ТЕХНОЛОГИЧЕСКИЕ ПРОБЛЕМЫ ТОМТОРА И ИХ РЕШЕНИЕ

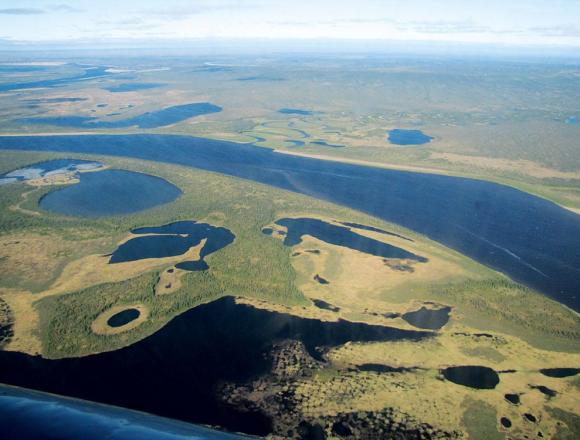
В РОССИИ на правительственном уровне санкционировано освоение мирового супергиганта — железорудно-алюмофосфатно-редкометалльного месторождения Томтор на северо-западе Республики Саха (Якутия). С 2009 года авторами в центральных научных изданиях и на конференциях продвигалась идея о необходимости создания на базе этого уникального месторождения нового заполярного горно-химико-металлургического кластера, подобного созданным в условиях «мобилизационной экономики» Кольскому и Норильскому ГПК. Высокие концентрации редких иттриево-земельных металлов в рудах Томтора и реальные возможности инфраструктурного обеспечения (ресурсные, энергетические, логистические), несмотря на локализацию в удаленном районе северо-запада Республики Саха (Якутия), позволяли рекомендовать его в качестве нового первоочередного сырьевого источника для производства РЗМ, феррониобия, иттрия, скандия, а также алюмофосфатов и другой высоколиквидной продукции. Комплексное освоение Томтора, превосходящего по ресурсам, качеству и разнообразию минерального сырья зарубежные аналоги (Араша в Бразилии и др.), может сыграть роль «спускового механизма» в создании на северо-западе Якутии нового заполярного горно-химико-металлургического комплекса, способного обеспечить необходимое импортозамещение потребностей России в важнейших видах стратегической металлопродукции.
История открытия (1959 г.), многолетних поисково-оценочных работ и предварительной разведки (1977–1997 гг.) месторождения Томтор на северо-западе Республики Саха (Якутия) с уникально богатыми содержаниями широкого комплекса редких и редкоземельных металлов (РЗМ), во многом напоминает ситуацию с Белозиминским месторождением, изложенную в предыдущем выпуске «РЗ». Действительно, прошло больше полувека с момента открытия Томтора, 20 лет геологоразведки и более 15 лет пребывания его в государственном резерве РФ, пока, наконец, в 2014–2015 годах было принято решение о необходимости его промышленного освоения. Усилиями геологов и ученых Российской академии наук обоснованы перспективы первоочередного освоения предварительно разведанного уч. Буранный как наиболее богатого в нашей стране сырьевого источника РЗМ, включая дефицитную группу иттриевых лантаноидов и такие редкие металлы, как ниобий и скандий. В настоящее время возобновлены геологоразведочные работы не только на уч. Буранный в целях его доизучения на стадии детальной разведки, но и на двух других, наименее изученных — Северном и Южном.
Одной из важнейших задач этих работ является разработка принципиально новых технологий глубокой и комплексной переработки сложных по составу охристых редкометалльно-редкоземельных руд, не поддающихся обогащению традиционными физико-механическими методами. Авторы настоящей публикации в рамках Программы НИР Президиума РАН, независимо от организации и финансирования ГРР, разрабатывают принципиально новую обогатительно-передельную технологию глубокой переработки томторского сырья с разделением в голове процесса ниобия и РЗМ, включающую методы пиро- и гидрометаллургического получения конечной высоколиквидной продукции.
СПЕЦИФИКА ХИМИЧЕСКОГО И МИНЕРАЛЬНОГО СОСТАВА РЕДКОМЕТАЛЛЬНО-РЕДКОЗЕМЕЛЬНЫХ РУД ТОМТОРА И РЕЗУЛЬТАТЫ ИЗУЧЕНИЯ ИХ ОБОГАТИМОСТИ
Редкометалльно-редкоземельные руды Томтора представляют собой переотложенные коры выветривания карбонатитов. Этим обусловлены их отличия от остаточных кор выветривания на карбонатитах: с одной стороны, высокая степень обогащенности редкими металлами как особо ценными полезными компонентами и, с другой стороны, тонкодисперсное строение, распределение редкометалльных компонентов между несколькими минеральными фазами, включая их сростки, глинистые фракции, пленки гидроксидов железа и другие шламообразователи. Указанная специфика состава и строения разведанного на уч. Буранном томторского сырья позволяет считать его с известной степенью допущения смесью природного редкометалльно-редкоземельного минерального концентрата со шламовой составляющей руд, которая также является продуктивной.
В то же время следует иметь в виду, что под «плащом» редкометалльно-редкоземельных руд средней мощностью порядка 10 м (до 20–40 м) залегают ниобиево-фосфатно-железистые (гетитовые, лимонитовые и сидеритовые) руды остаточной коры выветривания мощностью до 300–400 м при устойчивом содержании Nb2O5 ≥ 1%. Эти руды должны рассматриваться и оцениваться в качестве источника фосфатных (франколитовых) концентратов и, главное, как сырье для возможного производства феррониобия.
Минеральный состав руд уч. Буранный и распределение в них основных химических компонентов между минералами представлены на схеме рис. 1. Размеры минералов в рудах чрезвычайно малы, 75–80% из них составляют частицы размером меньше 20 мкм. Минералы в рудах находятся в тонком взаимном прорастании с большим количеством шламов. Указанные свойства руд не позволили создать на стадии разведки технологию комплексной переработки руд Томторского месторождения методами физического обогащения.
Химический состав руд уч. Буранный месторождения Томтор представлен в таблице 1. В колонке 2 приведено среднее арифметическое содержание компонентов (Х %, масс.) рудного пласта, в колонке 3 — среднее квадратичное отклонение (S, масс. %), в колонке 4 — коэффициент вариаций содержания компонентов (V, отн. %). В колонках 5 и 6 приведены химические составы двух различных по содержанию Р2О5, SiO2, TiO2, Al2O3, Fe2O3, CaO, Nb2O5, TR2O3 проб руды, которые использовались при изучении ликвации расплавов: богатая пирохлор-монацит-крандаллитовая руда, характеризующаяся очень высоким содержанием редких земель и ниобия и низким содержанием SiO2; рядовая пирохлор-монацит-каолинит-крандаллитовая руда с небольшим содержанием ниобия, средним содержанием редких земель и довольно высоким содержанием Al2O3 и SiO2. Изученные руды Томтора характеризуются крайне незначительным содержанием щелочей, относительно небольшим содержанием железа, титана, оксидов кальция, стронция и бария. Причем железо находится как в двух-, так и в трехвалентной форме. Для всех компонентов показательным является высокое значение коэффициента вариации их содержаний, составляющее около 50%. Меньше всего подвержены колебаниям содержания Р2О5, коэффициент вариаций которого составил 24,1%. Высокое значение коэффициента вариации компонентов ставит прямую задачу усреднения состава руд прежде чем они поступят на предприятие по их переработке.
Изученные руды значительно отличаются по минеральному составу на разных участках рудного поля (таблица 2). В количественном отношении главную роль играют три минерала: монацит, пирохлор и крандаллит, все остальные минералы находятся в подчиненном количестве. Фосфор на 90% находится в составе монацита и крандаллита и только небольшая его доля (2–5%) — в составе апатита. Отметим, что минералы группы крандаллита (алюмофосфаты Ca, Sr, Ba и TR) недостаточно изучены с технологических позиций. Основная часть ниобия содержится в пирохлоре — одном из главных рудообразующих минералов. Главным носителем редких земель, иттрия и скандия является монацит. Среди минералов железа широко представлен сидерит, в то время как содержания магнетита невелики. Содержание силикатных минералов весьма изменчиво: в богатых рудах их очень мало, в то же время в каолинит-крандаллитовых рудах содержится большое количество кремнезема.
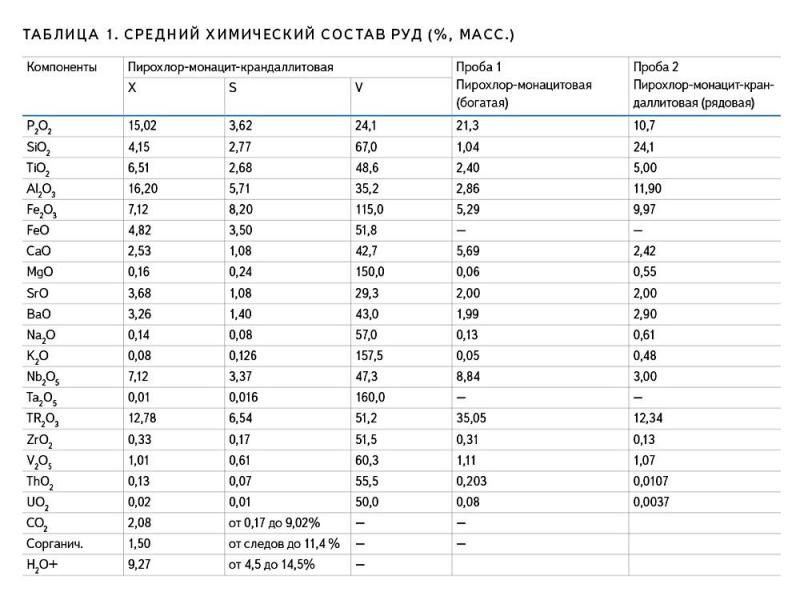
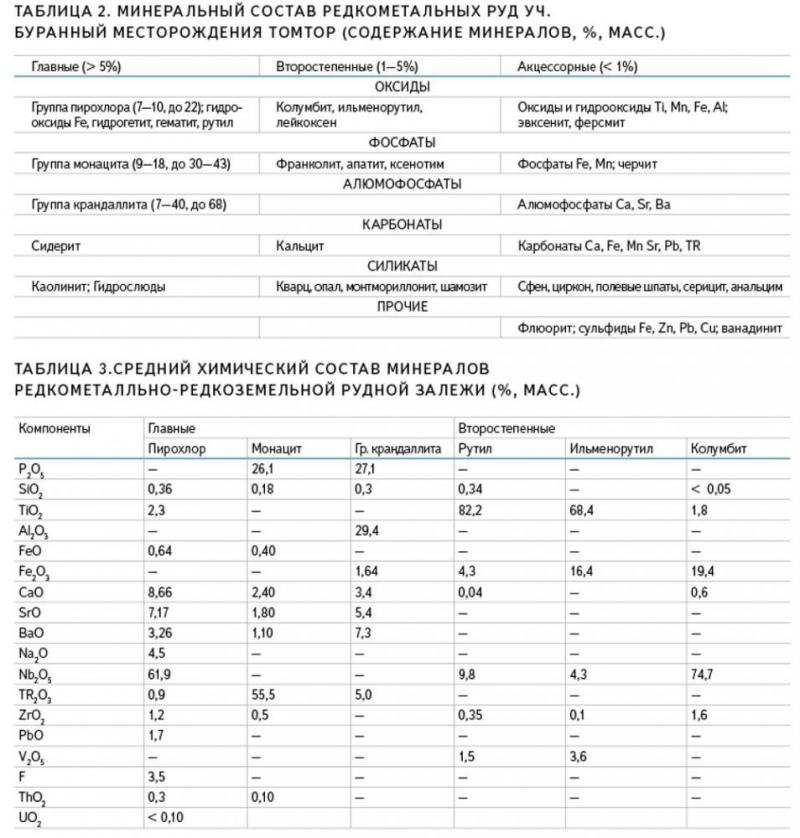
Средний химический состав главных рудо-образующих минералов редкометалльно-редкоземельной залежи по данным анализа на микрозонде приведен в таблице 3. По существу, главные минералы представляют собой соли соответствующих кислот: пирохлор — основная соль ниобиевой кислоты, монацит — редкоземельная соль ортофосфорной кислоты, крандаллит — основная соль алюмофосфорной кислоты. Рутил, ильменорутил и колумбит представляют собой сложные окислы. Одни и те же химические компоненты в том или ином количестве входят в состав всех рудных минералов: TR2O3 распределяются между монацитом, пирохлором и крандаллитом, Nb2О5 содержится в пирохлоре, рутиле и колумбите, Al2O3 — в крандаллите и каолините, Fe — в сидерите, крандаллите, колумбите и т.д.
Химические составы рудных минералов уч. Буранный Томторского месторождения в двух пробах руды, использованных для авторских технологических исследований, приведены в таблицах 4 и 5: в таблице 4 — фосфатных минералов, в таблице 5 — оксидных минералов.
Приведенные данные свидетельствуют о том, что одни и те же компоненты входят в состав различных минералов (рис. 1), что не позволяет получать мономинеральные концентраты, пригодные для производства соединений редких земель и ниобия.
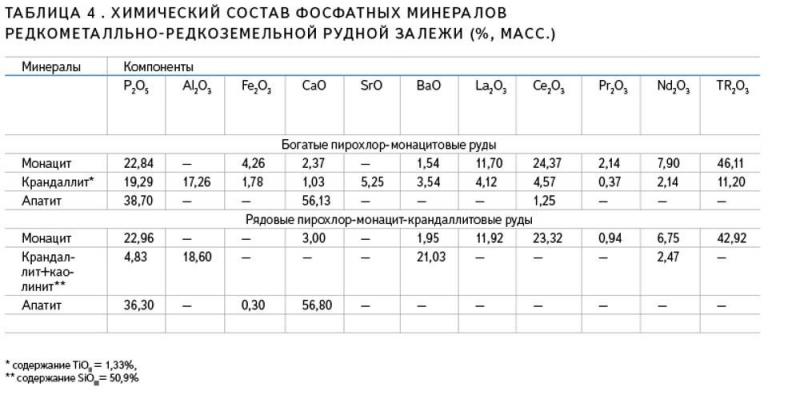
Карботермическим способом, относящимся к физико-химическим способам обогощения, возможно получение феррофосфора, содержащего ниобий, и шлака, содержащего редкие земли. Однако в процессе высокотемпературной плавки происходит восстановление в газовую фазу фосфора, потери которого составляют почти 20%. Двухстадийным гидрохимическим методом возможно получение редкоземельных и ниобиевых полупродуктов. При этом потери ценных компонентов с отвальными шламами составляют не менее 50%.
Несмотря на усилия обогатителей в процессе разведки уч. Буранный, где сосредоточено ~ 8% запасов и ресурсов Томторского месторождения, получение кондиционных пирохлорового и монацитового концентратов оказалось невозможным. Методы физического обогащения руд (флотация, магнитная сепарация, гравитационное обогащение) оказались не эффективными, а получаемые концентраты — непригодными для выпуска конечной редкометалльной продукции. В настоящее время за базовую схему принята предложенная ИХХТ СО РАН гидрометаллургическая — автоклавная щелочная технология переработки руды, которая пригодна не для всех промышленных типов руд и имеет значительные ограничения по содержаниям SiO2, Fe2O3, CaO и TiO2 (таблица 6).
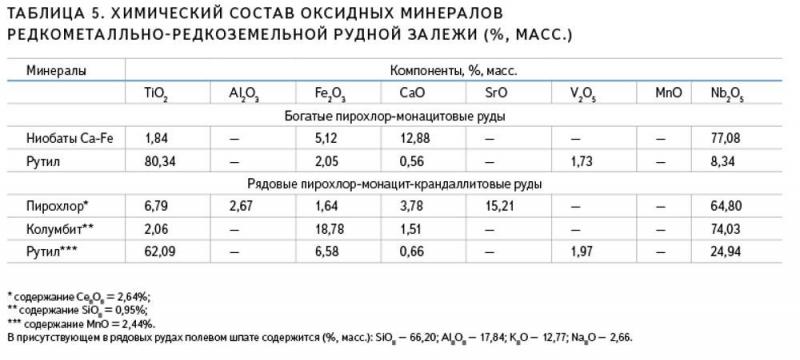
Приведенные в таблице 6 технологические способы обладают как положительными, так и отрицательными решениями, причем все они оказались в большой зависимости от состава и свойств тех проб руды, которые поступали в соответствующие организации. Однако накопленный опыт в данной области является той базой, которая использована для разработки принципиально новой пирохимической технологии — метода прямой ликвационной плавки.
НОВОЕ НАПРАВЛЕНИЕ ПЕРЕРАБОТКИ РУД ТОМТОРСКОГО МЕСТОРОЖДЕНИЯ — МЕТОД ЛИКВАЦИОННОЙ ПЛАВКИ
Процесс ликвационной плавки в присутствии солевых добавок-флюсов и агентов ликвации (фтор — соли — оксиды) с получением несмешивающихся расплавов, контрастных по составу и свойствам, применительно к рудам Томтора ранее не изучался и не применялся. Для рудных систем, содержащих фосфаты редких земель и алюмофосфаты щелочноземельных металлов, оксиды ниобия, титана, силикаты, сведения об образовании несмешивающихся расплавов в научно-технической литературе отсутствуют. Нет также данных даже о температуре плавления ортофосфатов редких земель (LaPO4, CePO4, монацита). В связи с этим выполнены экспериментально-технологические исследования ликвации расплавов для двух типов руд Томтора: богатой пирохлор-монацитовой (ПМР) и рядовой пирохлор-монацит-крандаллитовой (ПМКР). Кроме того, проведено изучение системы LaPO4-NaF с целью определения растворимости данных компонентов в области расплавленного состояния.
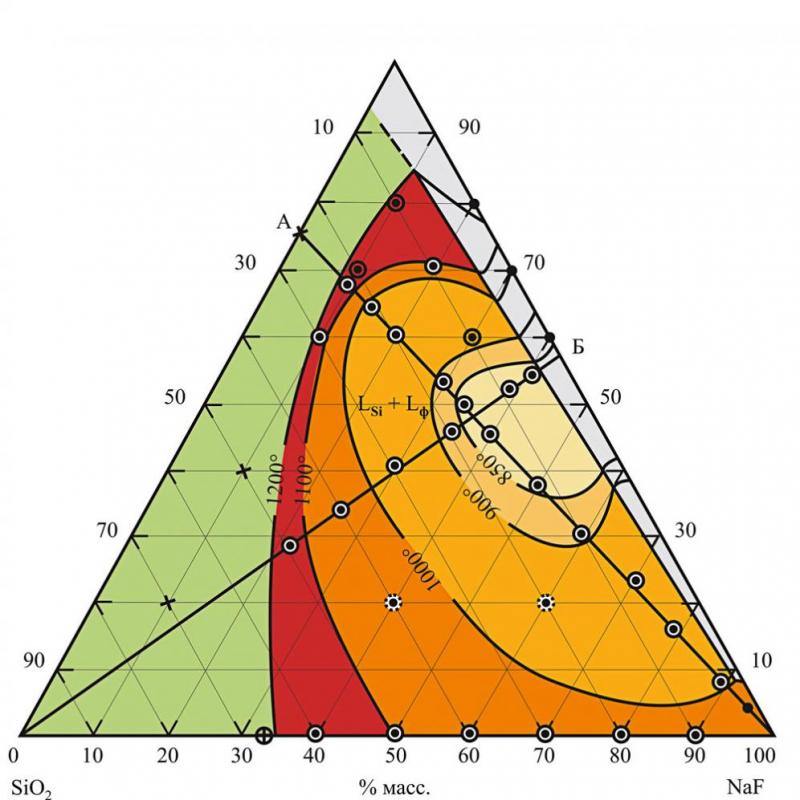
Система ПМР-SiO2-NaF. Результаты экспериментальных исследований полей ликвации расплавов в системе ПМР-SiO2-NaF представлены на рис. 2. На эмпирической диаграмме состояния этой системы (рис. 2) приведены пять изотермических сечений (850, 900, 1000, 1100 и 1200 0С), внутри которых оконтурены области ликвации расплавов; слева от изотермических линий находятся области неполного плавления, где в равновесии с несмешивающимися расплавами присутствуют кристаллические фазы. Площадь поля ликвации расплавов с увеличением температуры значительно расширяется: при температуре 850 0С она составляет 8% от площади диаграммы, при 900 0С — 14%, при 1000 0С — 38%, при 1100 0С — 53%, при 1200 0С — 62%. В экспериментальных точках, указанных на диаграмме, расплавы разделяются на два слоя: силикатный и фосфатно-солевой, и только там, где содержание ПМР составило 20% и меньше, образуются расплавы эмульсионного строения. Узкое поле однофазного состояния расплава (1L), где компоненты полностью растворяются друг в друге, находится в правой части диаграммы и занимает всего 5% площади диаграммы, что свидетельствует о небольшой растворимости силикатного расплава в фосфатно-солевом, не превышающей 5–7%.

Для выяснения влияния температуры и содержания в шихте фторида натрия на образование несмешивающихся расплавов в системе ПМР-SiO2-NaF исследован политермический разрез А-NaF, проведенный через точку А в угол NaF (рис. 3). Во всех точках разреза сохраняется постоянное отношение между содержанием руды ПМР и SiO2 = 3:1 при различном содержании в шихте фторида натрия. Данный разрез представляет собой частное сечение сложной многокомпонентной силикатно-солевой системы и характеризуется следующими особенностями. При 1100 и 1200 0С в отсутствие NaF происходит только частичное плавление шихты с образованием крепких спёков красного цвета. Никаких признаков образования несмешивающихся расплавов при этом не установлено. С увеличением температуры до 1400 0С количество жидкой фазы в спёкшемся материале увеличивается, однако полного плавления шихты при этом не происходит. Очевидно, что требуется более высокая температура для полного плавления томторской руды. В то же время при введении в систему фторида натрия шихта плавится с образованием двух несмешивающихся расплавов: силикатного и фосфатно-солевого.
Политермический разрез А-NaF в системе ПМР-SiO2-NaF. На рис. 3 хорошо видно, что система выше линии ликвидуса разделяется на два поля: левое — со стороны ПМР и правое — со стороны NaF.
Левая часть ликвидуса представляет собой кривую плавления руды с образованием двух несмешивающихся расплавов в зависимости от температуры и содержания NaF. При 1150 и 1200 0С и содержании в шихте 10% NaF образуются два слоя несмешивающихся расплавов: силикатный и фосфатно-солевой, при 1100 0С количество фторида натрия составляет 11–12%. При 1000 0С ликвация расплавов происходит при 15–16% NaF в шихте, при 900 0С необходимо добавить в шихту уже 31–32% NaF. Образование двух несмешивающихся расплавов происходит и при 850 0С, однако содержание NaF в шихте составляет 35%. Расплавы четко разделяются по границе фазового раздела. Левая ветвь линии ликвидуса имеет S-образное строение, что указывает на протекание в системе химических реакций между компонентами. На правой ветви линии ликвидуса данного разреза образование двух несмешивающихся расплавов происходит при 850 0С и содержании NaF 50%, при 900 0С содержание NaF 60%. При 800 0С два несмешивающихся расплава находятся в равновесии с кристаллическими фазами, при этом фосфатно-солевой расплав отделяется в виде хорошо сформировавшегося слоя. Начало плавления в данном разрезе определено при 770 0С и содержаниях ПМР 63% и NaF 37%. В правой части диаграммы видно, что при содержании NaF 90% расплавы являются двухфазными, то есть растворимость силикатного расплава в солевом составляет < 5%.
Образцы ликвации расплавов, полученные при плавке ПМР с содержанием в шихте 18% NaF при 1200, 1100 и 1000 0С в течение 1 часа, показаны на рис. 4. Во всех образцах фосфатно-солевые расплавы находятся на дне тиглей, силикатные расплавы располагаются над фосфатными расплавами и их перекрывают.
Химический состав сосуществующих расплавов определен на микрозонде, масс-спектрометрическим, атомно-эмиссионным и рентгеноспектральным методами и приведен в таблице 7. Эти данные свидетельствуют, что главными компонентами силикатных расплавов являются SiO2, Fe2O3, Na2O и Nb2O5, тогда как главными компонентами солевых расплавов являются P2O5, CaO, SrO, BaO, Na2O, F и лантаноиды: La2O3, Ce2O3, Pr2O3, Nd2O3 и др. Присутствие P2O5 в силикатном расплаве обусловлено наличием обособлений мелких фосфатно-солевых микросфероидов (рис. 5). Их химический состав идентичен составу фосфатно-солевого расплава, сформировавшегося в виде макрослоя (см. таблицу 7, 8 и рис. 4–7).
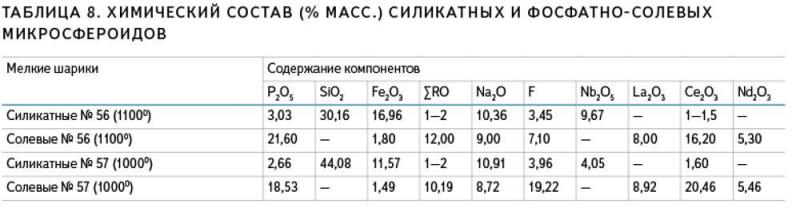
В фосфатно-солевом расплаве (аналогично силикатному расплаву) присутствуют мелкие обособления силикатного расплава (рис. 6). Их химический состав идентичен составу силикатного расплава, сформировавшегося в виде макрослоя (см. таблицу 7 и 8 и рис. 4–7). Высокая кристаллизационная способность фторидно-фосфатно-солевого расплава обусловливает его кристаллизацию, включая микрофазы редкоземельных новообразований (рис. 7).
Система ПМКР-SiO2-NaF. Для системы ПМКР-SiO2-NaF, так же как и для системы ПМР-SiO2-NaF, построен политермический разрез при равном отношении в шихте ПМКР к SiO2 = 3:1 и различном содержании фторида натрия. Результаты исследований представлены на рис. 9. На диаграмме состояния системы выделены два поля: левое, с образованием двух несмешивающихся расплавов в зависимости от температуры и содержания NaF, и правое, характеризующее растворимость руды в расплаве фторида натрия. Строение политермического разреза в системе ПМКР-SiO2-NaF практически мало отличается от разреза в системе ПМР-SiO2-NaF.
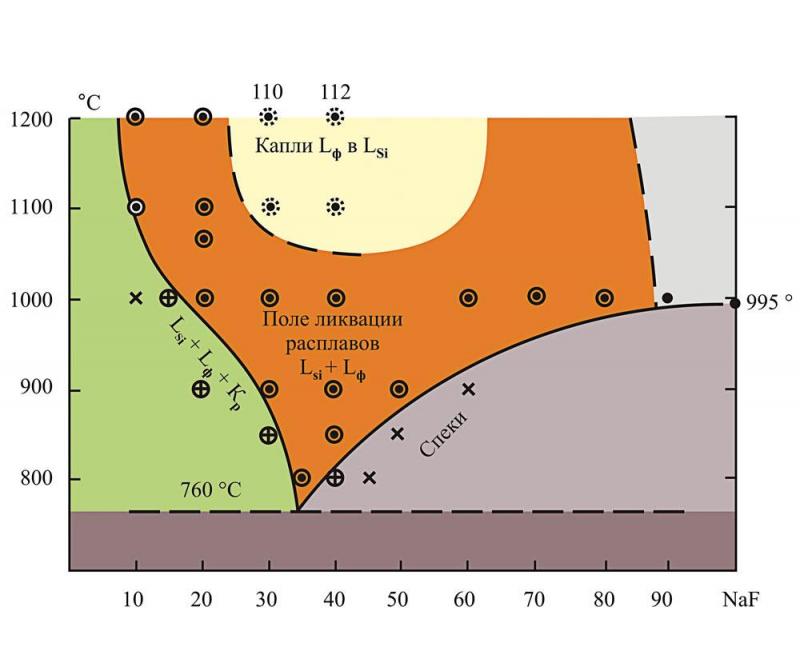
Во всех случаях при содержании в шихте до 30% NaF и температуре 1000–1200 0С происходит разделение силикатных и фосфатно-солевых расплавов на два слоя: верхний — силикатный расплав, нижний — фосфатно-солевой. Морфологически продукты ликвации такие же, как и для пирохлор-монацитовой руды. В правой части диаграммы видно, что при содержании NaF 90% расплавы остаются двухфазными, то есть растворимость силикатного расплава в солевом меньше 10%. Отметим, что рядовая пирохлор-монацит-крандаллитовая руда является более легкоплавкой по сравнению с пирохлор-монацитовой.
В то же время при содержании в шихте 30–40% NaF и температуре 1100–1200 0С расплавы приобретают эмульсионное строение. При температуре ниже 1100 0С при тех же составах рудная шихта плавится с образованием двух обособленных слоев.
Проведенное исследование системы LaPO4-NaF обусловлено необходимостью выяснения начальной температуры плавления солевых компонентов, а также их растворимости в расплавленном состоянии. Как следует из данных по минеральному составу томторских руд, главным носителем редких земель является монацит, в составе которого находятся лантан, церий, неодим, празеодим и др. лантаноиды. Поэтому на данной стадии исследований было принято использовать в качестве компонента ортофосфат лантана, ближе всего соответствующего монациту. Тем более что лантан всегда сохраняет валентность 3+, в отличие от церия и др. лантаноидов. Для изучения системы LaPO4-NaF в качестве компонентов использованы синтетический ортофосфат лантана и фторид натрия (ч.д.а.). Основной метод исследования — дифференциальный термический анализ. Установлено, что система LaPO4-NaF является системой c полной взаимной растворимостью компонентов в расплаве (рис. 9).
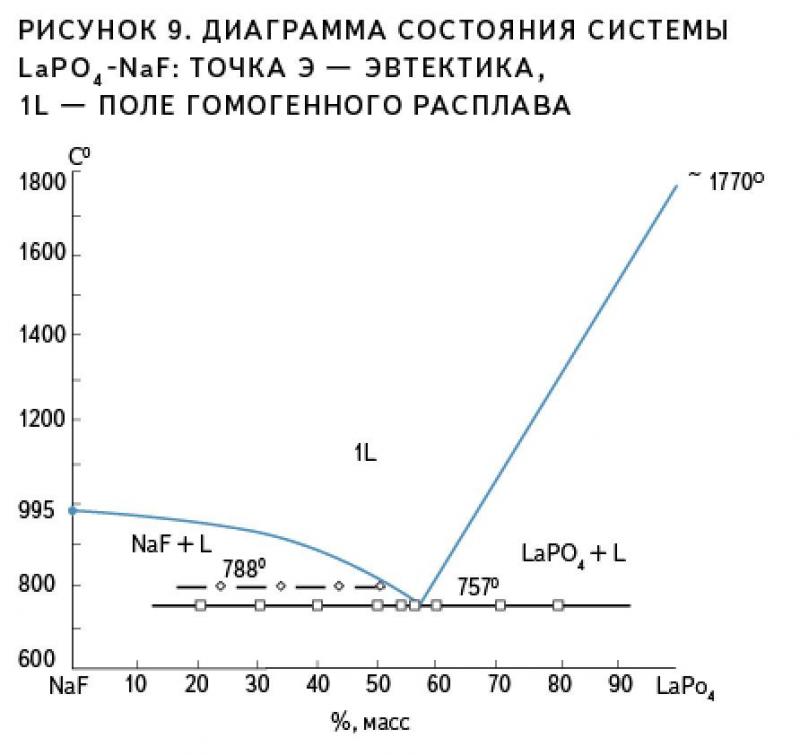
На диаграмме LaPO4-NaF выделены ветвь кристаллизации ортофосфата лантана и ветвь кристаллизации фторида натрия. Эвтектика в системе определена при температуре 757 0С и содержании LaPO4 57% + NaF 43%. Таким образом, LaPO4 и NaF полностью взаиморастворимы в расплавленном состоянии и никаких проявлений несмесимости не установлено. Вполне очевидно, что NaF является растворителем фосфатов редких земель и соответственно экстрагирует их в процессе ликвации в солевой расплав. Поскольку в рудах максимальное содержание монацита может составить 40–43%, то согласно диаграмме LaPO4–NaF при введении в шихту 20% NaF при температуре 1000оС все редкоземельные фосфаты будут растворены в солевом расплаве. Также установлено, что в системе LaPO4-NaF протекает обменная химическая реакция с образованием двойного фосфата Na3La[PO4]2.
Образование двойных фосфатов установлено также при проведении ликвационной плавки томторской руды с NaF. При этом в раскристаллизованных фосфатно-солевых расплавах присутствует несколько групп лантаноидов, одна из которых ближе всего соответствует монациту, а вторая представлена двойными фосфатами лантаноидов и оксида натрия. На рис. 7 приведена кристаллическая структура фосфатно-солевого расплава, где лантаноиды со структурой монацита образуют агрегаты белых кристаллов (1), а двойные фосфаты образуют длиннопризматические кристаллы серого цвета (2); темные непросвечивающие овальные микросфероиды (3) представляют собой капли силикатного стекла.
В отличие от монацита, для вскрытия которого, как известно, необходимо применение концентрированных растворов щелочей или серной кислоты и высокие температуры, двойной Ln-Na-фосфат разлагается слабыми растворами азотной кислоты при температурах 20–40 0С. Приведенные факты позволяют решать задачу переработки фосфатно-солевых расплавов иным способом, чем это принято в практике переработки монацитовых руд.
Инновационная технологическая схема переработки руд томторских редкометалльно-редкоземельных руд с применением ликвационной плавки как полезная модель. При проведении опытов ликвации расплавов с богатой пирохлор монацитовой и с рядовой пирохлор-монацит-крандаллитовой рудой в одинаковых условиях (температура 1070–1100 0С, продолжительность 1 час, вес шихты 100 г) установлено, что различие между ними заключается в объемах сосуществующих расплавов. Если при плавке богатой руды выход солевого расплава составил 70%, а силикатного 30% (см. рис. 4), то при плавке рядовой руды выход солевого расплава составил 30%, а силикатного 70% (рис. 10). Таким образом, ликвационная плавка богатой руды обеспечивает получение продукта, обедненного ниобием, и обогащенного редкими землями, в то время как плавка рядовой рудной шихты, наоборот, позволяет получать преимущественно ниобиевый и в меньшей степени редкоземельный продукты.
Следовательно, перед проведением ликвационной плавки руды разного состава необходимо смешивать в заданных пропорциях, то есть усреднять шихту до такого состава, чтобы выходы силикатного и солевого расплавов составляли примерно по 50%. При этом будут получены расплавы заданного состава, что должно положительно сказаться на последующей технологии их переработки в соответствующую продукцию.
Рудоподготовка богатой и бедной руды включает классификацию на грохоте с получением двух фракций: 0–2 мм и крупнее 2 мм. Фракцию крупнее 2 мм подвергают дроблению до классов меньше 2 мм и объединяют с фракцией 0–2 мм. Богатые и бедные руды объединяют в один поток и усредняют так, чтобы содержание в SiO2 cocтавило от 8 до 30%, P2O5 — от 5 до 15%, Fe2O3 — от 1 до 40%. Усредненную руду подают в шнековый смеситель, куда через дозатор вводят солевую добавку (6–20% масс.), и далее гранулируют на тарельчатом грануляторе. В качестве связующего для гранулирования используют бедную крандаллитовую руду, в которой содержится глинистый минерал — каолинит. Гранулированную шихту с влажностью 10–12% подают во вращающуюся печь, в которой обжигают при температуре 800–900 0С. Обожженные гранулы в горячем виде через питатель-дозатор бункерного типа подают в плавильный аппарат. Засыпка гранул происходит вдоль стенки плавильного аппарата так, чтобы они сформировали откосы, на которых при температуре 1100–1200 0С осуществляют процесс плавления с образованием двух несмешивающихся расплавов: фосфатно-солевого и железисто-алюмосиликатного. Гетерогенный (двухфазный) расплав по поду печи перетекает через бортик в обогреваемый до 1150–1250 0С копильник, в котором происходит его отстаивание и полное разделение несмешивающихся расплавов на два жидких слоя и усреднение их состава. Разделение расплавов происходит в соответствии с их плотностью: нижний более тяжелый расплав — фосфатно-солевой, верхний менее тяжелый — железо-алюмосиликатный. Небольшое (около 4–5%) количество «капель» фосфатно-солевого расплава остается в виде «запутавшихся корольков» в железисто-алюмосиликатном расплаве, а 4–5% «капель» железо-алюмосиликатного расплава остается в составе фосфатно-солевого расплава.
Таким образом, рекомендуемый технологический процесс осуществляется в две стадии (дуплекс-процесс): спекание шихты при температуре 800–900 0С и ликвационная плавка при 1100–1200 0С. На первой стадии происходит сушка шихты, ее обезвоживание, разложение карбонатных и глинистых минералов, удаление органики. В этом же интервале температур происходит выплавление легкоплавких фосфатно-солевых и силикатно-солевых эвтектик, которые образуются за счет реакций взаимодействия между фосфатными, силикатными и солевыми компонентами, входящими в состав шихты. Образующиеся эвтектические расплавы цементируют твердые фазы с образованием гранулированного материала. Нагретый до температуры 800–900 0С спек поступает в газовую печь. На второй стадии осуществляется ликвационная плавка с образованием двух несмешивающихся жидких фаз (расплавов). Печь по данному процессу используется только как плавильный аппарат. Процесс плавления ведут в воздушной атмосфере.
Выпуск расплавов из копильника осуществляют последовательно через две лётки, расположенные на разных уровнях. Вначале выпускают верхний железисто-алюмосиликатный расплав, затем — нижний фосфатно-солевой. Часть расплава оставляют в копильнике, на поверхность которого из плавильного аппарата перетекает новая порция гетерогенного расплава.
Железисто-алюмосиликатный расплав гранулируют на выпускном желобе струей воды, обезвоживают и дробят до фракции 0–1 мм. Раздробленный шлак методами гравитационного обогащения разделяется на две фракции: одну, содержащую включения фосфатно-солевого расплава, и вторую, очищенную от включений фосфатно-солевого расплава. Фракцию, содержащую включения фосфатно-солевого расплава, направляют в питатель-дозатор бункерного типа для плавки вместе с гранулированной шихтой. Вода отстаивается и возвращается на гранулирование шлака. Шламы направляют в шнековый смеситель для приготовления шихты. Фракцию, очищенную от включений фосфатно-солевого расплава, перерабатывают известными методами на феррониобий и другие ниобийсодержащие продукты.
Фосфатно-солевой расплав гранулируют на выпускном желобе струей воды. Гранулированный продукт обезвоживают и перерабатывают известными сернокислотным или азотно-кислотным методами с получением удобрительных фосфатов и концентрата редких земель. Образующиеся после разложения фосфатно-солевого продукта шламы и «капли» железисто-алюмосиликатного шлака сгущают и направляют в питатель-дозатор бункерного типа для плавки вместе с гранулированной шихтой. Вода отстаивается и возвращается на гранулирование шлака. Шламы направляют в шнековый смеситель для приготовления шихты.
В то же время необходимо учитывать крайне неравномерное распределение наиболее ценных индивидуальных РЗМ в пределах рудной залежи уч. Буранный. Анализ результатов, полученных в последние годы, показывает, что в пределах месторождения могут быть выделены целые блоки объемом в сотни тысяч тонн руды, которые аномально обогащены Y, Sc и тяжелыми лантаноидами по сравнению со средними параметрами по месторождению. Содержания Y2O3 в этих пересечениях повышаются до 1,5–2,0% и более при средних концентрациях по месторождению 0,5%, а отношения Ln2O3/Y2O3 снижаются до 4,8–8,0 по сравнению со средними значениями для томторских руд на уровне 20–30. При этом отношения Ce/Y понижаются до минимальных значений 2,0–6,0, что означает выравнивание относительной доли легких и тяжелых лантаноидов. Такие участки целесообразно оконтурить методами малообъемного минералого-геохимического картирования с последующим технологическим доизучением, включая применимость сочетания пирохимических и гидрохимических способов извлечения индивидуальных иттриевоземельных лантаноидов, иттрия, скандия, возможно циркония и гафния. Не менее важным представляется также доизучение закономерностей распределения и минеральных форм концентрации тория и урана. Как следствие — не исключается целесообразность селективной отработки участков локализации таких богатых или, наоборот, экологически опасных радиоактивных руд.
Дальнейшая разработка и совершенствование новой технологической схемы переработки томторских руд включает решение следующих основных задач: 1) изыскания технологических возможностей извлечения из томторского редкометалльного сырья индивидуальных РЗМ и их наиболее ценных групп; 2) то же — применительно к получению товарной алюмо-фосфатной продукции, редкометалльных лигатур и сплавов (Al-Sc, Fe-Ti и др.); 3) разработки технологии получения феррониобия и фосфатных продуктов из различного фосфатно-ниобиево-железорудного сырья остаточных кор выветривания карбонатитов.
В целях объединения усилий специалистов ОИВТ (Москва) и ИХХТ РАН (Красноярск) между двумя организациями подписан договор о творческом сотрудничестве в разработках пирохимических и гидрохимических методов переработки томторских руд с получением технологически возможного и экономически целесо- образного ассортимента конечной высоколиквидной товарной продукции.
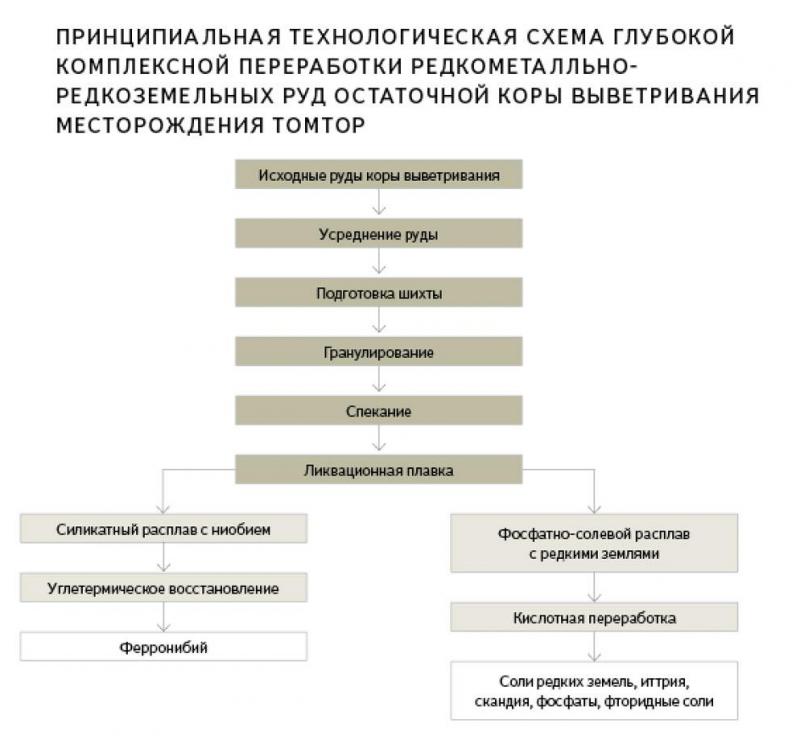
ТОМТОРСКИЙ МЕГАПРОЕКТ: РЕСУРСНО- ТЕХНОЛОГИЧЕСКИЙ «ПРОРЫВ» РОССИИ В XXI ВЕК?
В настоящее время крупным и единственным в нашей стране промышленным источником РЗМ в комплексе с Ta, Nb, Ti является Ловозерское месторождение лопаритовых руд. Томторское месторождение сравнительно с Ловозерским месторождением обладает целым рядом преимуществ, которые необходимо учитывать на инновационном этапе освоения северных территорий и тем более объектов стратегического значения: 1) возможностями открытой добычи сырья вместо подземной; 2) его дезинтегрированным состоянием и обогащенностью высоколиквидными полезными компонентами (руды как природные концентраты); 3) возможностями прямых переделов на месте с применением ликвационной плавки и получением сплава FeNb, фосфатного продукта, выделения иттриевых лантаноидов, иттрия, скандия; 4) более низкими содержаниями в сырье лимитируемых с технологических и экологических позиций компонентов — естественных радионуклидов, фтора и других.
Мировым эталоном уникальности среди крупных и богатых ниобием эксплуатируемых месторождений пирохлоровых руд является Араша в Бразилии, представленное корами выветривания карбонатитов со средними содержаниями 2,5% и запасами 11,5 млн т N2O5 при средних содержаниях сопутствующих РЗМ 13,5% и фосфора — 15% Р2О5. За счет прямых инвестиций США в освоение Араша через 7 лет после его открытия был организован выпуск пирохлоровых концентратов, а затем и их комплексная переработка на месте с получением в качестве ведущего продукта феррониобия. Впервые в мире здесь было осуществлено интегрирование добычи, обогащение и химико-металлургических переделов исходного сырья в единое производство.
В настоящее время Бразилия и компания СВММ являются монополистами на рынке феррониобия и ниобия, экспортируя их в возрастающих объемах более чем в 30 стран, включая Россию.
Наиболее совершенной и эффективной технологической схемой получения феррониобия из пирохлоровых концентратов является разработанная в 80-х годах и усовершенствованная в 2002 году применительно к рудам Араша комбинированная обогатительно-передельная технология компании СВММ. Она включает: 1) добычу дезинтегрированной коровой руды открытым способом с доставкой ее ленточным конвейером на обогатительную фабрику (3,2 км); 2) доизмельчение руды, получение фракций пирохлора ≤ 0,1 мм и флотацию с получением концентрата с примесями лимитируемых P2O5, S и Pb; 3) освобождение концентрата от лимитируемых компонентов прокаливанием при T = 800–900 0С с 25% хлоридом кальция и 5% извести (удаление свинца) и последующим выщелачиванием 5%-ной HCl (удаление фосфора и серы); при этом в фильтрате с растворимым фосфором в виде хлорида удаляется барий, содержания которого в пирохлоре Араша составляют 15–18% (пандаит); 4) пирометаллургический передел рафинированных пирохлоровых концентратов (59–65% Nb2O5) на феррониобий в восстановительной среде алюмотермическим способом с добавками в шихту шлакообразующих флюсов — флюорита, извести и гематитового концентрата; электроплавка проводится в печи при T ≥ 2000 0С с извлечением ниобия в конечный продукт до 96–97% и удалением природных радионуклидов в шлак.
Примеры Бразилии и Китая, которые в течение нескольких лет сумели монополизировать производства и мировой рынок, соответственно феррониобия и редких земель, свидетельствуют о необходимости ускоренного возрождения и развития таких производств в нашей стране, обладающей собственными крупными и суперкрупными запасами этих металлов, но утратившей по совокупности причин с распадом СССР производственные мощности.
С этих позиций обосновывается необходимость и перспективность первоочередного промышленного освоения Томторского месторождения богатых железисто-алюмофосфатно-редкометалльных руд как супергиганта, не имеющего аналогов в России и за рубежом. Уникальность Томтора и его инфраструктурное обеспечение, которому была посвящена специальная статья, ориентируют на создание нового химико-металлургического кластера в прибрежной зоне российской Арктики, подобного Кольскому и Норильскому ГПК, созданным в условиях мобилизационной экономики и обеспечившим возможности ускоренной индустриализации страны. Перспективность рекомендуемого поэтапного освоения Томтора обеспечивается не только уникальностью его сырья, но и возможностями использования этого месторождения в качестве эпицентра нового горно-химико-металлургического кластера в Заполярье, подобного Кольскому и Норильскому. Эти возможности обосновываются авторами с инновационных ресурсно-технологических, энергетических и логистических позиций, включающих социально-эколого-экономический фактор и общегосударственную целесообразность. Его создание, в отличие от Кольского и Норильского ГПК, должно соответствовать инновационному этапу развития российской экономики.
Инновационный потенциал территории Анабара — Уджи — Оленека преимущественно обусловлен уникальностью высококомплексного сырья Томтора, освоение которого предполагает использование нетрадиционных методов его поэтапного освоения — от организации первоначальной сезонной отработки, применения нетрадиционных технологий прямой переработки природных минеральных концентратов и до создания механизма эффективного взаимодействия соинвесторов и, соответственно, партнерства между государством и частным бизнесом на стадиях эксплуатации месторождения и создания необходимой инфраструктуры.
По мнению авторов, территория Анабара —Уджи — Оленека заслуживает включения в перечень центров экономического развития (ЦЭР), выделяемых МПР и экологии РФ, как одна из наиболее перспективных для создания здесь промышленного редкоземельно-редкометалльного кластера и развития с его использованием сопутствующих и побочных горно-химико-металлургических производств.
Таким образом, будущий горнопромышленный кластер можно рассматривать и как центр «берегового базирования» в восточной части Севморпути и российской Арктики. Если на юге от Томтора расположены сложившиеся центры алмазодобычи, то к северо-западу от него расположена Попигайская кольцевая структура, которая в перспективе представляется новым крупным центром добычи технических алмазов. Следовательно, вывоз продукции Томторского кластера может обеспечиваться в двух направлениях: северном и западном морском — до Мурманска и далее на юг по железной дороге и южном — до перерабатывающих предприятий «Росатома» в Красноярском крае.
В заключение необходимо заметить, что кластерная форма организации производств, согласно Майклу Портеру, приводит к созданию особой формы инноваций — «совокупного инновационного продукта». Как правило, наиболее эффективные кластеры формируются там, где ожидается или осуществляется «прорыв» в области техники и технологии с выходом на новые рыночные ниши. С этих позиций рекомендуемое создание нового горнопромышленного кластера с использованием уникального Томторского месторождения представляется безальтернативным вариантом ускоренного возрождения редкометалльных производств в России. При этом предусматривается перевод Томторского месторождения при его освоении из разряда пассивного государственного резерва в активный за счет создания складированных и легкодоступных запасов минеральных концентратов и конечной химико-металлургической продукции стратегического значения в соответствии с современной зарубежной практикой. Логика обеспечения экономической и национальной безопасности России обусловливает необходимость проявлений политической воли и финансовой поддержки инициатив таких высокотехнологичных корпораций со смешанным капиталом, как «Ростехнологии» и «Росатом», а также частных компаний, специализированных на производстве легированной металлопродукции, фосфатных удобрений и редких металлов.
- 23 апреля 2025 ОТ «ОБОРОНКИ» ДО СПОРТА: КАК СКАНДИЙ МОЖЕТ ПЕРЕВЕРНУТЬ РОССИЙСКУЮ ПРОМЫШЛЕННОСТЬ
- 18 апреля 2025 ОТ ХАЙПА К ДЕЛУ: КАК РАЗВИВАТЬ РЗМ-ИНДУСТРИЮ В РОССИИ
- 9 апреля 2025 ВЫИГРАТЬ ВСУХУЮ: О НОВЫХ ПОДХОДАХ И ТЕХНОЛОГИЯХ В ОБОГАЩЕНИИ ПОЛЕЗНЫХ ИСКОПАЕМЫХ В ЯКУТИИ
- 26 марта 2025 Арктическое пророчество
- 26 февраля 2025 ПОЯВЛЕНИЕ ЖУРНАЛА “РЕДКИЕ ЗЕМЛИ” ОПЕРЕДИЛО ВРЕМЯ НА 10 ЛЕТ - АКАДЕМИК РАН ВЛАДИСЛАВ ПАНЧЕНКО
- 14 февраля 2025 Редким землям России нужен ТРАМПлин
- 6 февраля 2025 РЕДКИЕ ЗЕМЛИ ЗА СТОЛОМ ПЕРЕГОВОРОВ
- 3 февраля 2025 РАЗДЕЛЯЙ И ЗАРЯЖАЙ
- 26 января 2025 ВЛАДИМИР ВЕРХОВЦЕВ ОТМЕЧАЕТ 70-ЛЕТИЕ
- 27 декабря 2024 МЕЖДУ МИРОМ И ВОЙНОЙ: ЯДЕРНОЕ ОРУЖИЕ ДЛЯ РАЗРУШЕНИЯ И СОЗИДАНИЯ
- 27 октября 2024 ДЛЯ ГЛАВНОЙ НАУКИ БУДУЩЕГО ЧЕЛОВЕЧЕСТВО ДАЖЕ НЕ ПРИДУМАЛО НАЗВАНИЕ
- 13 октября 2024 Форум «Микроэлектроника 2024» – без высокочистых редких металлов никуда
- 23 сентября 2024 ОТ ВОЗРОЖДЕНИЯ МАГНИТНОГО ПРОИЗВОДСТВА К СОЗДАНИЮ НОВОЙ ИНДУСТРИИ В РФ
- 14 сентября 2024 "Задачи будут решены" – О беспилотниках из первых рук
- 31 августа 2024 ВИКТОР САДОВНИЧИЙ: «ЕСЛИ БЫ НЕ МОСКОВСКИЙ УНИВЕРСИТЕТ, РОССИЯ БЫЛА БЫ ДРУГОЙ»