Инновационная технология получения алюминатных люминафоров

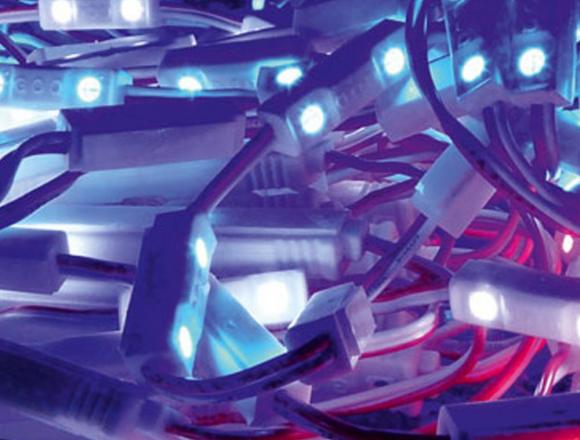
Алюминатные люминофоры, в частности, фотолюминофоры (например, алюминаты стронция), в последние 10—15 лет получили широкое и вполне заслуженное распространение. Связано это с тем, что они обладают высокой степенью аккумуляции энергии и высокой яркостью остаточного послесвечения в темноте. Ресурс их работы физически не ограничен, и поэтому они все более активно завоевывают потребительский рынок.
Несмотря на то что к числу редкоземельных элементов (РЗЭ) относится небольшое количество близких по своим химическим свойствам элементов периодической таблицы, тем не менее сегодня трудно назвать область военной или гражданской отрасли промышленности, использование в которой РЗЭ не давало бы эффективных результатов. К их числу относятся: металлургия, приборостроение, радиоэлектроника, химическая и атомная промышленности, ВПК, авиационно-космическая отрасль и др. При этом для достижения современного уровня решаемых задач, как правило, требуется наличие развитого наукоемкого производства и технологий. Таким образом, доля использования РЗЭ в различных сферах современной промышленности косвенно характеризует уровень развития государства в целом.
Известно, что твердофазный синтез неорганических фотолюминофоров проводится при ступенчатой прокалке, на заключительной стадии которой используются традиционно высокие температуры и длительные циклы выдержки с использованием инертной или окислительно-восстановительной среды и последующим измельчением целевого продукта. Например, алюмоиттриевый гранат (Y3GdCe)3Al5O12) синтезируется в три ступени при температуре на финишной стадии 1520–1600°С и времени выдержки 8–10 часов, синтез алюмината стронция (SrAl2O4:Eu, Dy и Sr4Al14O25:Eu, Dy) проходит в две стадии, на финише выдерживается температура 1320°С в течение 4–6 часов. При этом не обеспечивается получение однородных однофазных структур, что в конечном итоге оказывает негативное влияние на яркость стационарного и спонтанного излучения. Тем не менее к числу наиболее распространенных методов синтеза люминофоров на основе алюминатов стронция относятся классический твердофазный и золь-гель-методы. Реже используются методы горения и индукционного нагрева. В силу изложенных выше причин практически любой используемый способ синтеза не обеспечивает достижения высокого уровня монофазности искомого материала с однородным распределением РЗЭ в его объеме и, как следствие, максимально возможных светотехнических параметров. При этом технологический регламент представляет собой достаточно сложную и многоступенчатую схему, которая, тем не менее, не гарантирует достаточно высокого уровня повторяемости достигаемых параметров. Однако сложность и неоднозначность процессов, характеризующих люминесцентные свойства люминофоров в целом, не позволяет сегодня говорить о приоритетности тех или иных технологических факторов, оказывающих превалирующее влияние на формирование их светотехнических параметров и, в частности, на наноструктурное состояние синтезируемых порошков и их гранулометрический состав.
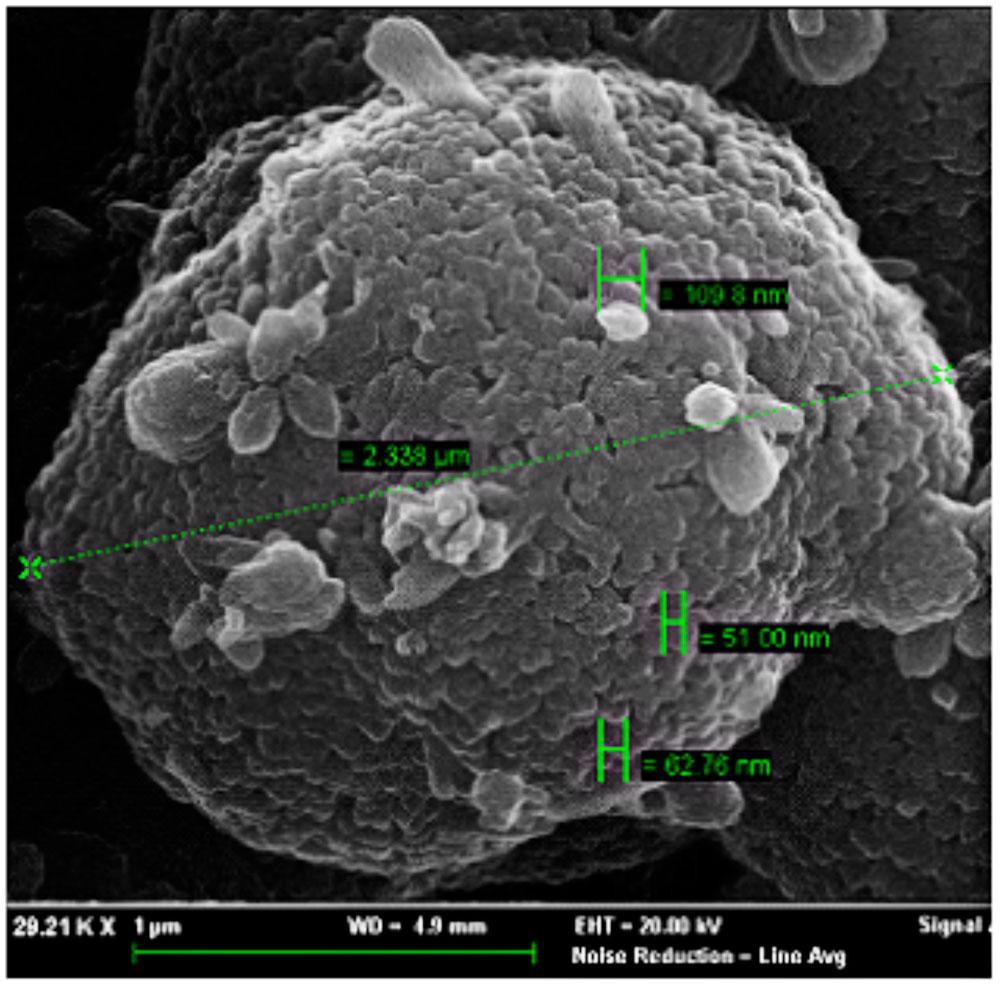
Рис.1.1. Наноструктурный макрообъект
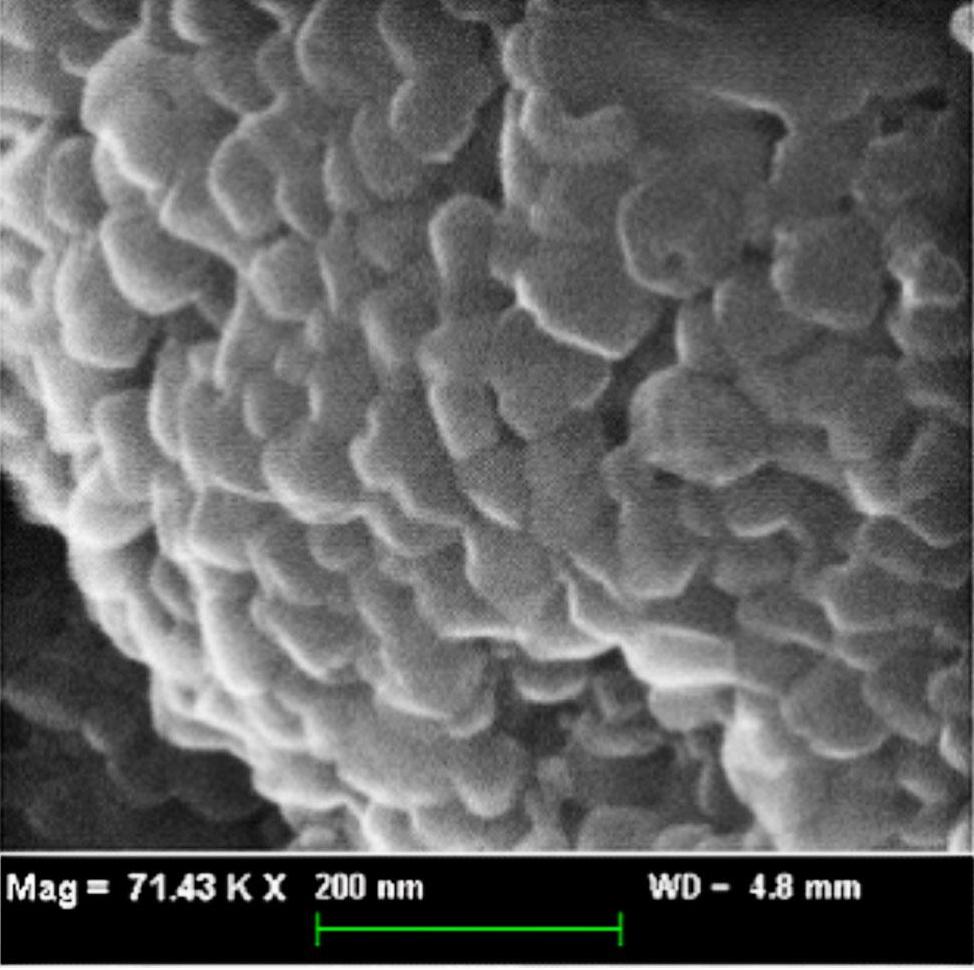
Рис.1.2. Фрагмент наноструктурного макрообъекта диоксида титана
Рис. 1. Формирование наноструктурного макрообъекта по технологии НС на примере диоксида титана
ёПолучение ультра- и нанопорошков для производства функциональной оксидной керамики с улучшенными электрофизическими, химическими и механическими параметрами до сих пор является одной из наиболее актуальных задач керамической технологии, относящихся к числу критических технологий федерального уровня.
Тем не менее современные нанотехнологии в этом вопросе занимают явно лидирующие позиции. Однако то, что большинство этих технологий носит лабораторный характер, говорит об их конструктивном использовании на этапе поиска принципиальных решений стоящих задач, но не обеспечивает быстрой промышленной реализации полученных результатов.
Практическое решение задач указанных критических технологий в части синтеза высококачественных ультра- и нанодисперсных порошков для производства оксидной керамики со стабильным химическим, фазовым и гранулометрическим составом было найдено при разработке технологии непрерывного твердофазного синтеза (HC)[1]. Концептуально непрерывность твердофазного синтеза связана с переносом протекания твердофазных реакций на уровень отдельной гранулы исходной гомогенной механической смеси, вводимой в реакционную камеру, предварительно нагретую до температуры синтеза конкретного оксидного материала. Возникающие при этом термоудар и градиент температур (в начальный момент он достигает 8000–100000 °С /мм) настолько активизируют диффузионные процессы, что завершение твердофазного синтеза осуществляется за период времени, измеряемый минутами, а не часами, как в классическом твердофазном синтезе [1,2]. Исследования показали, что синтезированные по НС порошки оксидных материалов представляют собой совокупность наноструктурных макрообъектов, формируемых из нанофазы путем самосборки (снизу вверх) непосредственно в процессе синтеза. Таким образом, наноструктурный макрообъект не представляет собой цельное кристаллическое образование, а является совокупностью отдельных кристаллических частиц, удерживаемых в рамках объема макрообъекта более значимыми силами, нежели гравитационные. На рис. 1 приведены данные растровой микроскопии перевода стандартного диоксида титана (TiO2) в наноструктурное состояние по непрерывной технологии. При этом размеры наноструктурных макрообъектов и их процентное соотношение между собой регламентируются температурно-временными характеристиками НС. Эта особенность наноструктурных порошков позволяет осуществлять в объеме разрабатываемого композиционного материала локализацию функциональных свойств разной интенсивности, например, магнитных, что, в свою очередь, позволяет создать магнитные жидкости для целей медицинского и технического назначения или радиопоглощающие покрытия и материалы с новыми функциональными возможностями. Практика использования технологии НС для синтеза функциональных материалов позволила выявить причинно-следственные связи между морфологией синтезируемой фазы, скоростью протекания твердофазных реакций, составом и концентрацией газовой среды в реакционной зоне, размером частиц синтезируемой фазы и качеством наноструктурных порошков.Именно эти вопросы поднимают сегодня исследователи люминофоров с целью выявления технологических факторов, влияющих на их светотехнические характеристики. В этой связи особый интерес представляют исследования синтеза люминофоров по технологии НС, тем более что их производство относится к одной из отраслей промышленности, наиболее активно используемых РЗЭ. Для этих целей в качестве модельного материала был выбран алюминат стронция, синтез которого представляет достаточно сложную технологическую задачу.
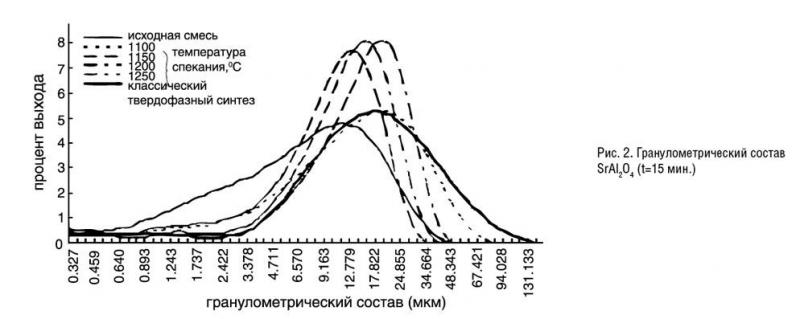
В первую очередь это диктуется:
• критичностью протекания химических реакций в системе SrO–Al2O3 в связи с большим количеством полиморфных превращений исходных реагентов в процессе их термической обработки;
• необходимостью внедрения активаторов и соактиваторов (Eu, Dy и др.) в кристаллическую решетку основания люминофора с формированием определенного их конфигурационного порядка. Анализ результатов синтеза люминофоров на основе алюминатов стронция показал, что уровень вероятности оптимизации их синтеза определяется технологическими возможностями используемого метода синтеза и регламентируется:
• уровнем достигаемой гомогенности исходной механической смеси синтезируемого алюмината стронция;
• дисперсностью и однофазностью используемых реагентов;
• скоростью протекания синтеза искомого материала, а также управляемостью технологических факторов, регламентирующих оптимизацию протекающих процессов. В этой связи особое внимание было уделено твердофазному синтезу алюминатов стронция с использованием плавней, то есть в присутствии жидкой фазы. Связано это с тем, что синтез в присутствии жидкой фазы, как правило, протекает на более высоком качественном уровне, позволяя при этом существенно снизить температуру синтеза как таковую. При этом надо понимать, что не любая жидкая фаза обеспечивает оптимальное решение стоящей задачи. Связано это с тем, что в процессе термообработки жидкая фаза, вступая в контакт с реагентами исходной механической смеси синтезируемого материала, образует промежуточные фазы и не всегда способствует формированию монофазности целевого продукта. Так, например, использование борной кислоты в качестве плавня для синтеза алюминатов стронция в процессе термообработки провоцирует формирование боратов и алюмоборатов стронция сложного состава с последующим их распадом, что, естественно, не упрощает технологический регламент синтеза монофазного алюмината стронция. Тем не менее использование жидкой фазы на этапе синтеза позволяет повышать качество как фазового состава, так и порошков синтезируемых материалов. В общем случае использование подобных спецстекол позволяет осуществлять твердофазный синтез в присутствии минимального количества жидкой фазы. Достигаемая при этом эффективность определяется степенью вероятности оптимизации баланса активности спецстекла целевого назначения по отношению к синтезируемому материалу, что в конечном итоге и позволяет простоту твердофазного синтеза дополнить достоинством жидкофазного синтеза, а именно ускорением процессов переноса и повышением гомогенности искомого продукта.
Исходя из вышеизложенного, для синтеза алюмината стронция были использованы карбонат стронция (SrСO3), оксид алюминия (Al2O3) квалификации «х.ч.» и предварительно подготовленное спецстекло целевого назначения. Гомогенизация исходной механической смеси (ИМС) осуществлялась по обычной керамической технологии путем смешения исходных реагентов с использованием дистиллированной воды. Синтез алюмината стронция осуществлялся по технологии непрерывного твердофазного синтеза (НС) в интервале температур до 12500С и времени синтеза до 30 минут. Гранулометрический состав синтезированных порошков определялся на лазерном анализаторе частиц Analysette 22, а рентгенофазовый анализ — на дифрактометре ARL X’TRA (Сukα-излучение).
Из анализа сравнительных данных гранулометрических составов порошков алюмината стронция в рамках проводимых экспериментов (рис. 2) следует:
• гранулометрический состав порошков, синтезированный по классическому твердофазному синтезу (КТС), практически совпадает с гранулометрическим составом порошков, синтезированных по НС при температуре синтеза 11000С в течение 15 мин. Синтез алюмината стронция по КТС осуществлялся с использованием той же партии ИМС;
• гранулометрические составы порошков, синтезированных в интервале температур от 1150 до 12500С и времени синтеза 15 минут, имеют тенденцию к смещению в сторону роста размеров исследуемых порошков. Полученные данные хорошо согласуются с общей моделью формирования наноструктурных макрообъектов оксидных материалов в процессе непрерывного твердофазного синтеза, согласно которой:
• температура синтеза оказывает превалирующее влияние на размеры формируемых наноструктурных макрообъектов,
• а время синтеза — на оптимальное соотношение между ними.
При этом фазовый состав порошков, синтезированных в интервале температур спекания 1175–12250С в присутствии спецстекла целевого назначения в количестве 0,5–0,75% масс. (обычно вводят 2–8% масс.) и времени синтеза 25–30 минут, соответствует 99±0,5% целевого продукта, что говорит о высокой гомогенности синтезированного алюмината стронция.
На рис. 3 приведены дифрактограммы алюмината стронция, cинтезированного по непрерывной и классической твердофазным технологиям (рис. 3а, 3с соответственно)[3].
Сравнительный анализ приведенных дифрактограмм со штрих-диаграммой международного стандарта (рис. 3б) говорит в пользу монофазности алюмината стронция, синтезированного по технологии НС в присутствии жидкой фазы.
Как видно из приведенных данных, использование эффективных наукоемких технологий позволяет решать не только задачи общего и специального назначения на более высоком качественном уровне, но и более активно содействовать оперативному наполнению внутреннего рынка наукоемкой продукцией.
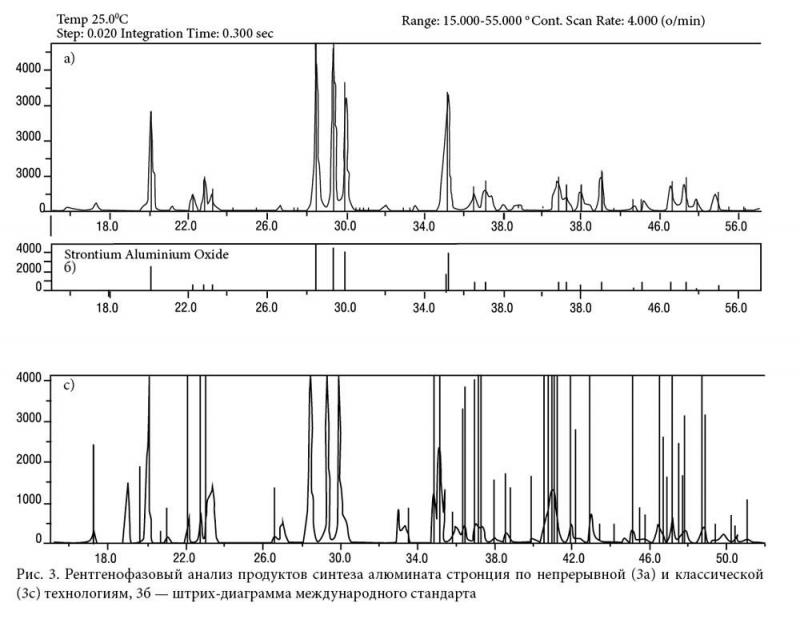
Преимущества предлагаемого решения по техническим, потребительским и экономическим показателям по сравнению с известными отечественными аналогами показаны в таблице.
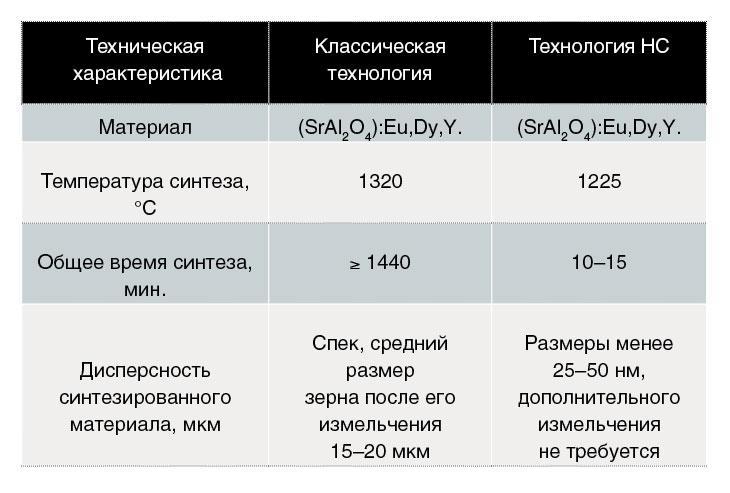
С точки зрения технологии реализация принципа непрерывности может быть представлена следующей последовательностью действий [4]:
• непрерывная загрузка гранулированной механической смеси в реакционную камеру, предварительно нагретую до температуры синтеза;
• обеспечение изотермической выдержки в соответствии с температурно-временными характеристиками синтеза в условиях непрерывности технологического процесса;
• обеспечение непрерывности удаления синтезированного материала из реакционной камеры за ее пределы;
• обеспечение непрерывности поступления и удаления синтезированного материала из накопителя (приемника).
Текст:
Борис Моисеевич Кербель, профессор, доктор технических наук, директор НОЦ «Технологии и материалы атомного энергопромышленного комплекса» Северского технологического института НИЯУ МИФИ;
Леонид Михайлович Кацнельсон, кандидат физико-математических наук, генеральный директор
ООО НПП «Технологика», г. Ростов-на-Дону
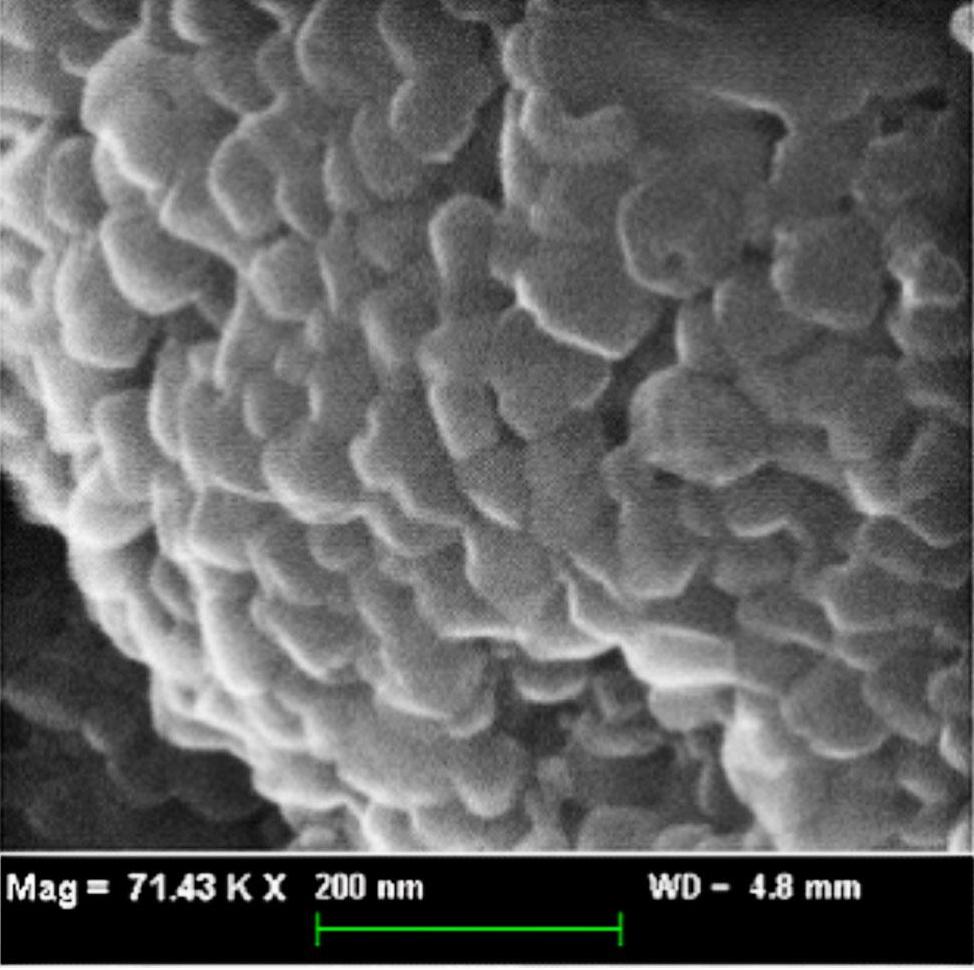
Рис.1.2. Фрагмент наноструктурного макрообъекта диоксида титана
Рис. 1. Формирование наноструктурного макрообъекта по технологии НС на примере диоксида титана
ёПолучение ультра- и нанопорошков для производства функциональной оксидной керамики с улучшенными электрофизическими, химическими и механическими параметрами до сих пор является одной из наиболее актуальных задач керамической технологии, относящихся к числу критических технологий федерального уровня.
Тем не менее современные нанотехнологии в этом вопросе занимают явно лидирующие позиции. Однако то, что большинство этих технологий носит лабораторный характер, говорит об их конструктивном использовании на этапе поиска принципиальных решений стоящих задач, но не обеспечивает быстрой промышленной реализации полученных результатов.
Практическое решение задач указанных критических технологий в части синтеза высококачественных ультра- и нанодисперсных порошков для производства оксидной керамики со стабильным химическим, фазовым и гранулометрическим составом было найдено при разработке технологии непрерывного твердофазного синтеза (HC)[1]. Концептуально непрерывность твердофазного синтеза связана с переносом протекания твердофазных реакций на уровень отдельной гранулы исходной гомогенной механической смеси, вводимой в реакционную камеру, предварительно нагретую до температуры синтеза конкретного оксидного материала. Возникающие при этом термоудар и градиент температур (в начальный момент он достигает 8000–100000 °С /мм) настолько активизируют диффузионные процессы, что завершение твердофазного синтеза осуществляется за период времени, измеряемый минутами, а не часами, как в классическом твердофазном синтезе [1,2]. Исследования показали, что синтезированные по НС порошки оксидных материалов представляют собой совокупность наноструктурных макрообъектов, формируемых из нанофазы путем самосборки (снизу вверх) непосредственно в процессе синтеза. Таким образом, наноструктурный макрообъект не представляет собой цельное кристаллическое образование, а является совокупностью отдельных кристаллических частиц, удерживаемых в рамках объема макрообъекта более значимыми силами, нежели гравитационные. На рис. 1 приведены данные растровой микроскопии перевода стандартного диоксида титана (TiO2) в наноструктурное состояние по непрерывной технологии. При этом размеры наноструктурных макрообъектов и их процентное соотношение между собой регламентируются температурно-временными характеристиками НС. Эта особенность наноструктурных порошков позволяет осуществлять в объеме разрабатываемого композиционного материала локализацию функциональных свойств разной интенсивности, например, магнитных, что, в свою очередь, позволяет создать магнитные жидкости для целей медицинского и технического назначения или радиопоглощающие покрытия и материалы с новыми функциональными возможностями. Практика использования технологии НС для синтеза функциональных материалов позволила выявить причинно-следственные связи между морфологией синтезируемой фазы, скоростью протекания твердофазных реакций, составом и концентрацией газовой среды в реакционной зоне, размером частиц синтезируемой фазы и качеством наноструктурных порошков.Именно эти вопросы поднимают сегодня исследователи люминофоров с целью выявления технологических факторов, влияющих на их светотехнические характеристики. В этой связи особый интерес представляют исследования синтеза люминофоров по технологии НС, тем более что их производство относится к одной из отраслей промышленности, наиболее активно используемых РЗЭ. Для этих целей в качестве модельного материала был выбран алюминат стронция, синтез которого представляет достаточно сложную технологическую задачу.
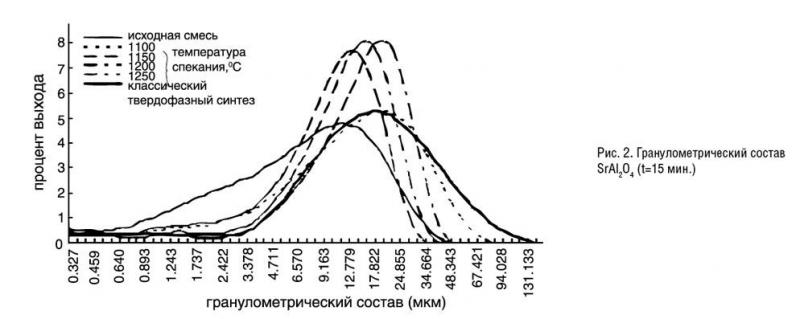
В первую очередь это диктуется:
• критичностью протекания химических реакций в системе SrO–Al2O3 в связи с большим количеством полиморфных превращений исходных реагентов в процессе их термической обработки;
• необходимостью внедрения активаторов и соактиваторов (Eu, Dy и др.) в кристаллическую решетку основания люминофора с формированием определенного их конфигурационного порядка. Анализ результатов синтеза люминофоров на основе алюминатов стронция показал, что уровень вероятности оптимизации их синтеза определяется технологическими возможностями используемого метода синтеза и регламентируется:
• уровнем достигаемой гомогенности исходной механической смеси синтезируемого алюмината стронция;
• дисперсностью и однофазностью используемых реагентов;
• скоростью протекания синтеза искомого материала, а также управляемостью технологических факторов, регламентирующих оптимизацию протекающих процессов. В этой связи особое внимание было уделено твердофазному синтезу алюминатов стронция с использованием плавней, то есть в присутствии жидкой фазы. Связано это с тем, что синтез в присутствии жидкой фазы, как правило, протекает на более высоком качественном уровне, позволяя при этом существенно снизить температуру синтеза как таковую. При этом надо понимать, что не любая жидкая фаза обеспечивает оптимальное решение стоящей задачи. Связано это с тем, что в процессе термообработки жидкая фаза, вступая в контакт с реагентами исходной механической смеси синтезируемого материала, образует промежуточные фазы и не всегда способствует формированию монофазности целевого продукта. Так, например, использование борной кислоты в качестве плавня для синтеза алюминатов стронция в процессе термообработки провоцирует формирование боратов и алюмоборатов стронция сложного состава с последующим их распадом, что, естественно, не упрощает технологический регламент синтеза монофазного алюмината стронция. Тем не менее использование жидкой фазы на этапе синтеза позволяет повышать качество как фазового состава, так и порошков синтезируемых материалов. В общем случае использование подобных спецстекол позволяет осуществлять твердофазный синтез в присутствии минимального количества жидкой фазы. Достигаемая при этом эффективность определяется степенью вероятности оптимизации баланса активности спецстекла целевого назначения по отношению к синтезируемому материалу, что в конечном итоге и позволяет простоту твердофазного синтеза дополнить достоинством жидкофазного синтеза, а именно ускорением процессов переноса и повышением гомогенности искомого продукта.
Исходя из вышеизложенного, для синтеза алюмината стронция были использованы карбонат стронция (SrСO3), оксид алюминия (Al2O3) квалификации «х.ч.» и предварительно подготовленное спецстекло целевого назначения. Гомогенизация исходной механической смеси (ИМС) осуществлялась по обычной керамической технологии путем смешения исходных реагентов с использованием дистиллированной воды. Синтез алюмината стронция осуществлялся по технологии непрерывного твердофазного синтеза (НС) в интервале температур до 12500С и времени синтеза до 30 минут. Гранулометрический состав синтезированных порошков определялся на лазерном анализаторе частиц Analysette 22, а рентгенофазовый анализ — на дифрактометре ARL X’TRA (Сukα-излучение).
Из анализа сравнительных данных гранулометрических составов порошков алюмината стронция в рамках проводимых экспериментов (рис. 2) следует:
• гранулометрический состав порошков, синтезированный по классическому твердофазному синтезу (КТС), практически совпадает с гранулометрическим составом порошков, синтезированных по НС при температуре синтеза 11000С в течение 15 мин. Синтез алюмината стронция по КТС осуществлялся с использованием той же партии ИМС;
• гранулометрические составы порошков, синтезированных в интервале температур от 1150 до 12500С и времени синтеза 15 минут, имеют тенденцию к смещению в сторону роста размеров исследуемых порошков. Полученные данные хорошо согласуются с общей моделью формирования наноструктурных макрообъектов оксидных материалов в процессе непрерывного твердофазного синтеза, согласно которой:
• температура синтеза оказывает превалирующее влияние на размеры формируемых наноструктурных макрообъектов,
• а время синтеза — на оптимальное соотношение между ними.
При этом фазовый состав порошков, синтезированных в интервале температур спекания 1175–12250С в присутствии спецстекла целевого назначения в количестве 0,5–0,75% масс. (обычно вводят 2–8% масс.) и времени синтеза 25–30 минут, соответствует 99±0,5% целевого продукта, что говорит о высокой гомогенности синтезированного алюмината стронция.
На рис. 3 приведены дифрактограммы алюмината стронция, cинтезированного по непрерывной и классической твердофазным технологиям (рис. 3а, 3с соответственно)[3].
Сравнительный анализ приведенных дифрактограмм со штрих-диаграммой международного стандарта (рис. 3б) говорит в пользу монофазности алюмината стронция, синтезированного по технологии НС в присутствии жидкой фазы.
Как видно из приведенных данных, использование эффективных наукоемких технологий позволяет решать не только задачи общего и специального назначения на более высоком качественном уровне, но и более активно содействовать оперативному наполнению внутреннего рынка наукоемкой продукцией.
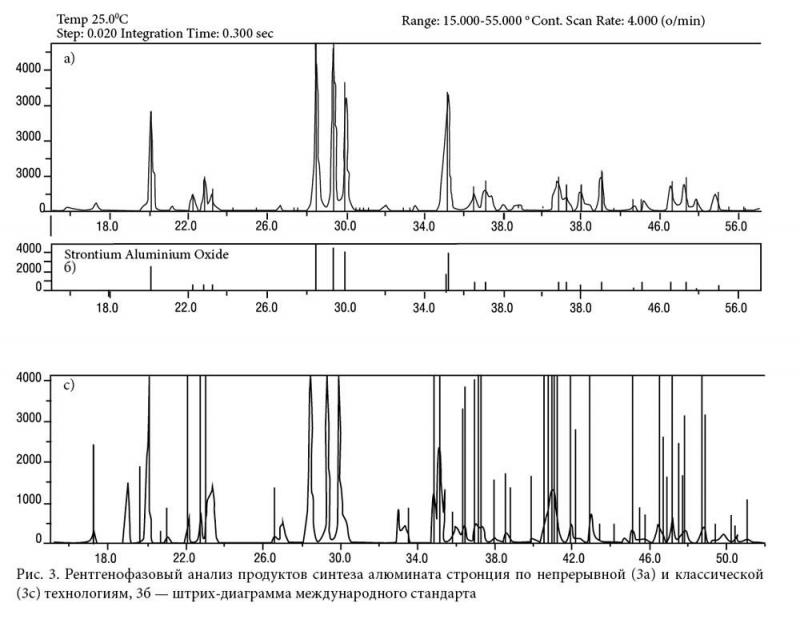
Преимущества предлагаемого решения по техническим, потребительским и экономическим показателям по сравнению с известными отечественными аналогами показаны в таблице.
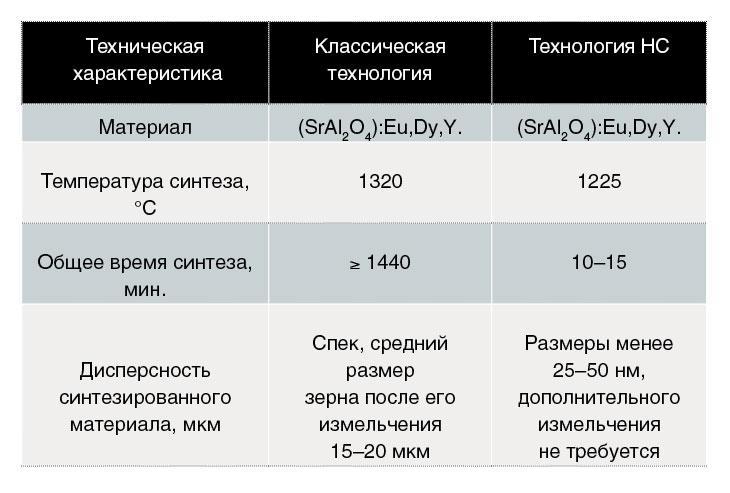
С точки зрения технологии реализация принципа непрерывности может быть представлена следующей последовательностью действий [4]:
• непрерывная загрузка гранулированной механической смеси в реакционную камеру, предварительно нагретую до температуры синтеза;
• обеспечение изотермической выдержки в соответствии с температурно-временными характеристиками синтеза в условиях непрерывности технологического процесса;
• обеспечение непрерывности удаления синтезированного материала из реакционной камеры за ее пределы;
• обеспечение непрерывности поступления и удаления синтезированного материала из накопителя (приемника).
Текст:
Борис Моисеевич Кербель, профессор, доктор технических наук, директор НОЦ «Технологии и материалы атомного энергопромышленного комплекса» Северского технологического института НИЯУ МИФИ;
Леонид Михайлович Кацнельсон, кандидат физико-математических наук, генеральный директор
ООО НПП «Технологика», г. Ростов-на-Дону
- 23 апреля 2025 ОТ «ОБОРОНКИ» ДО СПОРТА: КАК СКАНДИЙ МОЖЕТ ПЕРЕВЕРНУТЬ РОССИЙСКУЮ ПРОМЫШЛЕННОСТЬ
- 18 апреля 2025 ОТ ХАЙПА К ДЕЛУ: КАК РАЗВИВАТЬ РЗМ-ИНДУСТРИЮ В РОССИИ
- 9 апреля 2025 ВЫИГРАТЬ ВСУХУЮ: О НОВЫХ ПОДХОДАХ И ТЕХНОЛОГИЯХ В ОБОГАЩЕНИИ ПОЛЕЗНЫХ ИСКОПАЕМЫХ В ЯКУТИИ
- 26 марта 2025 Арктическое пророчество
- 26 февраля 2025 ПОЯВЛЕНИЕ ЖУРНАЛА “РЕДКИЕ ЗЕМЛИ” ОПЕРЕДИЛО ВРЕМЯ НА 10 ЛЕТ - АКАДЕМИК РАН ВЛАДИСЛАВ ПАНЧЕНКО
- 14 февраля 2025 Редким землям России нужен ТРАМПлин
- 6 февраля 2025 РЕДКИЕ ЗЕМЛИ ЗА СТОЛОМ ПЕРЕГОВОРОВ
- 3 февраля 2025 РАЗДЕЛЯЙ И ЗАРЯЖАЙ
- 26 января 2025 ВЛАДИМИР ВЕРХОВЦЕВ ОТМЕЧАЕТ 70-ЛЕТИЕ
- 27 декабря 2024 МЕЖДУ МИРОМ И ВОЙНОЙ: ЯДЕРНОЕ ОРУЖИЕ ДЛЯ РАЗРУШЕНИЯ И СОЗИДАНИЯ
- 27 октября 2024 ДЛЯ ГЛАВНОЙ НАУКИ БУДУЩЕГО ЧЕЛОВЕЧЕСТВО ДАЖЕ НЕ ПРИДУМАЛО НАЗВАНИЕ
- 13 октября 2024 Форум «Микроэлектроника 2024» – без высокочистых редких металлов никуда
- 23 сентября 2024 ОТ ВОЗРОЖДЕНИЯ МАГНИТНОГО ПРОИЗВОДСТВА К СОЗДАНИЮ НОВОЙ ИНДУСТРИИ В РФ
- 14 сентября 2024 "Задачи будут решены" – О беспилотниках из первых рук
- 31 августа 2024 ВИКТОР САДОВНИЧИЙ: «ЕСЛИ БЫ НЕ МОСКОВСКИЙ УНИВЕРСИТЕТ, РОССИЯ БЫЛА БЫ ДРУГОЙ»