэффициенты разделения позволяют эффективно отделять группу легких РЗМ от среднетяжелых, причем извлечение последних и иттрия из продукционной ЭФК на первой ступени экстракции составляет 90%, а из оборотной на ООО «БМЦ» — не менее 70%.
В ИХТЦ "Русредмет" (Санкт-Петербург) разработана сорбционно-экстракционная технология извлечения РЗМ непосредственно в производственном процессе ОАО «ФосАгро-Череповец». Она включает коллективную ионообменную стадию, вторую экстракционную очистку и разделение на групповые концентраты. На опытно-промышленной установке производительностью 12 т РЗМ/год были опробованы все стадии технологии и наработана партия редкоземельной продукции объемом 3 т. В 2014 году с выводом установки на проектную мощность впервые в практике промышленной переработки апатита была получена партия оксидов РЗМ объемом около 9 т, а ЭФК возвращена в цепочку производства удобрений. Разрабатываются исходные данные для проектирования производства РЗМ мощностью 200 м3 ЭФК/час и оцениваются необходимые контрольные затраты. Доклад французской компании «Солвей» свидетельствует о том, что за рубежом проблема получения редкоземельной продукции, как коллективной, так и индивидуальной, из фосфатного сырья была решена на уровне лабораторных исследований и опытно-промышленных испытаний еще в 1980-х годах. Однако расчеты некоторых специалистов, ориентированные на решение проблемы развития производства РЗМ до 28–34 тыс. т/год за счет их сопутствующего извлечения в процессе сернокислотной переработки хибинского апатита представляются нереальными. Во-первых, из ЭФК возможно извлечение лишь 15–20% РЗМ, содержащихся в исходном фосфатном сырье. Во-вторых, извлечение РЗМ из фосфогипса может быть организовано в ближайшей перспективе только «с колес», так как накопленный лежалый фосфогипс представляет собой весьма неоднородный по составу и качеству техногенный ресурс, требующий специальной оценки методами детального минералого-геохимического и технологического картирования вплоть до разведки с утверждением запасов оцененного сырья на весь комплекс полезных компонентов. В-третьих, объемы переработки корпорацией «Акрон» апатита альтернативным азотнокислотным методом составляют 15% от суммарного объема его добычи и переработки. При этом следует заметить, что уже на двух конференциях ОАО «Институт «ГИНЦВЕТМЕТ» отсутствует какая-либо информация о результатах опытно-промышленных испытаний установки по извлечению РЗМ на азотнокислотном производстве минеральных удобрений заводом в Великом Новгороде.
Cоздание какого-либо одного центра по извлечению РЗМ из фосфатного сырья, продуктов и отходов его переработки представляется нереальным и нецелесообразным. Уже сейчас естественным образом сложились два новых научно-производственных центра в г. Королеве («Скайград») и г. Череповце («ФосАгроЧереповец» и «Русредмет»). Кроме того, в НИЯУ МИФИ проводятся исследования по разделению РЗМ в нитратной и азотнокислотной среде с учетом опыта работы экстракционных установок Московского завода полиметаллов (МЗП). Технология включает разделение РЗМ на группы экстракцией из нитратных растворов с использованием ТБФ без высаливателя. Разделение легких РЗМ цериевой группы предусматривает получение оксидов La, Ce, Pr, Nd чистотой 99,9–99,99%. Разделение иттриевых среднетяжелых РЗМ осуществляется экстракцией из азотнокислотных растворов алкило-фосфорными или алкило-фосфоновыми кислотами. При этом получают наиболее востребованные оксиды Sm, Eu, Gd, Dy, Tb, Er и иттрия. С 1981 года в течение 10 лет на МЗП впервые в РФ был создан и эксплуатировался каскад из 70 центробежных экстракторов, на котором извлекался самарий. К настоящему времени более совершенная технология выделения тербия последовательной экстракцией внедрена на МЗП. Разрабатываемая в НИЯУ МИФИ новая технология разделения цериевых и иттриевых концентратов включает осаждение РЗМ из растворов гидрооксидом или карбонатом аммония из маточных растворов, полученных от фильтрации азотсодержащих удобрений.
Продолжает свою деятельность главный промышленный производитель РЗМ — горно-технологический альянс ОАО «Ловозерский ГОК» — СМЗ и начато промышленное освоение Томторского супергиганта в Республике Саха (Якутия). С другой стороны, не исключаются возможности ускоренного создания новых производств иттриевых лантаноидов и иттрия на базе небольших легкодоступных месторождений и вовлечение в промышленное использование техногенного и россыпного монацита.
С созданием ЕвразЭС появляются новые перспективы восстановления и развития межгосударственных научно-производственных комплексов по выпуску индивидуальных РЗМ (Россия и Казахстан) и преимущественно иттриевых лантаноидов и иттрия (Россия и Кыргызстан). В этих целях, при условии проявления политической воли заинтересованных государств, может и должна быть создана инициативная рабочая группа специалистов для подготовки проекта решения этой геоэкономической и геополитической проблемы к следующей редкоземельной конференции в 2016 году.
От АО «Центр наук о земле, металлургии и обогащения» (ИНЗМО, г. Алматы) на конференции были представлены два доклада: первый — о технологических возможностях переработки фосфогипса с получением, помимо кондиционного концентрата РЗМ, ряда сопутствующих товарных продуктов — сульфата натрия, гидрооксида кальция, нитрата аммония, и второй — о перспективах извлечения индивидуальных РЗМ из фосфорных шлаков. В обоих случаях исследования выполнены на пробах техногенных образований ТОО «Казфосфат» с содержаниями 3,2 кг/т РЗМ в фосфогипсе и 536,48 г/т в шлаке с преобладанием Y, Nd, Gd над La и Ce. Особое внимание привлекает доказанная технологическая возможность и высокие показатели извлечения РЗМ (около 99%) в фильтрат после азотнокислотного выщелачивания шлака, включая иттрий (кроме La и Sc).
В обзорном докладе специалистов ОАО «ГИРЕДМЕТ» выделено три традиционных метода промышленного получения редкоземельной металлопродукции в соответствии с классификацией РЗМ по их физико-химическим свойствам. Для получения легкоплавких (<1000 ˚С) металлов 1-й группы — La, Ce, Pr и мишметалла преимущественно используются электрохимические методы, 2-й группы — иттриевых лантаноидов, начиная с гадолиния и включая иттрий (кроме иттербия и тулия) с температурами плавления 1400 ˚С, основным методом является кальциетермическое восстановление из фторидов. РЗМ 3-й группы (Sm, Eu, Yb, Tm) характеризуются низкими температурами кипения и образованием устойчивых двухвалентных соединений, что позволяет восстанавливать их из оксидов карботермическим или лантанотермическим методами. В этих целях в промышленных условиях использовались дуговые печи. Высокие температуры кальциетермического восстановления иттриевых лантаноидов из фторидов обусловили развитие в ГИРЕДМЕТе технологий получения безводных хлоридов РЗМ и литиетермического восстановления. Производительность опытно-промышленной установки составила 100 кг металла за цикл при снижении себестоимости продукции примерно на 20%. Подобным же образом, за счет использования хлорида, была значительно снижена температура кальциетермического восстановления и получения неодима — до 1100 ˚С, что открывает новые конструкционно-технологические перспективы получения этого металла, всё шире используемого в производстве магнитов.
Принципиально новыми разработками ГИРЕДМЕТа являются: технология получения водородопоглотильных сплавов с повышенной на 20% водородостойкостью и создание более эффективных составов водородопоглотителей, в том числе для топливных элементов подводных лодок. На опытно-производственном участке получено около 2 т водородопоглотительного сплава.
Несомненный интерес представляют сообщения ряда участников конференции об использовании синергетического эффекта при комбинировании различных технологических методов в целях получения индивидуальных РЗМ высокой чистоты (Ce, La, Eu и др.). В частности, в докладе О.В. Юрасовой с соавторами (АО «ГИРЕДМЕТ») показана эффективность сочетанного, последовательного применения электрохимического и экстракционного методов для получения церия чистотой 99,9% из модельных и промышленных редкоземельных концентратов ОАО «СМЗ» с использованием традиционного экстрагента ТБФ, разбавленного до 80%, и 6-кратной промывки. Реэкстракция Ce после промывки органической фазы осуществлялась раствором HNO3 и пероксида водорода. Необходимо заметить, что за рубежом, включая ТОО «Снарк» (бывший Иртышский ХМЗ в Казахстане), в промышленных масштабах производится процесс электрохимического окисления катионов Ce+3 в Ce+4 с последующим их разделением жидкостной экстракцией и выделением четырехвалентного церия ионным обменом или осаждением.
Техноэкологические возможности получения РЗМ из нетрадиционного сырья
Среди докладов конференции привлекли внимание сообщения об инновационных технологических разработках способов глубокой и комплексной переработки таких нетрадиционных видов редкометально-редкоземельного сырья, как богатые руды переотложенной коры выветривания карбонатитов Томторского месторождения, легкодоступные и практически неограниченные ресурсы иттриевоземельных (c Zr, Hf, Ta и другие редкие металлы) эвдиалитовых руд Ловозера (ОИВТ РАН) и горючие сланцы месторождений Байсун и Сунгунтау в Узбекистане (Институты геологии и геофизики, общей и неорганической химии АН РУЗ), характеризующиеся повышенными содержаниями Мо, благородных металлов и РЗМ, а также техногенные ресурсы РЗМ и скандия. Результаты технологических исследований специалистов ИХХТ (г. Красноярск) и ВИМСа, выполненных в период разведки участка Буранный на Томторе, а также инновационно-технологической разработки специалистов ОИВТ РАН, доложенные на конференции, свидетельствуют о возможностях использования альтернативных гидрохимических и пирохимических методов в решении проблемных задач глубокой переработки комплексного томторского сырья.
Минералого-технологическими исследованиями ВИМСа установлено, что богатые редкометально-редкоземельные руды переотложенной коры выветривания карбонатитов являются сложным объектом для традиционного механического обогащения в связи с высокой дисперсностью (выход класса –20 мкм составляет 77–85%) и неразделимыми сростками основных рудных минералов — пирохлора, монацита, крандаллита, минералов-концентраторов Fe, Ti и др. Поэтому была разработана базовая гидрохимическая схема глубокой и комплексной переработки томторского сырья, представляющего собой фактически черновой концентрат ниобия, фосфора, РЗМ, иттрия и скандия. Эта схема включает стадии щелочной обработки с извлечением в раствор фосфора, азотнокислотное выщелачивание кека для растворения гидрооксидов РЗМ и перевода ниобия в нерастворимый остаток (40–42% Nb2O5) и, наконец, переработку азотнокислотного раствора с предварительным выделением скандия с ураном и торием и получением соединений РЗМ, иттрия (6,22% Y2O3)и скандия с извлечением 87–98%.
Альтернативная пирохимическая технология ОИВТ РАН предусматривает создание короткой схемы переработки богатой и рядовой томторской руды с использованием в качестве ключевого механизма ликвации — расслоения расплава рудной шихты с добавками-флюсами на две несмешивающиеся жидкие фазы, представляющие собой плавленые концентраты: верхний ниобиевый железисто-силикатный и нижний редкоземельный фторидно-фосфатно-карбонатный слои. По результатам эскпериментальных плавок составлена диаграмма состояния системы для пяти изотермических сечений: 850, 900, 1000, 1100 и 1200 ˚С. Установлено, что поле ликвации значительно расширяется с увеличением температуры. Извлечение РЗМ в солевой слой составляет 80–85%. Краткий обзор результатов применения ликвационной плавки к избирательному обогащению различного редкометалльного сырья, продуктов и отходов его переработки свидетельствует о высокой эффективности такого процесса вскрытия минеральных фаз, избирательного концентрирования и извлечения редких и редкоземельных металлов. Очевидно, что этот инновационный метод заслуживает необходимого внимания со стороны «Ростеха» и предприятий как крупного, так и малого горно-технологического бизнеса, поддержка которых необходима для создания пилотных и опытно-промышленных установок с авторским технологическим сопровождением. В качестве модели приводится схема комбинированной технологии комплексной переработки редкометально-редкоземельного сырья Томтора с получением конечной феррониобиевой продукции.
К сожалению, на конференциях 2014 и 2015 годов не была представлена информация о перспективах вовлечения в промышленное использование редкометально-иттриевоземельного эвдиалитового сырья Ловозера. Легкодоступные ресурсы этого сырья согласно многолетним исследованиям и оценкам специалистов ИМГРЭ, включая автора настоящего обзора, ИХТРЭМС КНЦ РАН, ГИРЕДМЕТ и геологов-разведчиков, являются легкообогатимыми, предназначены для многоцелевого использования и представляются практически неисчерпаемыми. В известной степени они могут рассматриваться в качестве альтернативного источника иттриевых лантаноидов и иттрия вместо утраченных с распадом СССР промышленных производств этих элементов в Киргизии (Актюз) и Казахстане (Прикаспийский ГМК). Примечательно, что концентрации в эвдиалите наиболее ценных иттриевых лантаноидов превосходят их содержания даже в рудах Томтора, специализированных на иттрий и скандий. Кроме того, для них характерны крайне незначительные содержания тория и урана, то есть практически отсутствует экологически лимитируемая природная радиоактивность (таблица 1).
Эвдиалитовые руды слагают месторождения в приводораздельной части Ловозерского массива, что обусловливает возможности их добычи открытым способом и доставки к железной дороге. Тем самым значительно сокращаются издержки, неизбежные при подземной добыче лопаритовых руд, доставляемых рудничным транспортом на дневную поверхность. Снижаются и геоэкологические риски. Эвдиалит, в отличие от мелковкрапленного лопарита в мелкозернистых и сливных уртитах, представляет собой породо- и рудообразующий минерал луявритов и ювитов с содержаниями в этих породах до 20–30%, что обеспечивает высокую обогатимость эвдиалитовых руд гравитационно-магнитной сепарацией с извлечением эвдиалита в концентрат на 75–80%. Принципиально важной является повышенная ценность эвдиалитовых ювитов, которые в отличие от луявритов содержат сопутствующий лопарит, обогащенный относительно традиционно добываемого лопарита танталом в 1,5–2 раза (до 1,3% Та2О5 и 12,9% Nb2О5).
Технология обогащения этих руд позволяет получать в магнитной фракции эвдиалит и эгирин, а в немагнитных хвостах — нефелин-полевошпатовый продукт. После сушки из коллективного магнитного концентрата электромагнитной сепарацией получают селективные эвдиалитовый (непроводящий) и эгириновый (проводящий) концентраты. Высокая рентабельность производства конечной химико-металлургической продукции из эвдиалита, согласно оценкам ГИРЕДМЕТа, может быть обеспечена объемами ежегодной добычи и переработки 1 млн т руды с получением 187,5 тыс. т эвдиалитового концентрата. Технология глубокой и полной химической переработки легкорастворимых эвдиалитовых концентратов кислотными методами разработана в различных вариантах ВНИИХТом, ГИРЕДМЕТом, ИХТРЭМСом КНЦ РАН и РХТУ им. Д.И. Менделеева. В зависимости от применяемых реагентов из эвдиалита получены различные комплексы товарных химических продуктов при ведущей роли иттрия, ассоциирующих с ним РЗМ среднетяжелой группы и тантала.
С техноэкологических позиций оптимальной, согласно исследованиям О.А. Аржаткиной, представляется сернокислотная технология ВНИИХТ, ранее разработанная (2000–2001 гг.) применительно к переработке лопаритовых концентратов непосредственно на месте их производства, то есть на территории Ловозерского ГОКа. На первом этапе переработки 10 тысяч тонн эвдиалита в год можно получать 0,66 кг Gd, 0,63 кг Dy и 0,3 кг Eu для удовлетворения потребностей Чепецкого механического завода в г. Глазове в Удмуртии. Создание полного цикла комплексной переработки того же количества эвдиалита позволит получать 3 т Er, 6,3 т Dy, 7 т Та2О5, 70 т Nb2O5, 890 т Zr2O в год, что соответствует (Еr) годовым потребностям промышленности 2000-х годов или превышает (Dy) их. На втором этапе при переработке 50–100 тыс. т эвдиалита прогнозируется выпуск широкого ассортимента индивидуальной редкоземельной и высоколиквидной редкометальной продукции, включая цирконий, гафний, тантал и др., а также аморфного кремнезема и целого ряда промежуточных побочных продуктов — Si-Zr-, Fe-Zr- и марганцевых кеков, сульфатов, хлоридов натрия и т. д.
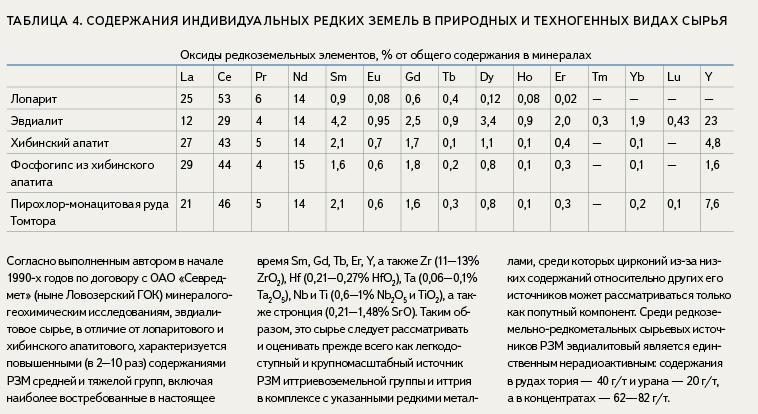
Среди новейших химико-технологических разработок необходимо отметить экспериментально доказанные возможности разложения эвдиалита разбавленными кислотами вместо концентрированных, включая серную, экстракционного разделения и извлечения РЗМ и циркония, применения в этих целях новых реагентов [Литвинова Т.Е., 2015]. Не менее перспективными являются технологические возможности использования легкоплавкого и нерадиоактивного эвдиалита в производствах льющихся глазурей и эмалей, специальных стекол, сварочных флюсов, обмазок для электродов, а также в качестве добавок в производствах модифицированных чугунов и сталей, спецсплавов и электродов. В перспективе возможно использование эвдиалита в производствах металлокерамики и сверхпроводящих материалах. Согласно расчетам, по достижении проектной мощности производства эвдиалитового концентрата в 187,5 тыс. т/год при капитальных затратах порядка 140 млн долл. прибыль для сернокислотной схемы составит 35 млн долл. при окупаемости за 4,5 года и рентабельности 22%. С изложенных позиций представляется целесообразным оценивать гигантские ресурсы ловозерского эвдиалитового сырья в качестве альтернативы приостановленному с 1995 года производству иттриевоземельной продукции Актюзским ГОКом и Киргизским ГМК, а также учитывать ряд конкурентных преимуществ рекомендуемого поэтапного освоения лопарит-эвдиалитовых руд с использованием базы действующего Ловозерского ГОКа. Необходимо отметить, что за рубежом эвдиалитовые концентраты Гренландии давно являются товарным продуктом: в начале 2000-х годов их стоимость составляла 28–50 долл./т.
В металлорудных горючих сланцах месторождений Узбекистана докладчиками установлены повышенные содержания (г/т) La (до 114,4), Ce (103,9), Nd (78,6), Pr (13,0) и среднетяжелой группы — Sm (до 19,5), Gd (30,1), Dy (36,2), Er (13,5), Yb (23) и др. Наиболее высокие содержания характерны для иттрия (до 329,0 г/т). Эти данные ориентируют на подобную же оценку горючих сланцев России в пределах субмеридианального пояса в Европейской части и субширотного — на севере Восточной Сибири.
Нетрадиционные техногенные месторождения РЗМ прежде всего представлены шлакозольными отходами (ШЗО) угольных ТЭС, среди которых выделяются ШЗО Ангренской ТЭЦ в Узбекистане, содержащие (г/т) в отдельных пробах La (150), Yb (100) и, главное, до 1 кг/т иттрия. С ними ассоциируют Au (0,2–10) и Ag (2–20), Ge (10–100),
Mo (50–100), Cu (500), Zn (2 кг/т) и Pb (кг/т), а также, возможно, Re, In, Cd и другие рассеянные редкие металлы. Установлено, что себестоимость их извлечения из ШЗО на 60% меньше, чем из традиционного промышленного сырья.
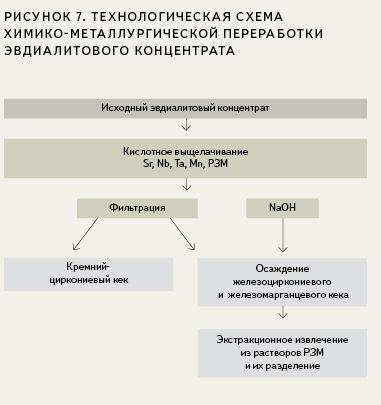
Особый интерес представляют техногенные ресурсы, содержащие скандий. В докладе от Института химии твердого тела УрО РАН обсуждается проблема использования красных шламов (КШ) как объемного отхода переработки бокситов на глинозем в качестве промышленного источника скандия. Ежегодно в мире накапливается 150 млн т КШ с содержаниями до 120–150 г/т Sc2O3, которые в сотни раз выше его содержаний в растворах подземного выщелачивания урана, используемых для извлечения скандия. Новая технология, разработанная авторами доклада, основана на способности скандия образовывать растворимые карбонатные комплексы. В производственных условиях при получении глинозема карбонатизация осуществляется отходящими газами, в результате чего каустическая щелочь шламовой пульпы преобразуется в карбонатную и гидрокарбонатный раствор, содержащий ≥50 мг/дм3 Sc2O3. Получен первичный скандиевый концентрат с содержанием 5% Sc2O3. Эта технология внедряется ООО «Техногория» в опытно-промышленном масштабе на территории ОАО «БАЗСУАЛ». Не менее перспективным источником скандия представляются силикатные отходы (хвосты) мокрой магнитной сепарации процесса обогащения титаномагнетитового сырья на Качканарском ГОКе.
В докладе РХТУ им. Д.И. Менделеева и ООО «Инредтех» изложена двухстадийная технология получения оксида скандия высокой чистоты с указаниями основных параметров его извлечения из силикатной «матрицы». На первой стадии осуществляется механоактивация хвостов и выщелачивание серной кислотой с последующим получением чернового скандиевого концентрата (ЧСК). На второй стадии согласно разработанной схеме процесса ЧСК перерабатывается в оксид скандия высокой чистоты. Для получения 100 г Sc2O3 необходимо переработать 1000 кг хвостов и 2,5 кг ЧСК. Установлено, что при исходном содержании 60–100 г/т Sc2O3 и сквозном его извлечении в конечный продукт от 75 до 90% для получения 1 т Sc2O3, необходимо переработать 10 тыс. т отходов мокрой магнитной сепарации Качканарского ГОКа. Значительные объемы их переработки обусловливают накопление силикатно-гипсового остатка, который может быть использован для производства цемента и гипса. Тем самым может быть осуществлено внедрение на Качканарском ГОКе комплексной переработки обогатительных отходов с получением оксида скандия и двух высоколиквидных строительных материалов.
Целый ряд докладов был посвящен специфике сорбционных и ионообменных процессов селективного извлечения индивидуальных РЗМ — Ce, La, Er и скандия, включая использование в этих целях наноматериалов и нанотехнологий (РХТУ им. Д.И. Менделеева, ВНИИХТ, АО «ГИРЕДМЕТ», Уральский федеральный университет).
В специальном докладе всесторонне освещены перспективы рециклинга РЗМ в связи с увеличением мирового производства люминесцентных ламп, никель-металлогидридных батарей, каталитических нейтрализаторов и магнитов. В отработанных продуктах связано до 60–65% от извлеченного из сырья количества La, Ce, Pr, Nd, Sm, Eu, Gd, Tb, Dy и иттрия. Прогнозная оценка специалистов Березниковского филиала Пермского НИПИ и Госуниверситета управления свидетельствует о том, что к 2020 году выпуск РЗМ за счет переработки вторичного сырья может превысить 5 тыс. т. Ведущие автомобильные компании Японии, а также немецкая OSRAM и бразильская Resende and Morais реализуют проекты получения РЗМ, включая Nd, Dy, Eu Y, из различного вторсырья, содержащего редкие земли.
В настоящее время очевидно формирование и саморазвитие, помимо действующих производств РЗМ Ловозерским ГОКом и СМЗ, нескольких научно-производственных редкометально-редкоземельных центров в Европейской части России (Москва, Апатиты, Санкт-Петербург, Королев, Череповец) и в Сибири (Новосибирск, Красноярск и др.). Их инновационные разработки базируются на различных видах природного сырья и техногенных образований. Исключительно актуальной, но пока не решенной задачей является восстановление нарушенных межгосударственных связей в редкометально-редкоземельной отрасли России с Казахстаном (Прииртышье) и Кыргызстаном (Актюз) в целях реализации стратегических задач ЕвразЭС. Не менее актуальной представляется организация совместных геологоразведочных и эксплуатационных работ с зарубежными странами Юго-Восточной Азии, где обнаружены месторождения РЗМ, заслуживающие совместной оценки в качестве объектов промышленного освоения (Монголия, Северная Корея).
Литература:
Аржаткина О.А., Елагин В.Я., Федорова Т.В. Щелочно-сернокислотная технология переработки лопаритового концентрата. // Сборник докладов Международного симпозиума «Стратегия использования и развития минерально-сырьевой базы редких металлов России в XXI веке». М: ВИМС, 1998.
Гончаров В.В. Анализ цен редкоземельных металлов по разным источникам и прогнозам до 2018 г. // Сборник материалов Международной практической конф. «Актуальные вопросы получения и применения РЗМ — 2015», 25 июня 2015, Москва. М: ОАО «Институт «ГИНЦВЕТМЕТ», 2015, С. 16–19.
Литвинова Т.Е. Получение соединений циркония и редкоземельных металлов из эвдиалитового сырья. // Сборник материалов Международной практической конф. «Актуальные вопросы получения и применения РЗМ — 2015», 25 июня 2015, Москва. М: ОАО «Институт «ГИНЦВЕТМЕТ», 2015, С. 167–171.
Маслобоев В.А., Лебедев В.Н. Редкоземельное сырье Кольского полу-острова и проблемы его комплексной переработки. Апатиты: КНЦ РАН, 1991. — С. 152.
Мелентьев Г.Б. Перспективы использования нерудного и редкометалльного сырья Кольского региона в производстве керамических и новых неорганических материалов. // «Конструкции из композитных материалов», 2003, № 1, С. 11–32. Мелентьев Г.Б., Самонов А.Е., Толстов А.В. В ожидании промышленного освоения, или Почему Томтор открывает огромные выгоды инвесторам и государству? // «Химия и бизнес», 2013, № 5–6, С. 60–63.
Мелентьев Г.Б. Редкоземельные приоритеты России. // «Редкие земли», 2014, № 3, С. 18–32.
Чистов Л.Б., Охрименко В.Е., Юфряков В.А и др. Эвдиалитовые руды — новое промышленное сырье циркония и редкоземельных элементов. // Сб. докладов Международного симпозиума «Стратегия использования и развития минерально-сырьевой базы редких металлов России в XXI веке». М: ВИМС, 1998, С. 102–104.
ТЕКСТ: Г.Б. Мелентьев
- 23 апреля 2025 ОТ «ОБОРОНКИ» ДО СПОРТА: КАК СКАНДИЙ МОЖЕТ ПЕРЕВЕРНУТЬ РОССИЙСКУЮ ПРОМЫШЛЕННОСТЬ
- 18 апреля 2025 ОТ ХАЙПА К ДЕЛУ: КАК РАЗВИВАТЬ РЗМ-ИНДУСТРИЮ В РОССИИ
- 9 апреля 2025 ВЫИГРАТЬ ВСУХУЮ: О НОВЫХ ПОДХОДАХ И ТЕХНОЛОГИЯХ В ОБОГАЩЕНИИ ПОЛЕЗНЫХ ИСКОПАЕМЫХ В ЯКУТИИ
- 26 марта 2025 Арктическое пророчество
- 26 февраля 2025 ПОЯВЛЕНИЕ ЖУРНАЛА “РЕДКИЕ ЗЕМЛИ” ОПЕРЕДИЛО ВРЕМЯ НА 10 ЛЕТ - АКАДЕМИК РАН ВЛАДИСЛАВ ПАНЧЕНКО
- 14 февраля 2025 Редким землям России нужен ТРАМПлин
- 6 февраля 2025 РЕДКИЕ ЗЕМЛИ ЗА СТОЛОМ ПЕРЕГОВОРОВ
- 3 февраля 2025 РАЗДЕЛЯЙ И ЗАРЯЖАЙ
- 26 января 2025 ВЛАДИМИР ВЕРХОВЦЕВ ОТМЕЧАЕТ 70-ЛЕТИЕ
- 27 декабря 2024 МЕЖДУ МИРОМ И ВОЙНОЙ: ЯДЕРНОЕ ОРУЖИЕ ДЛЯ РАЗРУШЕНИЯ И СОЗИДАНИЯ
- 27 октября 2024 ДЛЯ ГЛАВНОЙ НАУКИ БУДУЩЕГО ЧЕЛОВЕЧЕСТВО ДАЖЕ НЕ ПРИДУМАЛО НАЗВАНИЕ
- 13 октября 2024 Форум «Микроэлектроника 2024» – без высокочистых редких металлов никуда
- 23 сентября 2024 ОТ ВОЗРОЖДЕНИЯ МАГНИТНОГО ПРОИЗВОДСТВА К СОЗДАНИЮ НОВОЙ ИНДУСТРИИ В РФ
- 14 сентября 2024 "Задачи будут решены" – О беспилотниках из первых рук
- 31 августа 2024 ВИКТОР САДОВНИЧИЙ: «ЕСЛИ БЫ НЕ МОСКОВСКИЙ УНИВЕРСИТЕТ, РОССИЯ БЫЛА БЫ ДРУГОЙ»