Томские ученые предлагают извлекать палладий, родий и рутений из отработавшего ядерного топлива

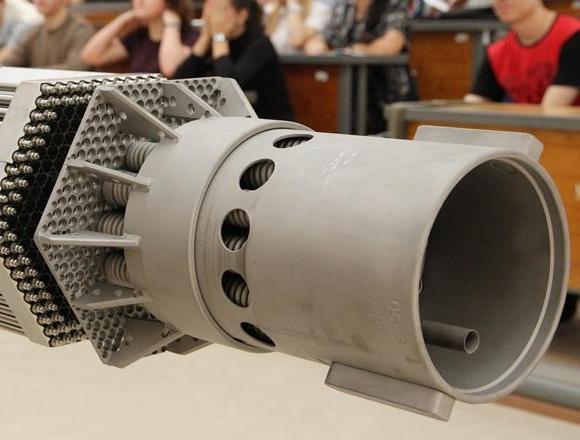
Основная цель переработки ОЯТ - повторное использование его в качестве энергетического реакторного топлива. Как поясняется в сообщении, стандартный процесс предполагает экстракционное извлечение урана и плутония и производство на их основе MOX-топлива для АЭС. Оставшиеся без урана и плутония отходы переработки ОЯТ (ОП ОЯТ) представляют собой водно-солевые растворы высокой активности, включающие целый ряд радиоактивных продуктов деления изотопа уран-235 (платиноиды, РЗЭ) и других металлов. Сейчас эти отходы выпаривают, добавляют химические реагенты (силикаты, фосфаты, бораты и другие) и направляют на операцию остекловывания с последующим захоронением в виде «брикетов». Однако у существующего способа есть ряд недостатков, главный из которого в том, что из этих «брикетов» в дальнейшем невозможно извлечь ценные и редкоземельные металлы, которые образуются в процессе деления.
«ОП ОЯТ в отличие от радиоактивных отходов несут в себе определенную ценность — то, что входит в его состав, может быть востребовано в будущем. "Брикеты", которые получаются в процессе остекловывания, конечно, занимают меньший объем и не содержат уран и плутоний, однако содержат изотопы очень ценных металлов платиновой группы — палладия, родия и рутения, которые являются продуктами деления. Но проблема в том, что из "брикетов" их потом просто не извлечь», — приводятся в сообщении слова ассистента кафедры технической физики Ивана Новоселова.
Технология переработки ОЯТ, которую разработали ученые ТПУ, предполагает использование низкотемпературной плазмы для иммобилизации отходов переработки ОЯТ. Причем технология политехников позволяет не только встроиться в уже существующий процесс переработки, но и удешевить его.
«Основой технологии переработки ОЯТ на радиохимических заводах является PUREX-процесс, в котором экстракцию урана и плутония из водно-солевых растворов осуществляют трибутилфосфатом (ТБФ) с использованием различных органических разбавителей (керосин, очищенные углеводороды и другие), которые под действием радиоактивного облучения с течением времени теряют свою эффективность и превращаются в горючие отходы переработки ОЯТ (ГОП ОЯТ). Нами разработан процесс совместной плазменной иммобилизации горючих и негорючих отходов переработки ОЯТ в воздушной плазме в расплавах хлоридов металлов (натрий, калий), стойких к радиационному облучению. В итоге получается горючая композиция, которая обрабатывается в воздушной плазме при температуре не менее 1 200 °С. На выходе мы получаем своеобразный расплав, который собирается в специальные емкости, затвердевает и отправляется на хранение. По прошествии необходимого времени из субстанции можно будет извлечь химическими способами металлы платиновой группы. Для сравнения: с одной тонны ОЯТ образуется до 2 килограммов рутения, до 1,5 килограмма палладия и до 0,5 килограмма родия», — поясняет доцент кафедры технической физики Александр Каренгин.
Ученые предлагают использовать плазмохимический комплекс, созданный в вузе. Как они полагают, установка позволит извлекать не только металлы платиновой группы, но и получать из ОЯТ нанопорошки редких металлов: после экстракции урана и плутония в образующемся растворе остаются редкие элементы, например, иттрий или цирконий. После переработки в плазме можно получать нанопорошки оксидов данных элементов. Ученые уже провели лабораторные пробы на плазмохимическом комплексе с использованием не на реального ОЯТ, а моделей, которые полностью имитируют физико-химические свойства сырья. Также ученые ТПУ уже разработали мобильный плазменный комплекс, который при необходимости можно модернизировать под нужды предприятия, и стационарную установку.
- 23 апреля 2025 ОТ «ОБОРОНКИ» ДО СПОРТА: КАК СКАНДИЙ МОЖЕТ ПЕРЕВЕРНУТЬ РОССИЙСКУЮ ПРОМЫШЛЕННОСТЬ
- 18 апреля 2025 ОТ ХАЙПА К ДЕЛУ: КАК РАЗВИВАТЬ РЗМ-ИНДУСТРИЮ В РОССИИ
- 9 апреля 2025 ВЫИГРАТЬ ВСУХУЮ: О НОВЫХ ПОДХОДАХ И ТЕХНОЛОГИЯХ В ОБОГАЩЕНИИ ПОЛЕЗНЫХ ИСКОПАЕМЫХ В ЯКУТИИ
- 26 марта 2025 Арктическое пророчество
- 26 февраля 2025 ПОЯВЛЕНИЕ ЖУРНАЛА “РЕДКИЕ ЗЕМЛИ” ОПЕРЕДИЛО ВРЕМЯ НА 10 ЛЕТ - АКАДЕМИК РАН ВЛАДИСЛАВ ПАНЧЕНКО
- 14 февраля 2025 Редким землям России нужен ТРАМПлин
- 6 февраля 2025 РЕДКИЕ ЗЕМЛИ ЗА СТОЛОМ ПЕРЕГОВОРОВ
- 3 февраля 2025 РАЗДЕЛЯЙ И ЗАРЯЖАЙ
- 26 января 2025 ВЛАДИМИР ВЕРХОВЦЕВ ОТМЕЧАЕТ 70-ЛЕТИЕ
- 27 декабря 2024 МЕЖДУ МИРОМ И ВОЙНОЙ: ЯДЕРНОЕ ОРУЖИЕ ДЛЯ РАЗРУШЕНИЯ И СОЗИДАНИЯ
- 27 октября 2024 ДЛЯ ГЛАВНОЙ НАУКИ БУДУЩЕГО ЧЕЛОВЕЧЕСТВО ДАЖЕ НЕ ПРИДУМАЛО НАЗВАНИЕ
- 13 октября 2024 Форум «Микроэлектроника 2024» – без высокочистых редких металлов никуда
- 23 сентября 2024 ОТ ВОЗРОЖДЕНИЯ МАГНИТНОГО ПРОИЗВОДСТВА К СОЗДАНИЮ НОВОЙ ИНДУСТРИИ В РФ
- 14 сентября 2024 "Задачи будут решены" – О беспилотниках из первых рук
- 31 августа 2024 ВИКТОР САДОВНИЧИЙ: «ЕСЛИ БЫ НЕ МОСКОВСКИЙ УНИВЕРСИТЕТ, РОССИЯ БЫЛА БЫ ДРУГОЙ»