Без рения ракеты не летают

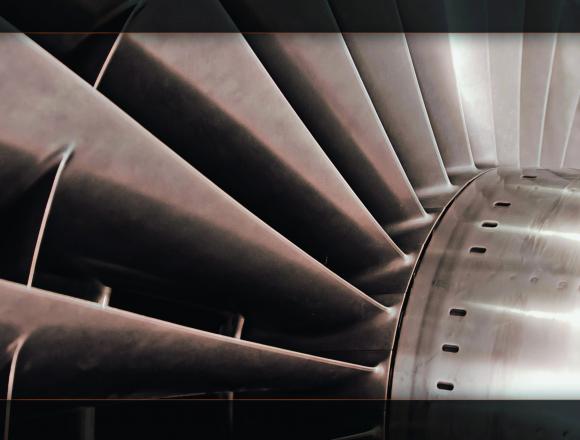
Рения в мире катастрофически мало. Но этот металл незаменим, скажем, в производстве ракетно-космической техники. Его используют для изготовления частей ракетных сопел, носовых насадок ракет, теплозащитных экранов многоразовых космических аппаратов и т.д. Рений позарез нужен в нефтехимической промышленности. Какими способами добыть этот редчайший металл, если учесть, что все производства первичного рения с распадом ссср остались за пределами России? Как уменьшить зависимость нашей промышленности, ее обороноспособности от импорта этого стратегически важного металл? На эти вопросы и пытаются ответить авторы данной статьи.
Немногие слышали о таком металле, как рений, – редком и рассеянном, дорогостоящем и стратегически важном. Тем не менее этот металл на сегодняшний день является одним из важнейших в аэрокосмической индустрии. Дело в том, что только благодаря уникальным свойствам рения стало возможным создание газотурбинных авиадвигателей для самолетов последних поколений — сверхмощных и экономичных. Рений является незаменимым компонентом суперсплавов — жаропрочных никелевых сплавов (ЖНС), способных работать в экстремальных условиях реактивных двигателей — при температурах порядка 1200°С. Суперсплавы рения с тугоплавкими металлами — вольфрамом, молибденом, танталом — имеют высокую твердость и пластичность при температурах 2000–3000°С, что позволяет использовать их в ракетно-космической технике для изготовления частей ракетных сопел, носовых насадок ракет, деталей термоионных двигателей, теплозащитных экранов многоразовых кос-
мических аппаратов и др. Обладание самым современным авиапарком, сочетающим последние достижения отечественной и мировой науки, напрямую связано с обороноспособностью страны; создание уникальных космических аппаратов позволяет России поддерживать звание ведущей космической державы. Очевидно, что области применения рения являются стратегически важными направлениями.
При этом рений является одним из наиболее редких и рассеянных элементов на Земле. Среднее содержание рения в земной коре крайне мало — 7×10-8%, что примерно в 5 раз меньше, чем содержание золота и платины. Основные производства этого металла находятся в Чили, США, Перу и Польше и приурочены к медно-молибденовой индустрии. Как выражаются специалисты, рений — дважды попутный металл. Те небольшие объемы рения, которые ежегодно вырабатывают в мире из первичного сырья (а это не более 50 т в год), получают преимущественно из медно-молибденового сырья. При этом сначала из руд получают медный и молибденовый концентраты, и только затем, из концентратов (главным образом — молибденового), выделяют рений. Таким образом, первичное производство этого металла зависит не столько от спроса на рений на мировом рынке, сколько от объемов производства меди и молибдена, обусловленных,соответственно, спросом на последние. Это обуславливает практическую невозможность заметного увеличения производства рения из традиционного сырья.
В то же время спрос на этот металл со стороны производителей суперсплавов постоянно возрастает. С начала использования рения в качестве легирующего элемента в составе суперсплавов с конца 1980-х годов сменилось три поколения сплавов, содержание рения в них увеличилось: с 2–3% в сплавах второго поколения до 4–9% в сплавах третьего и четвертого. Доля производителей сплавов в структуре потребления рения в 2012 году достигала 83,3%.
На высоком уровне остается спрос на металл и во второй по объему области потребления рения — нефтехимии, где рений используется главным образом в составе платино-рениевых катализаторов риформинга в производстве неэтилированного (не содержащего свинца) высокооктанового бензина. Несмотря на огромные объемы нефтепереработки, потребность в рении в этой отрасли относительно небольшая благодаря рециклингу, в котором теряется не более 10% рения. По последним данным, нефтехимическая промышленность ежегодно дополнительно потребляет порядка 5 тонн перрената аммония. Тем не менее, с учетом разработки новых ренийсодержащих катализаторов оргсинтеза, в том числе для перспективных GTL-технологий (ожижение газа, Gas-To-Liquid), можно ожидать в перспективе повышения спроса на рений в этом секторе.
Напряженность на рынке рения сохраняется уже длительное время, что привело к значительному росту цен, особенно до 2008 года, когда они достигали, по некоторым данным, 12 тыс. долл. за килограмм. Сейчас цены несколько снизились: по данным на январь 2013 года они составляли 3,5–3,7 тыс. долл. за кг, тем не менее, рений остается одним из самых дорогих промышленных металлов.[1]
В условиях сырьевой базы России вопрос дефицита рения стоит особенно остро, поскольку производства первичного рения с распадом СССР отошли к союзным государствам (Казахстан, Узбекистан, Армения). И несмотря на то, что именно в России находится единственное собственно рениевое месторождение, третье в мире по запасам этого металла, — фурамольные поля вулкана Кудрявый, о. Итуруп Курильской гряды, отечественная промышленность в большой степени зависима от импорта металла. Это связано с отсутствием на сегодняшний день промышленных технологий, позволяющих извлекать рений «из вулкана». Хотя среднее содержание рения в вулканических породах месторождения ~30 г/т (на отдельных участках до 1000 г/т)[2], что является промышленно значимой концентрацией, породы фурамольных полей находятся вблизи кратера действующего вулкана. Также рений присутствует в горячих парогазовых выбросах из кратера вулкана. Извлечение металла из таких источников является далеко не тривиальной задачей. Предложенные российскими учеными технологии улавливания рения из парогазовых выбросов вулкана пока находятся на стадии пилотных испытаний. В настоящее время производство рения в России ограничено лишь скромными объемами получаемого при переработке вторичного рений содержащего сырья металла, по разным оценкам не превышающими 0,5–1,5 т.
Несмотря на бурное развитие и совершенствование ренийсодержащих ЖНС, централизованная переработка отходов таких сплавов в России пока не налажена и осуществляется на отдельных малых предприятиях в опытно-промышленном масштабе.[3] В то же время за рубежом сложилась практика «рециклинга замкнутого цикла»[4] в области использования ренийсодержащих никелевых суперсплавов, когда крупнейшие производители авиадвигателей, такие как General Electric, налаживают сбор отработавших деталей из ренийсодержащих ЖНС у своих клиентов по всему миру и ведут их переработку на собственных мощностях.
В отличие от суперсплавов, применение в нашей стране платино-рениевых катализаторов нефтехимии имеет более богатую историю и широкие масштабы в связи с большими объемами нефтепереработки. Первые отечественные ренийсодержащие катализаторы были разработаны в начале 1970-х годов НПО «Леннефтехим», и уже в 1976 году была выпущена первая промышленная партия платино-рениевого катализатора КР–104, содержавшего 0,36% платины и 0,20% рения. Позднее были внедрены катализаторы марок КР–108 и КР–110 с модифицированным носителем. Процесс реформинга на алюмо-платино-рениевых катализаторах получил название «рениформинг». По состоянию на 1990 год, в СССР на полиметаллических катализаторах марки КР работало 44 завода и 99 установок.[5]
Катализаторы рениформинга относятся к нанесенным катализаторам, представляющим собой гранулы из оксида алюминия — так называемую «подложку», с нанесенными (адсорбированными) на поверхность каталитическими металлами, в случае биметаллических катализаторов — рением и платиной. Содержание ценных металлов в катализаторе невелико и обычно не превышает 0,3–0,4% по массе. В процессе эксплуатации на установках рениформинга катализаторы подвергаются действию контактных ядов и отложению кокса на поверхности, что ведет к снижению их каталитических свойств. Несмотря на то что в промышленности используются технологии регенерации катализаторов, средняя продолжительность «жизни» платино-рениевых катализаторов (с регенерациями) до дезактивации и необходимости их замены редко превышает 3–5 лет. Дезактивированные (или «отработанные») катализаторы традиционно подвергают утилизации с извлечением ценных компонентов и возвращением их
в технологическую цепочку.
В России в перестроечные годы сложилась особая ситуация с переработкой отработанных катализаторов рениформинга. Государство передало переработку такого сырья в частные руки, которые не были заинтересованы в извлечении рения. В последние годы рост цен на этот металл заставил перерабатывающие предприятия направить усилия на максимально эффективное извлечение из катализаторов не только платины, но и рения.
Существующие технологические схемы переработки алюмо-платино-рениевых катализаторов можно условно разделить на две группы:[5]
1 — с разложением алюмооксидной основы катализатора;
2 — с селективным извлечением ценных компонентов (без разложения основы).
Оба подхода, как правило, сочетают пиро- и гидрометаллургические операции на различных этапах технологического процесса.
Для разложения алюмооксидной подложки катализатора могут быть использованы концентрированные растворы минеральных кислот и щелочей, причем процесс более эффективно проходит в условиях повышенных температур и давления, создаваемых при автоклавном выщелачивании. В последнее время также активно изучается возможность использования микроволнового излучения для интенсификации процессов растворения. При этом, в зависимости от условий проведения процесса, либо могут быть получены концентраты одного или обоих ценных компонентов в нерастворимом остатке, которые далее перерабатываются в аффинажном производстве, либо компоненты катализатора полностью переводятся в раствор, откуда платину и рений выделяют методами осаждения или ионообменной сорбцией.
Переработка отработанных платинорениевых катализаторов со щелочным разложением основы использована на ЗАО «Промышленные катализаторы» (г. Рязань), где получают 5–25%-ный концентрат драгоценных металлов в нерастворимом остатке, а раствор алюмината натрия используют для производства носителей новых катализаторов, а также адсорбентов и осушителей.
Для полного растворения катализатора применяют также плавиковую или соляную кислоты (с окислителем). В этом случае для выделения концентратов металлов из алюминатных растворов используют осадительные методы.
Другим вариантом полного разложения алюмооксидной основы катализатора является спекание его со щелочными реагентами (щелочью, содой и др.) в присутствии окислителей или восстановителей с последующим выщелачиванием спека водными растворами.
Один из вариантов технологии, основанной на спекании катализаторов со щелочью, был опробован несколько лет назад на ОАО «Красцветмет» при переработке катализаторов КР 108 и КР 110. При водном выщелачивании спека в раствор переводился алюминий и рений, последний выделяли в концентрат цементацией на железном порошке. Полученный обогащенный по рению продукт содержал 2–19% Re, <0.1% Pt, 4-13% Fe, 4–10% Al и далее был переработан на перренат аммония, соответствующий требованиям ТУ–48–7–1–90. Промышленной группой «Редмет» (г. Новосибирск) из раствора от растворения спека рений извлекают ионообменной сорбцией. Платину из остатка выделяют методом гидрохлорирования.
Для реализации второго подхода к переработке дезактивированных катализаторов рениформинга – селективного извлечения ценных компонентов, также могут быть применены как пиро-, так и гидрометаллургические методы. Наиболее простой вариант — выщелачивание рения из катализаторов разбавленной серной кислотой. Такой прием был использован в технологии, испытанной на комбинате «Североникель» ОАО Кольская ГМК в 1980–90 х гг. Извлечение рения в слабокислый раствор выщелачивания составляло 96–97%, алюминий и платина оставались в остатке, который далее перерабатывался в технологической цепочке комбината в печах КС рафинировочного цеха. Рений из растворов выделяли анионообменной сорбцией на смоле ВП-14П.
Похожая схема была внедрена в 2003 году на Кыштымском медно-электролитном комбинате (ОАО «Русская медная компания») с тем отличием, что здесь для извлечения рения использовалась более современная селективная анионообменная смола Purolite A170.
Также селективное извлечение в раствор ценных компонентов катализаторов возможно при выщелачивании солянокислыми растворами в присутствии окислителя, слабокислыми растворами смеси соляной и азотной кислот, и даже растворами соды. Процессы в отдельных случаях предложено интенсифицировать путем использования автоклава. В последнее время в гидрометаллургии популярно направление сольвометаллургии — выщелачивания органическими жидкостями, и для селективного извлечения рения из отработанных катализаторов предложен метод хлорирования в диметилформамиде. Тем не менее такие экзотические методики пока не нашли промышленного применения.
С начала 1980-х гг. изучалась возможность выделения каталитических металлов из дезактивированных алюмо-платино-рениевых катализаторов электролизом. Предложены электрохимические технологии селективного перевода в раствор рения в хлоридном электролите, совместного перевода в раствор рения и платины в солянокислом или смешанном соляно-сернокислом электролитах, причем в последнем случае возможно одновременное выделение элементов на катоде в металлической форме. При электрохимической переработке алюмооксидная основа катализатора практически не затрагивается и может быть использована для изготовления новых партий катализаторов. Получаемые на катоде металлические платино-рениевые осадки могут быть использованы для приготовления новых катализаторов. Кроме того, наложение электрического тока приводит к интенсификации процессов, что в свою очередь позволяет использовать менее концентрированные растворы, снижает расход реагентов и упрощает их дальнейшую утилизацию. Несмотря на очевидные достоинства электрохимических технологий, данные об их промышленном использовании отсутствуют.
Наконец, одним из методов селективного извлечения рения из дезактивированных катализаторов является его высокотемпературная окислительная отгонка в виде летучей семиокиси рения. Преимуществом такой схемы является то, что при прокаливании катализатора при температуре выше 1000 °С происходит не только отгонка рения, но и фазовый переход алюмооксидной подложки Al2O3 из «гамма»- в «альфа»-форму, которая отличается повышенной химической стойкостью, а также переход платины в менее упорную форму, что положительно сказывается на их дальнейшем разделении в процессе выщелачивания.
В промышленности процесс окислительной отгонки рения, по существу, реализовывался на комбинате «Североникель» ОАО Кольская ГМК, когда дезактивированные катализаторы подавали в технологическую цепочку основного производства в печи «кипящего слоя». При этом рений вместе с обжиговыми газами поступал в сернокислотный цех, где практически полностью улавливался растворами мокрого пылегазоулавливания (МПУ). Однако из-за отсутствия эффективной технологии выделения рения из растворов МПУ на предприятии практическая эксплуатация такой схемы невозможна. В последние годы в ИХТРЭМС КНЦ РАН было разработано несколько вариантов технологии извлечения рения из растворов МПУ комбината «Североникель» ОАО Кольская ГМК, основанных на жидкостной экстракции, однако пока они остаются невостребованными отечественной промышленностью.
Таким образом, на примере обзора технологий отработанных катализаторов можно видеть, что технических решений для извлечения такого ценного металла, как рений, из вторичного сырья на сегодняшний день более чем достаточно. В то же время внедрены только отдельные технологии, и такое сырье в России на деле перерабатывается на ограниченном числе предприятий, обслуживающих, как правило, внутриотраслевые нужды (регенерированный перренат аммония идет на изготовление катализаторов).
В свете вышеизложенного очевидно, что для укрепления обороноспособности страны необходимо изыскать возможности для снижения зависимости промышленности России от импорта рения как стратегически важного металла. Для этого необходимо направить усилия на разработку новейших технологий, позволяющих организовать добычу металла из «трудных» месторождений, нетрадиционных сырьевых источников, а также увеличить рециклинг рения из вторичного сырья.
В заключении хочется отметить, что хорошие новости все же приходят и из отечественного перерабатывающего сектора. В марте 2013 года в СМИ появились данные, что к 2014 году в Екатеринбурге ГК «Металлургия благородных металлов» планирует построить производственный комплекс по переработке дезактивированных катализаторов нефтяной промышленности. По-видимому, предполагается использовать вариант высокотемпературной окислительной отгонки рения с переработкой огарка по одной из аффинажных схем. Заявлено, что технология утилизации будет «более экологичной, чем все используемые в настоящее время».
[1] Vulcan T. Rare metal rhenium’s toughness under heat and pressure key attraction as super-alloy & turbine material (April 03, 2013) / www.hardassetsinvestor.com/features/4666-rare-metal-rheniums…
[2] Палант А.А., Трошкина И.Д., Чекмарев А.М. Металлургия рения. М.: «Наука», 2007. 298 с.
[3] Касиков А.Г., Петрова А.М. Рециклинг рения из отходов жаропрочных и специальных сплавов // Технология металлов. 2010. №2. С. 2-12.
[4] Rhenium reduction program: using less of a rare mineral / https://citizenship.geblogs.com/rheniumreduction-program-using-less-of-a-rare-mineral
[5] Касиков А.Г., Петрова А.М. Переработка дезактивированных платино-рениевых катализаторов // Хим. технология. 2008. Т. 9. №8. С. 376-385.
Текст: А.М. Петрова — к.т.н., науч. сотрудник ИХТРЭМС КНЦ РАН, А.Г. Касиков — к.х.н., зав. сектором гидрометаллургии ИХТРЭМС КНЦ РАН (г. Апатиты)
Фото: Йен Алессон
- 23 апреля 2025 ОТ «ОБОРОНКИ» ДО СПОРТА: КАК СКАНДИЙ МОЖЕТ ПЕРЕВЕРНУТЬ РОССИЙСКУЮ ПРОМЫШЛЕННОСТЬ
- 18 апреля 2025 ОТ ХАЙПА К ДЕЛУ: КАК РАЗВИВАТЬ РЗМ-ИНДУСТРИЮ В РОССИИ
- 9 апреля 2025 ВЫИГРАТЬ ВСУХУЮ: О НОВЫХ ПОДХОДАХ И ТЕХНОЛОГИЯХ В ОБОГАЩЕНИИ ПОЛЕЗНЫХ ИСКОПАЕМЫХ В ЯКУТИИ
- 26 марта 2025 Арктическое пророчество
- 26 февраля 2025 ПОЯВЛЕНИЕ ЖУРНАЛА “РЕДКИЕ ЗЕМЛИ” ОПЕРЕДИЛО ВРЕМЯ НА 10 ЛЕТ - АКАДЕМИК РАН ВЛАДИСЛАВ ПАНЧЕНКО
- 14 февраля 2025 Редким землям России нужен ТРАМПлин
- 6 февраля 2025 РЕДКИЕ ЗЕМЛИ ЗА СТОЛОМ ПЕРЕГОВОРОВ
- 3 февраля 2025 РАЗДЕЛЯЙ И ЗАРЯЖАЙ
- 26 января 2025 ВЛАДИМИР ВЕРХОВЦЕВ ОТМЕЧАЕТ 70-ЛЕТИЕ
- 27 декабря 2024 МЕЖДУ МИРОМ И ВОЙНОЙ: ЯДЕРНОЕ ОРУЖИЕ ДЛЯ РАЗРУШЕНИЯ И СОЗИДАНИЯ
- 27 октября 2024 ДЛЯ ГЛАВНОЙ НАУКИ БУДУЩЕГО ЧЕЛОВЕЧЕСТВО ДАЖЕ НЕ ПРИДУМАЛО НАЗВАНИЕ
- 13 октября 2024 Форум «Микроэлектроника 2024» – без высокочистых редких металлов никуда
- 23 сентября 2024 ОТ ВОЗРОЖДЕНИЯ МАГНИТНОГО ПРОИЗВОДСТВА К СОЗДАНИЮ НОВОЙ ИНДУСТРИИ В РФ
- 14 сентября 2024 "Задачи будут решены" – О беспилотниках из первых рук
- 31 августа 2024 ВИКТОР САДОВНИЧИЙ: «ЕСЛИ БЫ НЕ МОСКОВСКИЙ УНИВЕРСИТЕТ, РОССИЯ БЫЛА БЫ ДРУГОЙ»