Профессор Ti — от первого слитка до «титановой» медицины

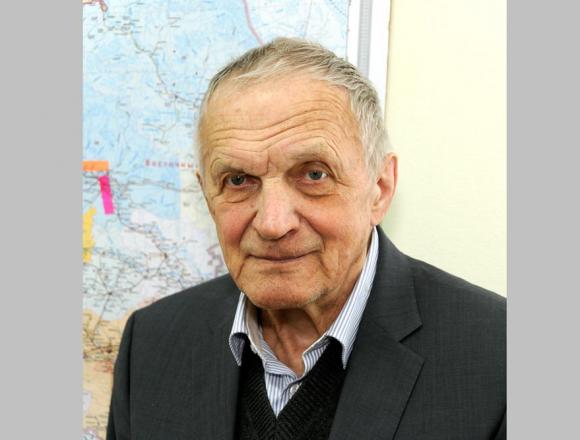
Фото: Редкие земли
Возглавив флагман отрасли — Верхнесалдинское металлургическое производственное объединение (ВСМПО) в самое тяжелое для предприятия время после распада страны в 1992 году, Владислав Тетюхин не только сохранил производство, но и вывел родной завод, на котором начинал еще молодым специалистом, в мировые лидеры титанового производства. А когда предприятие прочно встало на ноги, Тетюхин, уже будучи в солидном возрасте, загорелся новой идеей, вложил в нее все свои средства и силы и создал на Урале уникальный инновационный медицинский центр.
Как все начиналось
Это сейчас Верхняя Салда — «колыбель российского титана» и «титановая столица мира», где Boeing размещает свои предприятия, а в 1956 году, когда сюда по распределению приехал молодой инженер-металлург Владислав Тетюхин, выпускник Московского института стали им. И.В. Сталина (позднее — Московский институт стали и сплавов — Прим. ред.), это был отдаленный провинциальный городок, не отмеченный на картах. В городе не было асфальтированных дорог, и лишь местами сколоченные деревянные тротуары помогали жителям преодолевать непролазную грязь.
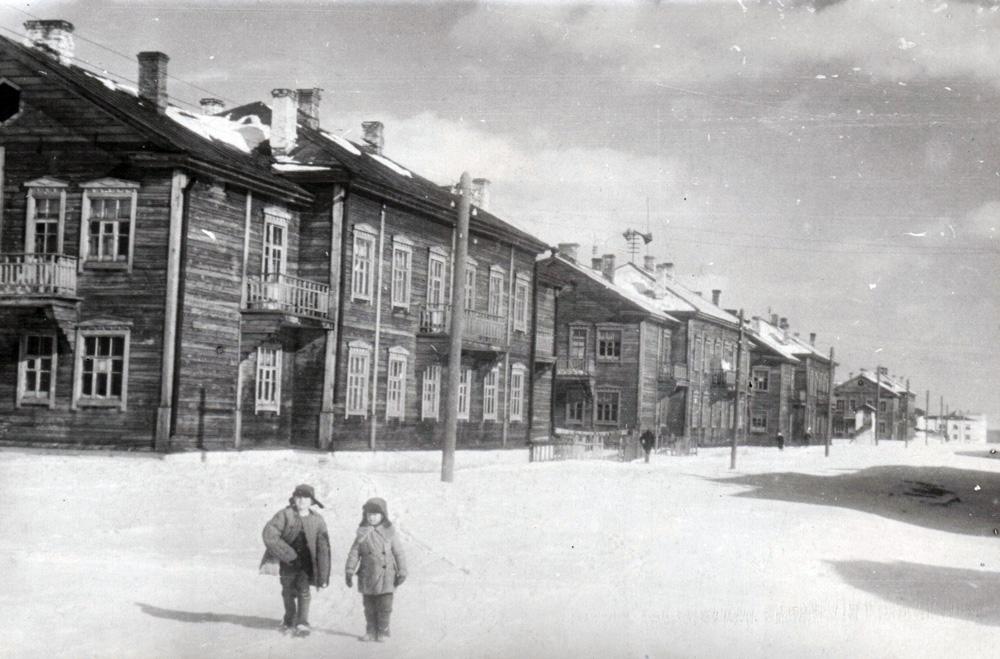
Поселок Верхняя Салда. 1950-е годы
Но самое главное, здесь не было ни одного человека, кто разбирался бы в технологии производства титановых сплавов. Только два молодых специалиста, приехавших из Москвы, — Владислав Тетюхин и его товарищ Александр Андреев, раньше занимались этим вопросом.
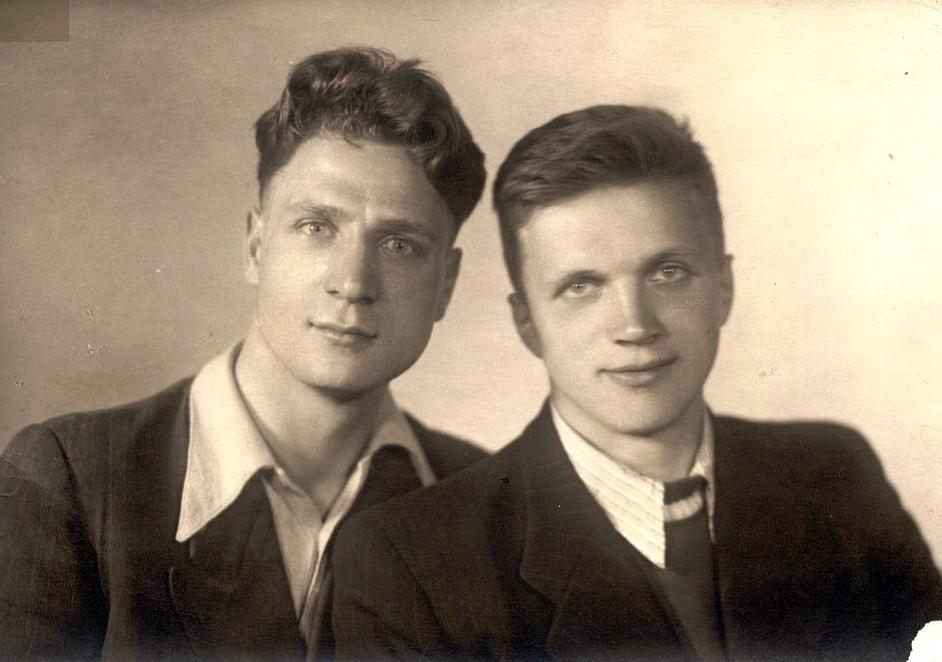
Молодые специалисты А. Андреев и В.Тетюхин
Вспоминает Владислав Тетюхин: «В 1948 году в Московском институте стали был создан новый физико-химический факультет. В две группы этого факультета набирали ребят, которые должны были заниматься редкими металлами — титаном, цирконием, гафнием, танталом, ниобием, молибденом, вольфрамом. Я туда попал в 1950 году, закончив школу с золотой медалью. Поэтому меня взяли без экзаменов. В 1956 году закончил».
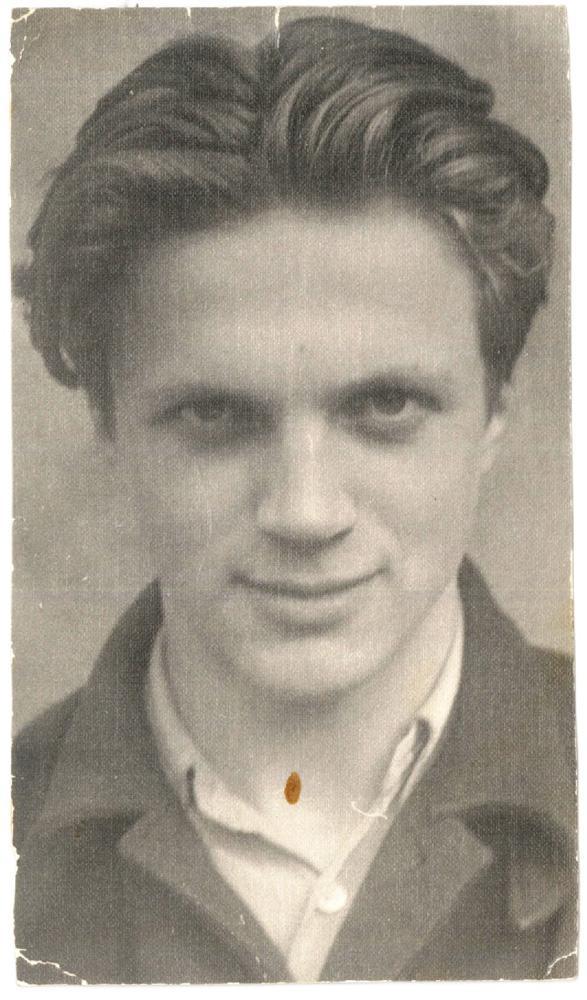
В.В.Тетюхин. 1956
Именно тогда, в середине 1950-х принималось решение по развертыванию на Урале производства титана для авиастроения. Выбор пал на Верхнюю Салду, куда осенью 1941 года был эвакуирован из подмосковной Сетуни завод № 95 по производству полуфабрикатов из алюминиевых и магниевых сплавов. Здесь же разместился завод № 519 наркомата цветной металлургии. В 1957 году произошло объединение двух заводов. Директором объединенного завода стал Г.Д. Агарков.
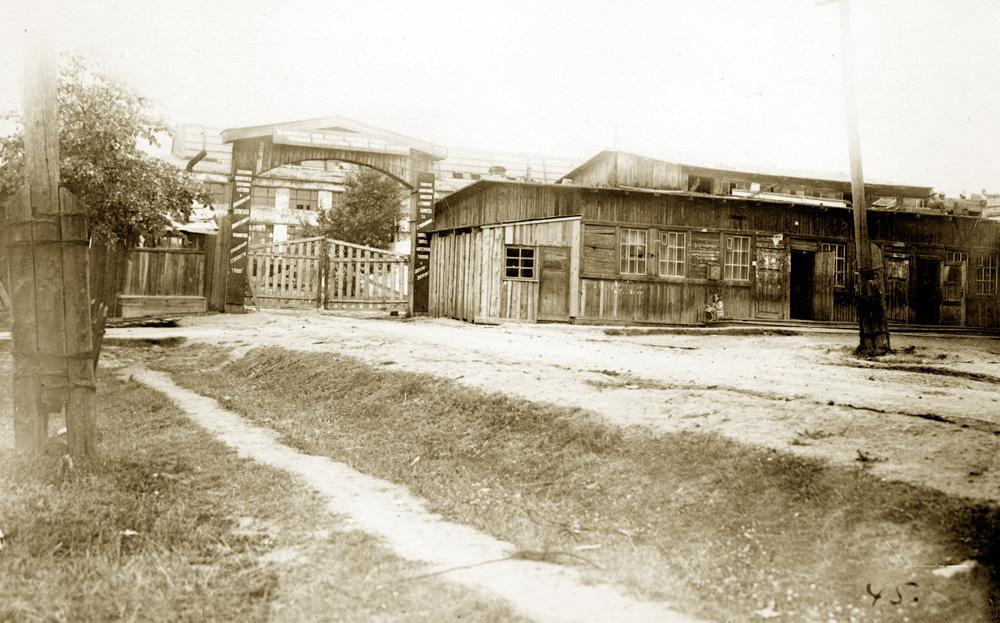
Старая проходная завода
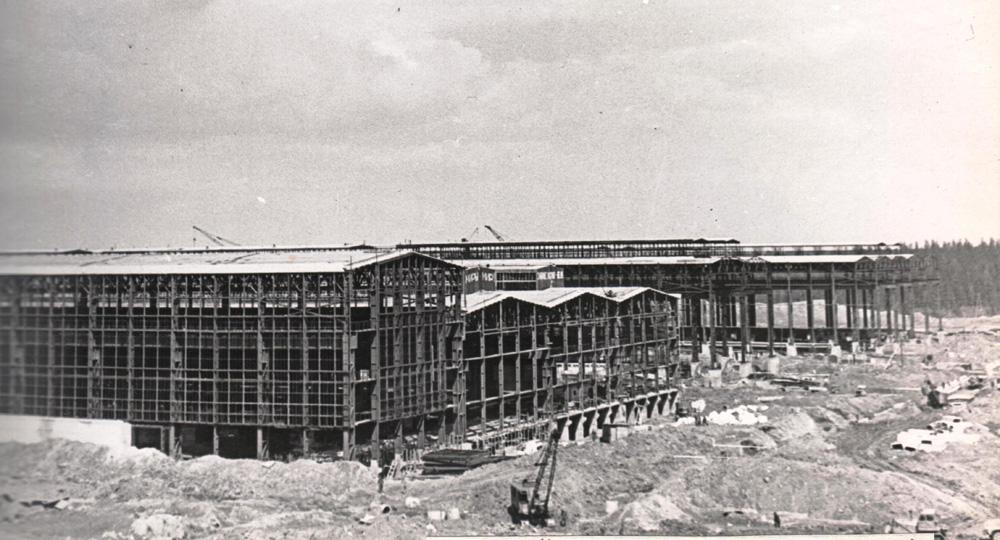
Строительство нового плавильного цеха. 1960-е годы
«На Верхнесалдинском заводе делали полуфабрикаты для самолетов из алюминиевых сплавов. Это были трубы, листы, плиты. Агарков пробивал в 1955-56-м внедрение титана. На тот момент еще не было титанового производства, была только опытно-промышленная база в Подмосковье, в Подольске. Мы там практику проходили. И были лаборатории в институтах — в ВИАМе в Москве и в Питере. Титаном интересовались судостроители, авиаторы, те, кто занимался космосом, ракетостроением. И в Верхней Салде хотели организовать производственную базу. Нам, выпускникам, объявили, что есть два места, и мы поехали — я и Саша Андреев. Это был май 1956 года. Мы приехали. Здесь никто про титан не слышал. О том, что здесь намечается, знали, может быть, три-четыре человека на заводе».
Поэтому вначале пришлось заниматься алюминием. Назначенный сразу на должность помощника мастера Владислав Тетюхин, отказался от этого места, решив начать с низов, с рабочих профессий. Был газовщиком, затем литейщиком. А уже в 1957 году при его непосредственном участии был отлит первый титановый слиток.
«Я попал в 31-й цех, где плавили слитки алюминиевых сплавов и затем отдавали их уже на обработку — на прокатку, ковку, штамповку и так далее. Прошел там все по порядку, чтобы понять, что это такое. А потом нас вызвал главный металлург В.И. Добаткин и сказал: «Все, ребята, закончена практика не по профилю». А я проходил преддипломную практику в ВИАМе, работал на печах, где плавят титан. Правил цирконий, сплавы титана с алюминиевыми наплавками.
Мы приехали в ВИАМ, договорились, чтобы нам отдали одну печку, погрузили ее и отправили в Салду, и начали работать. Это была маленькая лабораторная печь. На ней и сделали в феврале 1957 года первый четырехкилограммовый слиток. Это событие можно считать точкой отсчета освоения титана в России.
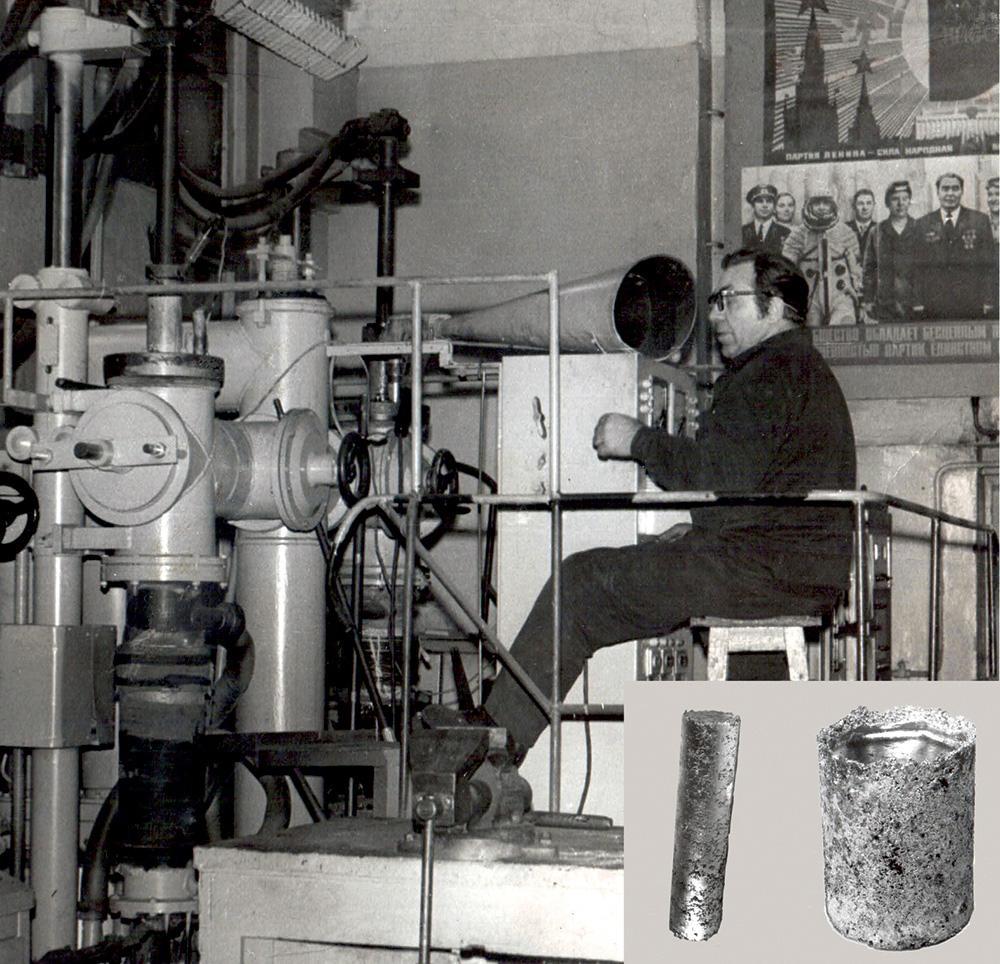
Первая печь ВИАМ и полученные на ней слитки
Потом вторую печку сами уже спроектировали. Ну и пошло. Было нас изначально: два инженера и четыре техника, которые окончили металлургический техникум в Салде. Но надо отдать должное, что руководство завода сделало все, чтобы мы ни в чем не нуждались. Полупромышленные печи, предназначенные для плавки молибдена, приспособили под титан. На них можно было получать слитки диаметром 150–250 и до 300 мм. В цехе, который работал по алюминию, была отведена специальная территория, поставлена ограда, часовой с ружьем».
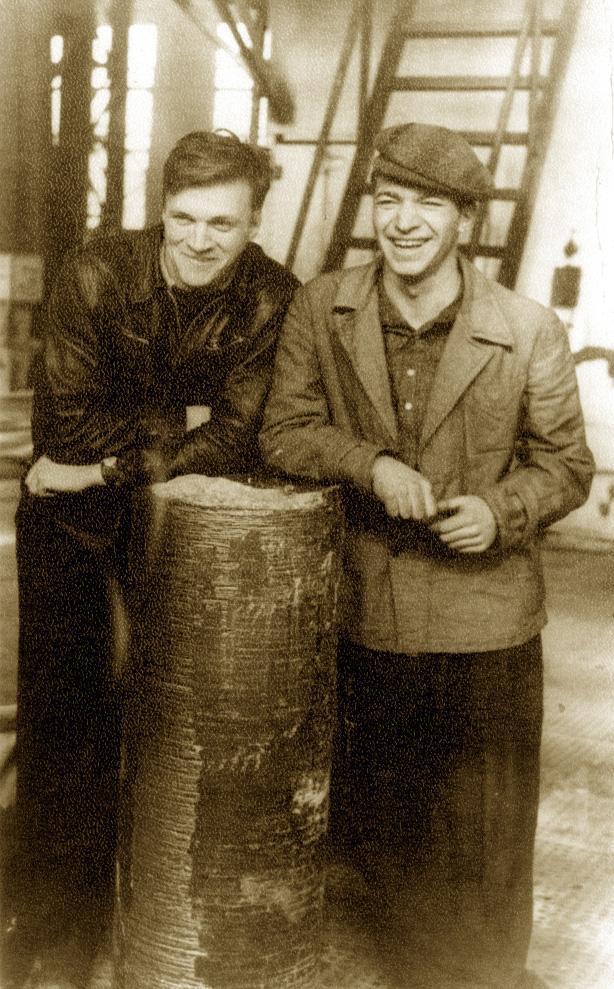
В.В. Тетюхин и Ю.А. Кунцев у первого промышленного слитка. 1957 г.
Романтические ожидания
Титановое производство развивалось очень быстро, отодвигая и замещая алюминиевое. Вводились в строй новые титановые печи, способные производить большие слитки.
«Это было востребовано, потому что было много надежд на титан. Очень много надежд. Ну, какие-то надежды реализовались, какие-то не реализовались. Это был период романтических ожиданий. Титан пробовали все — авиация, самолетостроение, моторостроение, производители ракетной техники, производители космической техники. В общем, все пробовали. Ну и судпром, конечно. Он был наиболее мощным потребителем. Причем, это были не малогабаритные изделия».
В 1959 году было принято решение о создании скоростной подводной лодкой с корпусом из титана. В отличие от маломагнитных сталей, из которых строились и строятся сейчас корпуса всех подводных лодок мира, титановые сплавы обладают более высокой прочностью, немагнитностью и стойкостью к коррозии. Правда, на тот момент не только в СССР, но и в мире не существовало технологий изготовления деталей из титана больших размеров и сварки их с необходимыми прочностными характеристиками. Поэтому для строительства первой титановой подводной лодки длиной около 120 метров пришлось радикально преобразовывать производство.
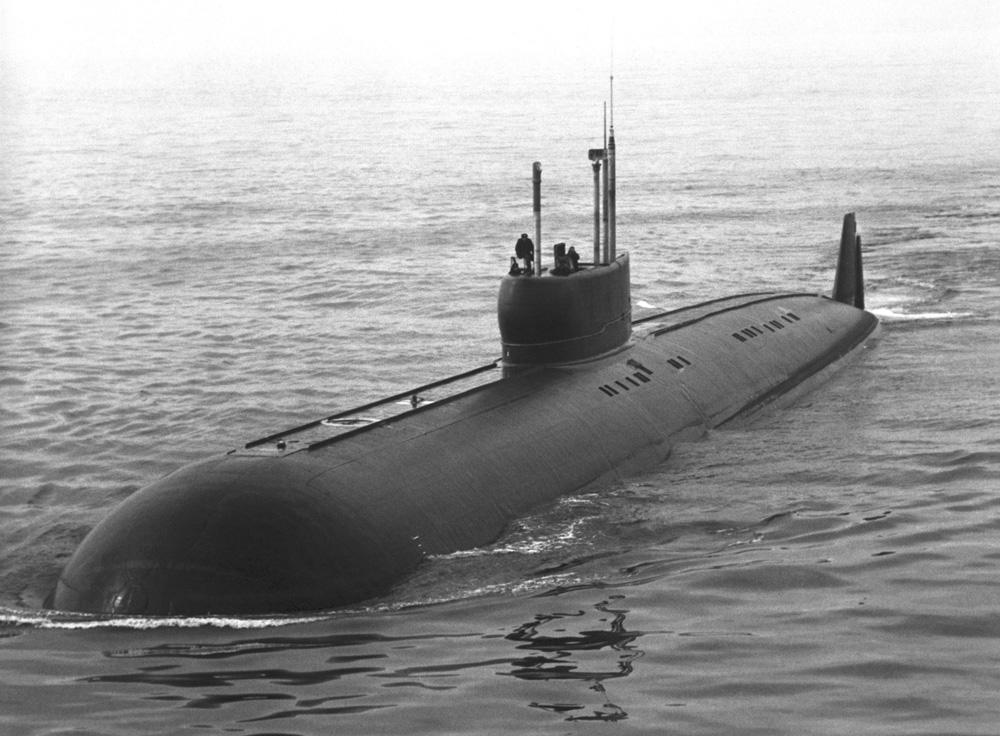
«Тогда пошли большие слитки —3–5 тонн, катали плиты. Все было под эту лодку заточено. Были романтические ожидания… Сейчас уже нет романтизма, сейчас — прагматизм. Титан прочно занял свое место в моторостроении. До 450-480 градусов титан работает эффективно. Если говорить о самолетных конструкциях, то даже если будет замена на углепластик, то все равно все крепежные детали, все силовые конструкции, будут делаться из титана. Потому что по другим материалам идет коррозионный процесс».
На Верхнесалдинском предприятии Владислав Тетюхин прошел все ступени заводской карьеры: помощник мастера, начальник техбюро, замначальника цеха, заместитель главного металлурга по титановому производству. В 1965 году он становится кандидатом наук, а спустя 10 лет, в 1975 году — доктором технических наук. В 1976 году Владислава Тетюхина переводят в Москву во Всесоюзный НИИ авиационных материалов (ВИАМ).
« В ВИАМе я был заведующим сектором надежности ресурсов, а потом — титановой лаборатории. А в 1992 году, когда в стране все было не очень хорошо, приехали ребята из Верхней Салды и сказали: «Поехали обратно!» Ну, поехали обратно. Были выборы. И меня выбрали генеральным директором».
Тяжелые времена
Владислав Валентинович рассказывает об этом поворотном моменте в своей жизни как о чем-то обыденном, как о решении, которое было принято легко и как бы само собой. На самом деле, нужно было обладать огромным мужеством и гражданской ответственностью, чтобы в 60 лет бросить налаженную московскую жизнь и вернуться на родной завод, который был в тот момент на грани банкротства, а город — на краю социальной катастрофы. После развала Советского Союза титановый гигант остался без госзаказов, и объемы производства упали в десятки раз.
«Тогда в 30 раз упали заказы на титан, и где-то в шесть раз на алюминий. То есть это была катастрофа, настоящий коллапс. Еще что-то делали, но потребители не платили за металл. Тихо начался распад. Завод в целом уже работал на аренде. Это был первый эксперимент министерства авиационной промышленности, когда завод выпустили на аренду. Отдельные большие цеха стали самостоятельными предприятиями. Образовался прокатный завод, образовался кузнечный завод — 21-й цех, образовался литейный завод. В общем, это было что-то. Стало ясно, что если это продолжится, будет полный распад. Но заявить об этом вслух на фоне всех этих речей о демократии, о свободе и так далее, было сложно. Поэтому пришлось за счет определенных юридических мер обратно все это соединить. Убрать все эти заводы, собрать опять все в единый кулак и подумать, как этот кулак мог бы работать в условиях совершенно дикого экономического падения».
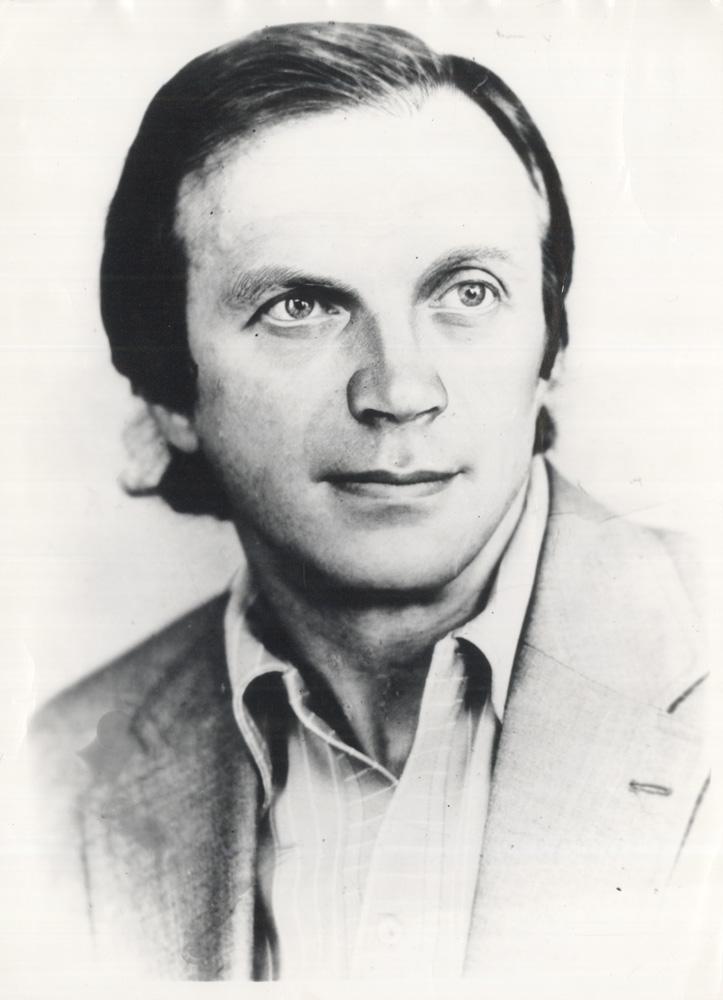
В.В. Тетюхин
Для начала помогли старые производственные связи и кооперация с ВИАМом, ВИЛСом, Академией наук, ЦНИИ-48 в Санкт-Петербурге (ныне ЦНИИ КМ «Прометей»).
«Тогда директором ВИАМа был Р.Е. Шалин, очень разумный человек. У них не было денег и у нас не было денег. И мы с ним договорились, что не будем платить друг другу, а будем делать: мы — свою часть работы, они — свою, а вместе — делать одно дело. И это было воспринято. Поэтому, может быть, не в таком масштабе, как было, тем не менее, работа продолжалась. Мы делали свою часть — плавили, ковали и так далее, они занимались исследованиями, тоже за свой счет. Потом, объединив усилия, смотрели, что получилось, собирались периодически в Москве или здесь. Точно такая же работа была и с Питером».
Выход на западный рынок
Все это было хорошо, но Тетюхин понимал, что базовую подпитку заводу могут обеспечить только регулярные заказы, рассчитывать на которые внутри страны не приходилось. Стало ясно, что надо пробиваться на Запад, искать заказчиков среди западных авиастроителей. И Тетюхин поехал в Америку, объехал все авиационные компании, был даже в НАСА. Его рассказ об этом времени напоминает выдержки из приключенческого романа.
«Нужно было открыть «окна» для поставок в Штаты, Европу, Азию. Конечно, лидерами были американцы, поэтому встал вопрос, как прорываться в Штаты? Каким образом, если их компании — Timet (Titanium Metals Corporation) и Ormet — были лидерами на тот момент, имели большой опыт в публикациях, в технологиях, в науке, в производстве? Вопрос был деликатный. Главное было — не ввязаться в драку, как-то «нежно» зайти. Нужно было за кого-то «зацепиться», за какого-то реального производителя, который бы попробовал взять наш материал.
Первым нашим реальным партнером в США была компания из Лос-Анджелеса Shulz Steel Company. Во главе компании стоял Гордон Шульц, продолжатель рода основателей компании — хороший инженер, толковый, энергичный и ковбой по натуре. Так получилось, что мы поставили туда слитки, и наши слитки очень понравились Шульцу. И хоть они по составу ничем не отличались от слитков Таймета (это был тот же сплав Ti-6Al-4V, все по их стандартам делали), но наши были обточенные, красивые, блестящие. А раз обточены, то — меньше вероятность дефектов при ковке, резке и т.д. К тому же мы использовали средства выявления микротрещин на поверхности, чтобы снизить до предела степень риска разрушения материала при деформации. В общем, наши слитки понравились.
Они приезжали к нам в Верхнюю Салду раза три, смотрели, как слитки куются, как деформируются, что из них получается. Мы были у них в Лос-Анджелесе. Короче, наладили очень хороший персональный контакт. Это была удача, нам просто повезло. Шульц работал с «Боингом», делал для них штамповки. У него был великолепный пресс. И это было то окошечко, через которое мы попали на «Боинг». Здесь нам повезло еще раз — «Боинг» открыл свое представительство в Москве, которое возглавил Сергей Владимирович Кравченко — тогда молодой инженер, ученый, энтузиаст. И он тоже нас поддержал, когда наш материал попал на «Боинг». Конечно, это была удача. Но главным было то, что мы делали кондиционный материал».
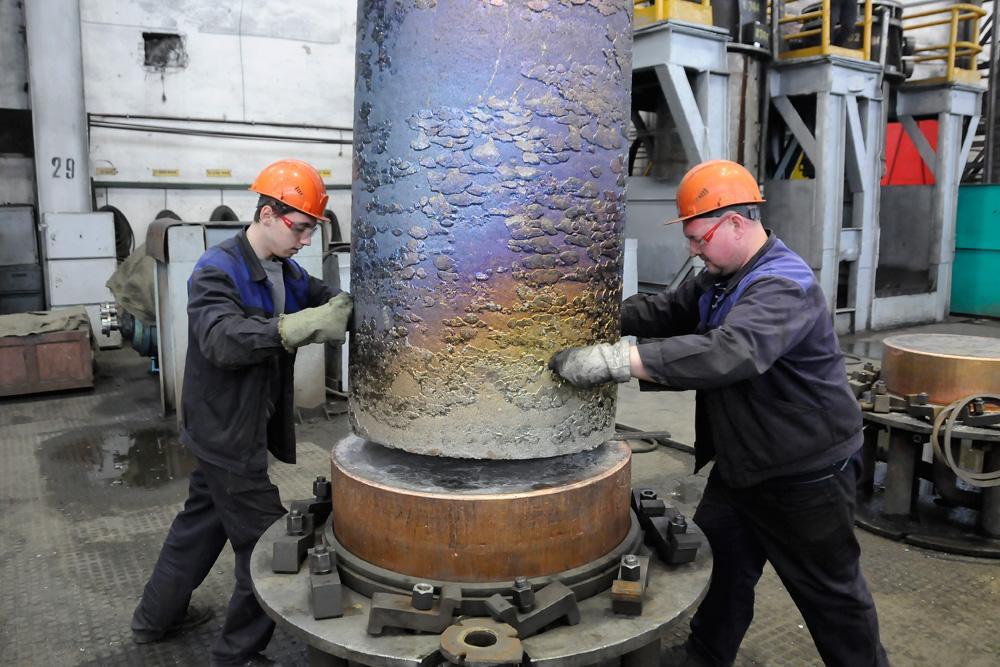
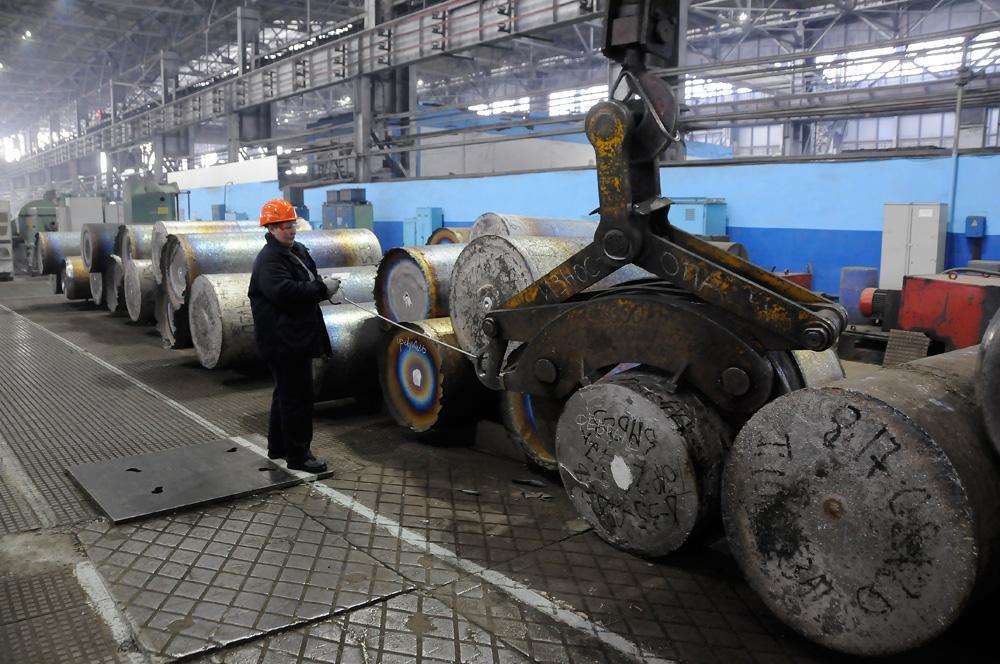
Производство титановых слитков на предприятии в Верхней Салде. 2018 г.
Партнерство с Boeing
Начало партнерству ВСМПО и Boeing было положено в 1993 году, когда российское предприятие вошла в число поставщиков титана для американской компании. С тех пор сотрудничество с крупнейшим в мире авиапроизводителем только расширялось.
«Уже в 1994 году мы работали с «Боингом», «смотря в лицо друг другу». В 1996-м они уже были абсолютно уверены в том, что материал качественный, хороший и заключили с нами соглашение по созданию стратегического склада для «Боинга». Мы туда поставили две тысячи тонн слитков. Причем это были слитки специально зашихтованные, сделанные под крепежные детали и под конструкционные детали. А в 1998 году был подписан первый контракт с «Боингом». Это был первый в истории «Боинга» и в истории Соединенных Штатов в принципе контракт с российским заводом. Причем история была такая.
«Боинг» распределял объемы между американскими компаниями Timet, RMI и нами. Дали 70% Таймету, 16% RMI и 14% нам. Я им говорю: «Ребята, как-то неудобно, неуважение какое-то к россиянам. Поставьте нас хотя бы между двумя американскими компаниями!» Они посмеялись и дали нам 16%, а RMI — 14%. То есть мы заняли второе место среди поставщиков «Боинга». Это был 1998 год. Помните, была такая комиссия «Гор-Черномырдин»? Вот в ходе одной из ее сессий в Вашингтоне и был подписан первый контракт. И дальше пошло. Сначала мы поставляли в основном слитки, но уже начались поставки титановых полуфабрикатов. А потом наступил 2011 год».
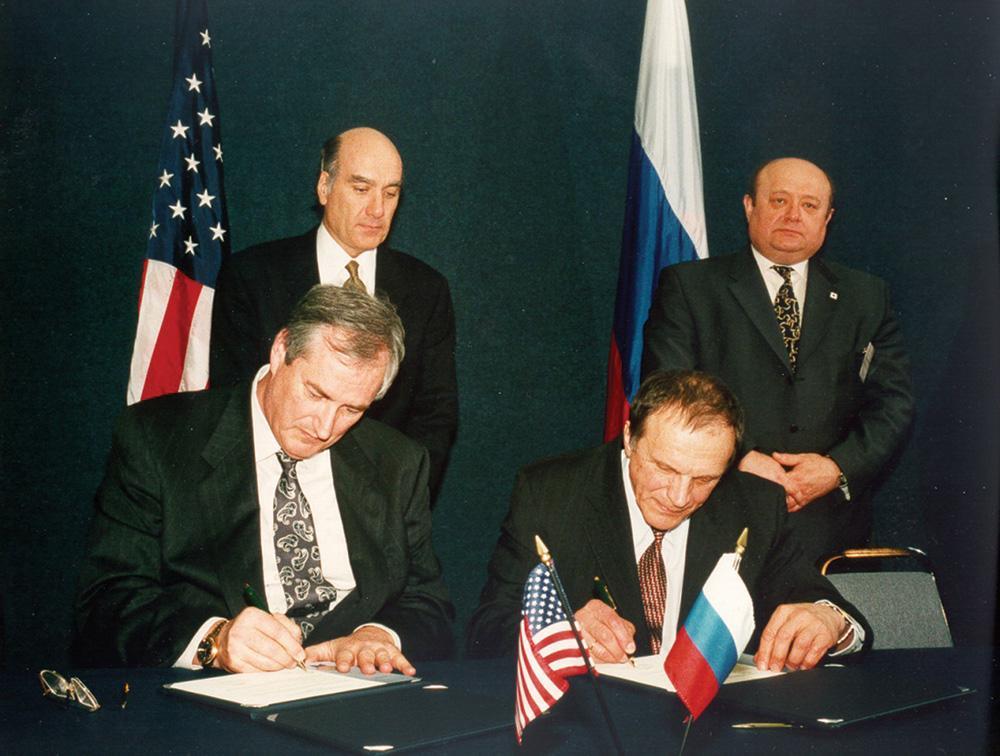
Подписание первого контракта с Boeing. 1998 г.
После терактов 11 сентября 2001 года в мире резко сократилось количество авиаполетов. Объем заказов на комплектующие для самолетов резко упал. Соответственно, авиапроизводители перестали заказывать титан. Поставщики в этой ситуации повели себя по-разному.
«Главные американские поставщики титана Timet и RMI ввели у себя систему pay-or-take — бери или плати. «Боинг» спрашивает нас: «А вы какой штраф с нас будете брать?» Я им говорю: «Вы наши партнеры, и находитесь в беде. У нас в такой ситуации не принято брать штрафы». Он удивился. Потом, когда у нас была проблема — в Салде в деревнях была вспышка гепатита С, и не хватало лекарств, они перевели срочно 150 тысяч долларов в Европу, там закупили препараты и привезли в Салду. Это говорит об уровне отношений. Отношения продолжали развиваться, «Боинг» поднял нашу долю с 16 до 20 процентов, потом — до 30. Мы договорились о создании совместного предприятия».
В 2006 году между ВСМПО-АВИСМА и Boeing было подписано соглашение о создании совместного предприятия по механической обработке титановых штамповок Ural Boeing Manufacturing в городе Верхняя Салда. Общие инвестиции в проект составили порядка 70 млн долларов, производство было запущено в 2009 году. Совместное предприятие постепенно наращивает объемы производства, а также повышает качество и глубину механической обработки изделий. В 2018 году на территории Свободной экономической зоны «Титановая долина» в Верхней Салде начнет работать вторая очередь Ural Boeing Manufacturing. Объем инвестиций — 5,5 млрд рублей. Также совместными усилиями ВСМПО-АВИСМА и Boeing был создан инновационный научно-исследовательский центр титановых технологий.
««Боинг» для нас — образец плодотворного совместного сотрудничества. Нас связывают достаточно глубокие, откровенные отношения, которые распространяются не только на производство, но и на личные взаимоотношения. На всех уровнях — от исследователя и конструктора до президента «Боинга» — никаких проблем, обо всем можно договориться».
Сотрудничество ВСМПО-АВИСМА и Boeing — пример весьма плодотворного технологического партнерства, в котором российская корпорация выступает не только как ответственный поставщик, строго придерживающийся стандартов, но и предлагает компании Boeing собственные технологические решения. К примеру, сейчас практически в каждом самолете Boeing используется сверхпрочный титановый сплав VST 5553 (Ti-5Al-5V-5Mo-3Cr), разработанный специалистами ВСМПО.
«Изначально мы производили все сплавы для «Боинга» по их стандартам. Самым популярным, естественно, был Ti-6Al-4V. А еще был сплав с железом Ti-10V-2Fe-3Al , технологически очень сложный, так как железо очень сильно ликвирует и образуются микроучастки, обогащенные железом. Соответственно, возможно возникновение неоднородностей и связанных с этим проблем. Вместо этого сплава мы предложили им сплав 5553, с которым мы работали с 1998 года. Сначала они отнеслись к этому сплаву скептически, потом заинтересовались, да так, что отказались от своей разработки и взяли нашу. Представляете себе, россияне вошли в американское авиастроение не только со своим металлом, но и со своим сплавом! Это не только производственный, но и технологический прорыв, даже научный, я бы сказал».
Секреты успешных отношений
Такие успешные отношения с зарубежными партнерами выстраивались, во многом, благодаря дипломатическому таланту «Профессора Ti» и принципам, которым он следовал в бизнесе.
«Был принцип, который был положен в основу отношений со всеми зарубежными партнерами. Мы могли начинать работать, потом расходиться, даже начинать конкурировать. Но — с уважением к людям, к производству. И без негатива. Никаких там скандалов, публикаций, никаких шероховатостей не должно быть. Должны быть нормальные деловые отношения. Если вас судьба свела, и вы работаете вместе, развивайте отношения. И с уважением относитесь к конкурентам. Вот такой был принцип. Поэтому у нас сохранились отношения и с Timet и с RMI. Мы с ними хотели даже совместное предприятие делать. Мы сотрудничали с обеими компаниями, металл им поставляли, хотя это наши конкуренты. Они наш металл реализовывали в Америке. И когда Ленни Мартин, президент Timet, уходил на пенсию, мы пожелали ему благополучия, и но сказал: «Я всегда видел в вас конкурентов, но относился к вам с уважением. И до сих пор так отношусь за то, что вы сделали». Вот что значит отношения и принципы».
Не менее важным фактором был постоянный поиск, постоянное совершенствование производства, технологий, расширение и углубление ассортимента продукции.
«Помню, предложили мы «Боингу» листы сплава Ti-6Al-4V для сверхпластической деформации, поставили пробные листы. Приезжаю, думаю, хвалить будут. А они собрали инженерный круг и разнесли в пух и прах нашу разработку. Я рассмеялся. Говорю: «Хорошо, ребята, ладно, понял. Презентация не состоялась. Можно тогда у вас попросить материал, который вы используете?» Мне дали этот материал. И мы договорились: каждый месяц мы высылаем им по листу. Через полгода нас сертифицировали. Все. И пошло. Вот пример отношений. Сейчас мы поставляем «Боингу» эти листы, и они ничем не отличаются от исходных поставщиков, которые годами эти листы делали».
К большим деталям
Благодаря наличию на предприятии ВСМПО уникального оборудования, в том числе одного из самых мощных в мире гидравлических прессов усилием 75 тысяч тонн, на заводе в Верхней Салде сегодня производятся самые крупногабаритные в мире детали для самолетов, такие, например, как балка шасси для самого большого в мире пассажирского самолета А380, которая весит почти 3,5 тонны.
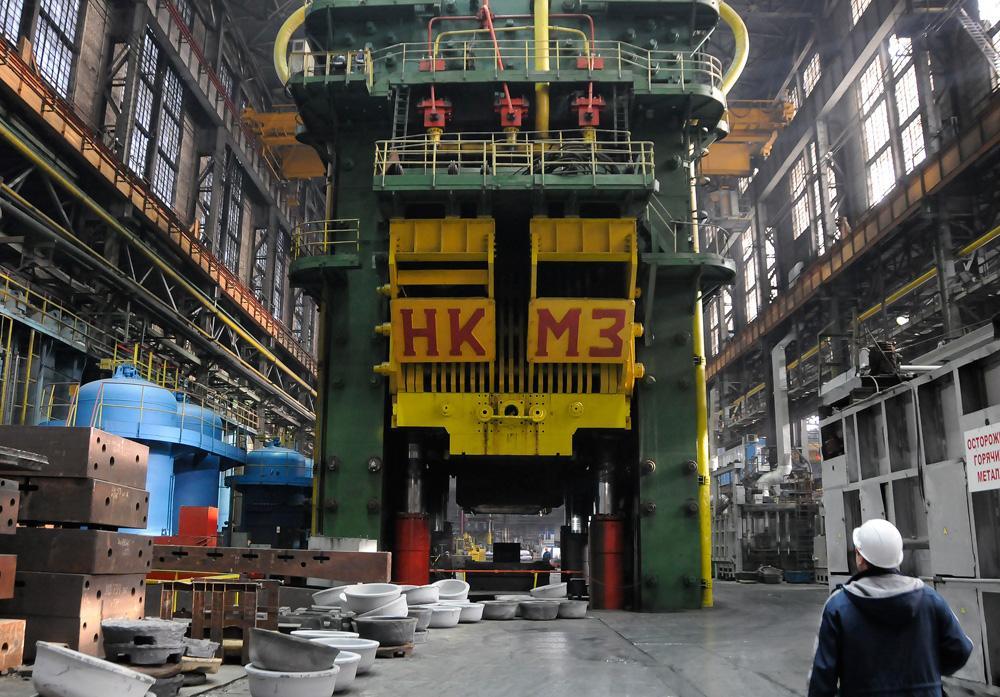
Один из самых мощных в мире гидравлических прессов усилием 75 тысяч тонн на заводе в Верхней Салде
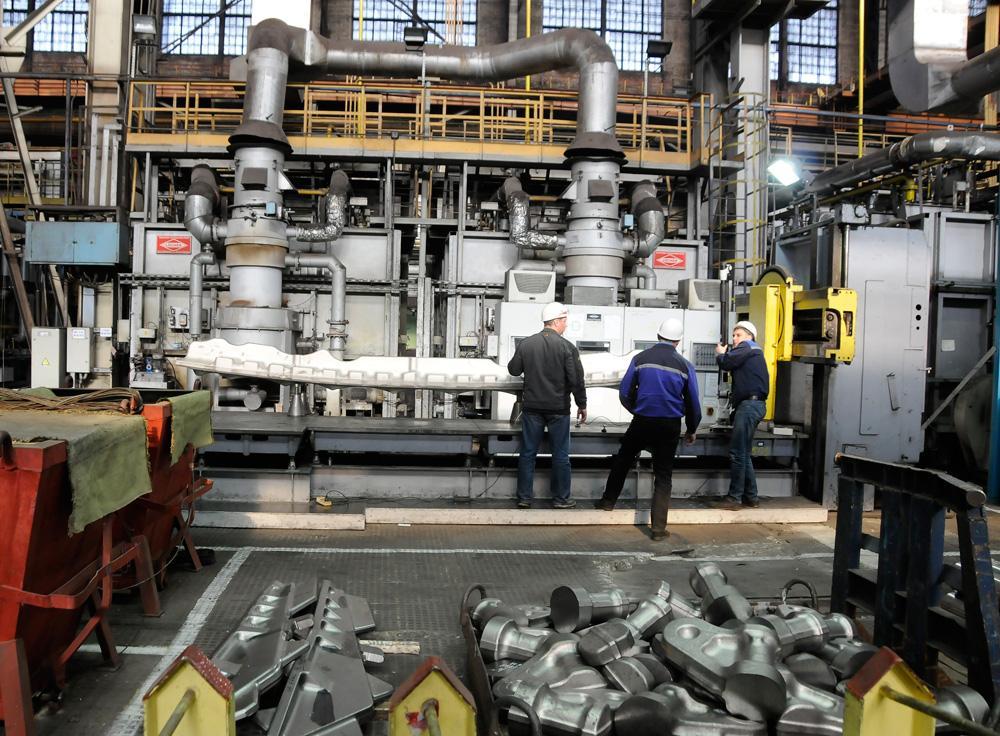
Производство крупных деталей для Boeing и Airbus на современном производстве ВСМПО-АВИСМА
Владислав Валентинович рассказывает о начале пути к большим деталям: «Это был 1994 или 1995 год. На выставке в Фарнборо, где проходил авиационный салон, была представлена знаменитая кузнечная компания Wyman-Gordon. У них на цепях висел огромный, как стенобитное орудие, тракбим (truck beam — балка тележки шасси — Прим. ред.). Они были первыми кузнецами, штамповщиками, которые делали тракбимы. Это было чудо для нас, просто чудо. Ну и тогда возникла шальная идея — тоже попробовать. И сейчас вот делаем сами все, для «Боинга» и для всех остальных».
Расширение партнерства
«Следующим партнером была канадско-американская компания Goodrich. Они обрабатывали наши штамповки, из которых затем изготавливали тракбимы. А первый международный сертификат качества мы получили в 1994 году от General Electric за поставку им прутков сплава Ti-6Al-4V для авиационного двигателя. В конце 1990-х начали работать с канадским производителем самолетов Bombardier, с европейскими Daimler-Benz, Aérospatiale и British Aerospace,которые затем объединились в Airbus. Наши поставки в те времена закрывали примерно 55% потребностей Airbus в титане. В 1995 году начали работать с Rolls-Royce, в 1996-м — с французской компанией SNECMA. И со всеми предприятиями, хоть европейскими, хоть американскими, у нас хорошие рабочие отношения. Правда, такого полного взаимопонимания, как с «Боингом», ни с кем нет».

Владислав Тетюхин с президентом США Джорджем Бушем-младшим
В 1995 году Владислав Тетюхин решил, что американского и европейского рынка недостаточно и надо пытаться выходить на азиатские рынки.
«С 1995-го мы начали ездить в Китай, Корею, Японию. Что-то развивалось, потом затихало. С японцами сначала очень активно было, потом меньше. Продолжается работа с Китаем в плане поставок для авиаконструкций. И естественно уменьшились работы по гражданскому титану — трубы для теплообменников, для водоочистки. Потому что Китай здесь сам очень мощно вошел. Очень трудно конкурировать с ними в этой области. И мы сфокусировали усилия на авиации, самолетостроении. Хотя направление гражданского применения — это очень интересно и, мне кажется, перспективно».
Во второй половине 1990-х, начале 2000-х Владислав Валентинович активно изучал возможности применения титана в неавиационных областях.
«Это водоочистка, медицина, туристическое снаряжение. Но здесь появляется много конкурентных материалов. Вот, допустим, была мода делать спортивные велосипеды из титана. Сейчас делают из пластика, и так далее. Надо искать и новые применения. Титановые сплавы — коррозионностойкие. Их можно использовать под землей, в морских условиях, делать из них контейнеры для хранения химических, радиоактивных отходов.
Титан занял сейчас прочные позиции. Не в том объеме, который предполагался тогда, когда проводились начальные исследования, но позиции достаточно прочные. И мне кажется, что было бы сейчас целесообразно вернуться к некоторым идеям, которые так возбуждали публику в 1980-е и в 1990-е годы, но сейчас подзабыты. Потенциал использования титана, мне кажется, еще не полностью раскрыт».
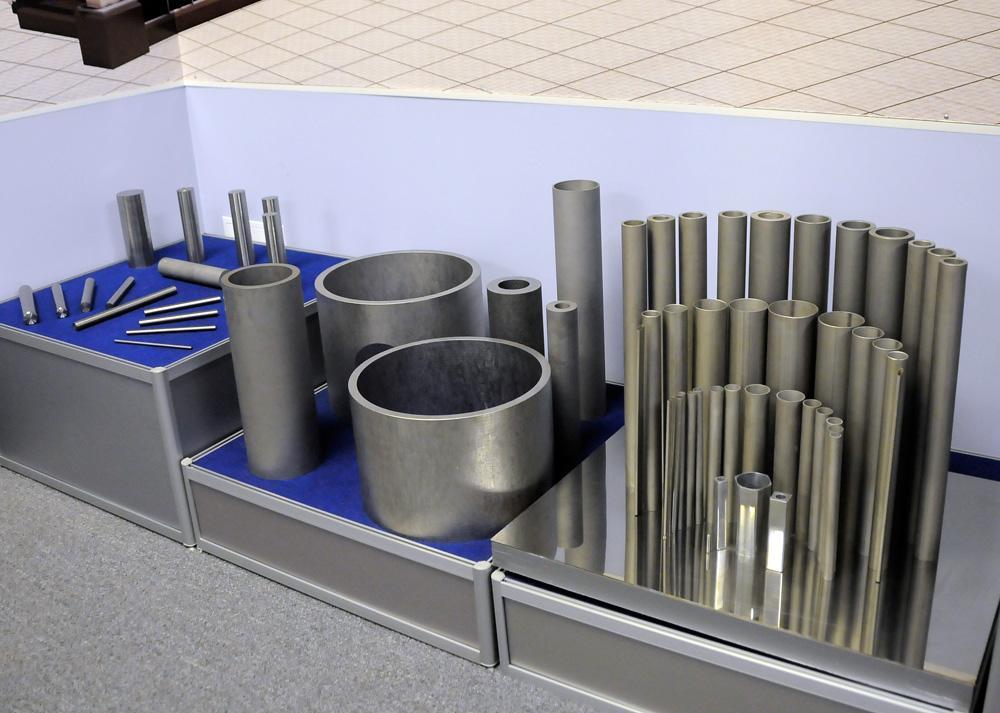
Титановые трубы, производимые ВСМПО-АВИСМА
Находясь на посту гендиректора крупнейшего в мире титанового предприятия, Тетюхин продолжал думать о стратегии его развития и наращивании конкурентных преимуществ.
«Мы делали все по стандартам. Здесь нет вопросов, стандарты, они во всем мире одинаковые, им надо было просто соответствовать. Это безусловно. Но надо было и развиваться. Очень хорошая инициатива была объединить в единый цикл производство титановой губки и конечного продукта (присоединение к ВСМПО в 1998 году Березниковского титано-магниевого комбината, положившее начало корпорации ВСМПО-АВИСМА — Прим. ред.), оправдала себя и стратегия, нацеленная на выпуск механически обработанных деталей. Получилось так, что мы стали единственным в мире титановым предприятием полного цикла — от сырья до машиностроения. И это очень ценно для потребителей — приехал, всю цепочку проконтролировал, не надо ездить по всему миру. К примеру, RMI тоже делает на своем заводе небольшие финишные детали, но чтобы огромные штамповки... это только мы можем».
Когда родилась идея создания в Верхней Салде «Титановой долины» — особой экономической зоны, где будут созданы специальные условия для развития промышленного производства, Тетюхин планировал, что сюда приедут конечные потребители титановой продукции —зарубежные производители, и здесь будет налажено производство именно финишных, окончательно обработанных изделий. Это позволило бы не только нарастить производственные мощности, но и осуществить, как сейчас принято говорить, локализацию — перенести на российскую территорию новейшие зарубежные технологии.
«Но «Титановая долина» не развивается в том направлении, в котором она была задумана. Например, как развивается наше совместное предприятие с «Боингом»? Идет передача всех производственных процессов, создается такой мощный производственный, машиностроительный комплекс. Вот как это было задумано. И когда это задумывалось, то мы беседовали со многими российскими и зарубежными компаниями такого профиля, с авиастроителями, с двигателестроителями. И в общем они смотрели очень позитивно на все это дело. Для них это было бы выгодно, здесь все отходы после обработки тут же идут обратно на завод, что положительно сказывается на себестоимости конечного продукта. Здесь можно разместить оборудование, на котором обслуживать несколько заводов, загрузка станков будет более эффективной. Но, увы, пока есть то, что есть.
Возможно, здесь наша корпорация должна быть более активной, настойчивой. Но сейчас, в связи с этими проблемами с санкциями, надо думать, как себя вести. Потому что активность в этой области может вызвать даже определенный негатив».
Новый большой проект
В 2009 году Владислав Валентинович Тетюхин ушел с поста генерального директора корпорации ВСМПО-АВИСМА, оставаясь одним из крупнейших акционеров титанового гиганта и продолжая работу в Совете директоров корпорации. Казалось бы, у Тетюхина было на тот момент все — почет и уважение коллег и партнеров, признание научных заслуг, выдающиеся управленческие успехи и впечатляющие деловые достижения на международном уровне. По итогам рейтинга журнала Forbes 2011 и 2012 годов Владислав Тетюхин попал в списки богатейших бизнесменов России, его состояние оценивалось в 650 миллионов долларов. И в тот самый момент, когда «жизнь удалась» и можно, наконец, в свои 76 уйти на заслуженный отдых, Тетюхин продает все свои акции и вкладывает деньги в строительство в Нижнем Тагиле медицинского центра эндопротезирования. В этом проекте он выступал не просто как инвестор, а как его идейный вдохновитель. Построить ортопедический центр — была его идея. И в основе идеи, как ни странно, лежал все тот же титан.
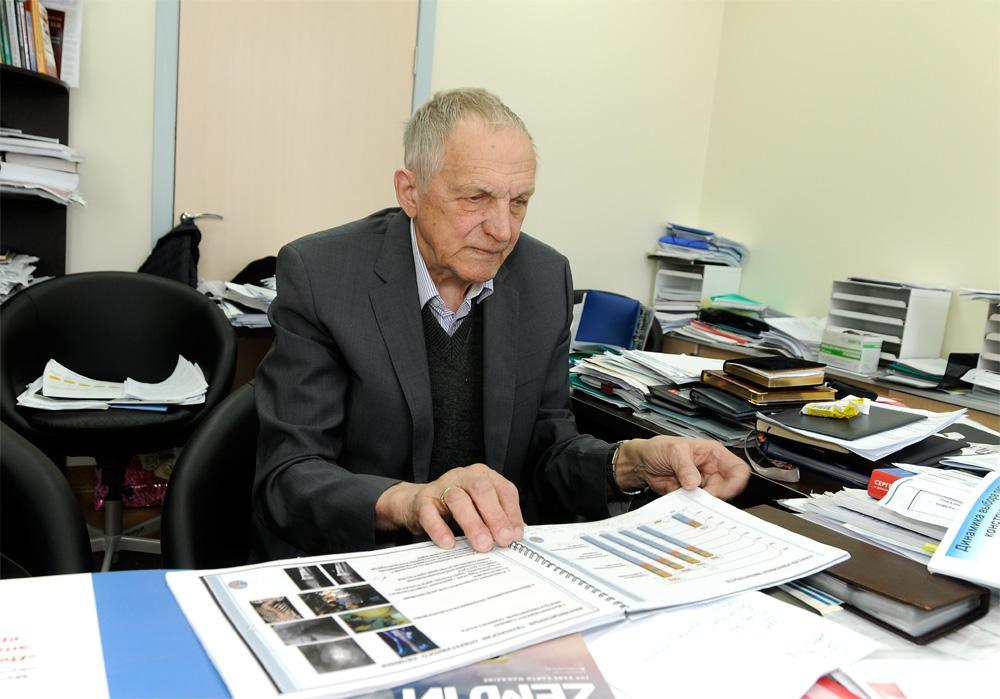
В.В. Тетюхин в своем кабинете. 2018 г.
«Мы поставляли титановые листы и прутки для медицины в США и Европу, для переработки на имплантаты. Это первое. Второе, так как я активно занимался спортом, приходилось и ломаться, и реабилитироваться, и даже поставить протез. Так что я был знаком с проблематикой. Это была лично моя идея — создать лечебно-реабилитационный центр не хуже, чем в Германии. Именно медицинский центр полного цикла — и диагностика, и лечение, и реабилитация. Он так и продумывался изначально. И в этом наше основное отличие от существующих федеральных центров — у нас несравненно на более высоком уровне стоит реабилитационный процесс. То есть, у них его вообще нет. Они зависят от реабилитации в соседних больницах и так далее. Или они это у себя только сейчас организуют. А у нас это изначально было заложено. Более того, вторая очередь проекта — это комплекс по «супер-реабилитации» — бассейн, около сотни медицинских тренажеров. Вот этим мы принципиально отличаемся».
За строительство нижнетагильского инновационного центра восстановительной медицины в 2012 году Владислав Тетюхин получил звание «Человек года» по версии журнала «Деловой квартал». Общая стоимость проекта составила 4,3 млрд рублей, из которых 3,3 млрд рублей инвестировал сам Тетюхин, а недостающий 1 млрд рублей выделил областной бюджет.
В сентябре 2014 года центр был открыт. Но для того чтобы центр заработал, пришлось преодолеть не один бюрократический барьер. Строительство центра и сам проект применения инновационных технологий получили одобрение Президента России. Владимир Путин поставил резолюцию на письме от свердловского губернатора Евгения Куйвашева, в котором автор просил оказать поддержку госпиталю восстановительных технологий. Ответственным за поддержку была назначена министр здравоохранения РФ Вероника Скворцова.
«Но Минздрав до сих пор нас игнорирует. Я не знаю, что еще нужно. Есть прямое указание Президента, но — никакой реакции. Указание было еще в 2012 году, когда мы начали строительство. Теперь мы уже работаем, вовсю оперируем, лечим. В 2015 году еще одно письмо Владимиру Путину от губернатора с просьбой выделить федеральные квоты на операции. Президент пишет: «Нужно поддержать. Доложите». Но ничего. Ноль».
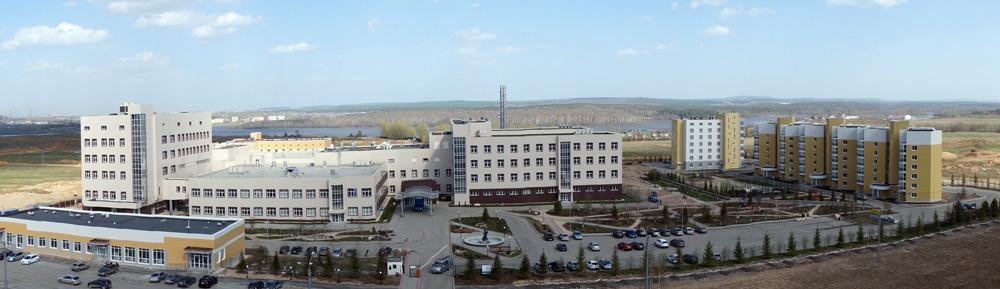
Уральский клинический лечебно-реабилитационный центр в Нижнем Тагиле. 2018 г.
С декабря 2015 года медицинский центр Владислава Тетюхина начал делать операции бесплатно при наличии полиса ОМС. Поддержка госпиталю нужна не только материальная (например, на строительство реабилитационного корпуса, которое может стоить до 1 млрд рублей), но главное, в чем нуждается госпиталь — квоты на операции. Сейчас центр имеет региональный статус, что позволяет проводить по квотам, оплачиваемым Минздравом, только операции для жителей Свердловской области. Эта загрузка существенно меньше возможностей госпиталя.
«Только по эндопротезированию мы можем делать до шести с половиной тысяч операций в год, а мы делаем в пределах двух тысяч. А врачам надо платить зарплату. Пока мы работаем в долг».
Тетюхин надеется, что Минздрав повысит статус госпиталя до федерального, что позволит оперировать пациентов из других российских регионов. По его словам, без этого одни только налоговые льготы окажутся бессмысленными и не спасут медучреждение.
Значимость человека определяется не тем, сколько денег он заработал, а тем, что он сделал, чтобы изменить жизнь людей. Губернатор Свердловской области Евгений Куйвашев назвал создание Уральского клинического лечебно-реабилитационного центра «гражданским подвигом» Владислава Тетюхина. Но не меньшим подвигом было и восстановление титанового производства в России в кризисные 1990-е годы, а еще раньше — создание с нуля этого производства. Что называется, от первого слитка. Владислав Тетюхин не раз в своей жизни брался за большие проекты, реализация которых меняла жизнь не только сотен и тысяч людей, но и всей страны.
Текст: Владислав Стрекопытов
- 23 апреля 2025 ОТ «ОБОРОНКИ» ДО СПОРТА: КАК СКАНДИЙ МОЖЕТ ПЕРЕВЕРНУТЬ РОССИЙСКУЮ ПРОМЫШЛЕННОСТЬ
- 18 апреля 2025 ОТ ХАЙПА К ДЕЛУ: КАК РАЗВИВАТЬ РЗМ-ИНДУСТРИЮ В РОССИИ
- 9 апреля 2025 ВЫИГРАТЬ ВСУХУЮ: О НОВЫХ ПОДХОДАХ И ТЕХНОЛОГИЯХ В ОБОГАЩЕНИИ ПОЛЕЗНЫХ ИСКОПАЕМЫХ В ЯКУТИИ
- 26 марта 2025 Арктическое пророчество
- 26 февраля 2025 ПОЯВЛЕНИЕ ЖУРНАЛА “РЕДКИЕ ЗЕМЛИ” ОПЕРЕДИЛО ВРЕМЯ НА 10 ЛЕТ - АКАДЕМИК РАН ВЛАДИСЛАВ ПАНЧЕНКО
- 14 февраля 2025 Редким землям России нужен ТРАМПлин
- 6 февраля 2025 РЕДКИЕ ЗЕМЛИ ЗА СТОЛОМ ПЕРЕГОВОРОВ
- 3 февраля 2025 РАЗДЕЛЯЙ И ЗАРЯЖАЙ
- 26 января 2025 ВЛАДИМИР ВЕРХОВЦЕВ ОТМЕЧАЕТ 70-ЛЕТИЕ
- 27 декабря 2024 МЕЖДУ МИРОМ И ВОЙНОЙ: ЯДЕРНОЕ ОРУЖИЕ ДЛЯ РАЗРУШЕНИЯ И СОЗИДАНИЯ
- 27 октября 2024 ДЛЯ ГЛАВНОЙ НАУКИ БУДУЩЕГО ЧЕЛОВЕЧЕСТВО ДАЖЕ НЕ ПРИДУМАЛО НАЗВАНИЕ
- 13 октября 2024 Форум «Микроэлектроника 2024» – без высокочистых редких металлов никуда
- 23 сентября 2024 ОТ ВОЗРОЖДЕНИЯ МАГНИТНОГО ПРОИЗВОДСТВА К СОЗДАНИЮ НОВОЙ ИНДУСТРИИ В РФ
- 14 сентября 2024 "Задачи будут решены" – О беспилотниках из первых рук
- 31 августа 2024 ВИКТОР САДОВНИЧИЙ: «ЕСЛИ БЫ НЕ МОСКОВСКИЙ УНИВЕРСИТЕТ, РОССИЯ БЫЛА БЫ ДРУГОЙ»