Техногенный потенциал: в ожидании промышленного освоения

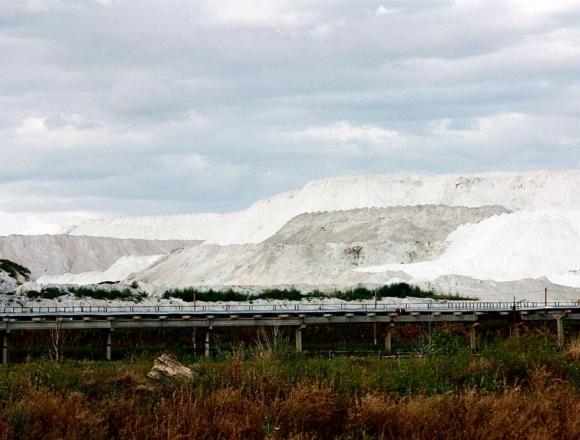
Фото: "Редкие земли"
Техногенные ресурсы России представляют собой неиспользуемую в должном объеме резервную материальную базу перерабатывающих производств и в то же время источники экологического неблагополучия и роста заболеваемости населения[1]. Новая Россия в полной мере унаследовала от СССР нерешенные проблемы комплексного использования минерального сырья и накопления отходов ГПК, ГМК и ТЭК, обусловленные узковедомственной отраслевой специализацией советских горнодобывающих предприятий. В новых экономических условиях эти предприятия ориентированы на получение максимальной прибыли при минимальных затратах. Такой экстенсивный способ горнопромышленного производства находится в полном противоречии с природными процессами минерало- и рудообразования, которые обусловили формирование устойчивых парагенетических ассоциаций промышленно ценных компонентов и минералов-концентраторов с суммарной извлекаемой ценностью, предопределяющей необходимость рационального использования исходного сырья как нево-зобновляемого ресурса природы. С этих позиций очевидна необходимость систематического учета на всех стадиях геологоразведки, добычи, обогащения и переделов минерального сырья специфики его поликомпонентного состава, то есть соотношений между ведущими и сопутствующими рудными и нерудными полезными компонентами, определяющими его потенциальную и извлекаемую ценность. Тем самым обеспечивается возможность подсчета в соответствии с международной практикой извлекаемых, а не геологических запасов сырья и, как следствие, вовлечения их в комплексное промышленное использование с максимальной прибылью, обеспечиваемой не принципом «коротких денег», а выпуском широкого ассортимента товарной продукции при минимальных отходах производства.
Ситуация с отходами обогащения собственно редкометалльного сырья была проанализирована нами еще в 70-х годах на ГОКах Минцветмета и Минсредмаша СССР в процессе выполнения договорных работ по профилирующей редкометалльной продукции. Были оценены допущенные потери этой продукции в хвостах и, с другой стороны, перспективы использования преобладающей в них нерудной части исходного сырья – редкометалльных пегматитов, гранитов и нефелиновых сиенитов. Соответственно в хвостах редкометалльных ГОКов обнаружено накопление неизвлекавшихся минералов лития (Белогорский ГОК в Восточном Казахстане), недоизвлеченного (до 50–70%) лопарита с Ta, Nb, TR, Ti (Ловозерский ГОК в Кольском регионе) и т.д. Результаты этих НИР были реализованы организацией доизвлечения танталовых концентратов на одной из фабрик и попутной добычи поллуцита ручной рудоразборкой на Белогорском ГОКе (Восточный Казахстан), извлечения тантала из шлаков оловоплавильных производств при переработке касситеритовых концентратов с Эге-Хайского (Якутия) и Орловского (Восточное Забайкалье) ГОКов и т.д. Заметим, что зарубежное производство тантала из подобных шлаков, накопленных в Малайзии, Таиланде, Индонезии, достигало 60% его мирового производства.
По результатам количественно-минералогического изучения нерудных фракций и обобщения соответствующих материалов по редкометалльным ГОКам в 70-х годах нами совместно со специалистами ИМГРЭ и ВНИИГЕОЛНЕРУДа (г. Казань) были разработаны рекомендации для Минпромстройматериалов о необходимости организации полномасштабного выпуска молотых K-Na-полевошпатовых, слюдяных и кварцевых концентратов на базе редкометалльных ГОКов, которые по своей инициативе уже начали выпуск и реализацию попутной нерудной продукции в объемах до десятков тыс. т (Белогорский, Забайкальский, Вишневогорский ГОКи). Тем самым возникали возможности сокращения отраслевых затрат в указанном Министерстве, вплоть до прекращения строительства Ёнской фабрики на пегматитовом сырье в Кольском регионе.
В связи с задачами возрождения и развития в России приостановленных и утраченных редкометалльных производств необходимо иметь в виду, что за рубежом в равной степени развиваются обогатительные производства профилирующих редкометалльных (США, Канада, Зимбабве, Австралия и др.) и молотых нерудных концентратов (Норвегия, Финляндия, Канада), а также добыча редкометалльного и нерудного сырья ручной рудоразборкой (страны Африки, Канада). При возобновлении производственной деятельности редкометалльных ГОКов и освоении новых месторождений необходимо учитывать все категории извлекаемых запасов профильных и сопутствующих полезных компонентов, оставшихся в недрах, включая забалансовые, особую роль нерудных компонентов в извлекаемой ценности, доля которых достигает 50–70%, и перспективы вовлечения в промышленное использование накопленных и ожидаемых техногенных ресурсов. Следует также иметь в виду инновационные технологические возможности организации производств новых композитных материалов из редкометалльных и нерудных «отходов» (например, литиевого фарфора, специальных видов керамики и стекол с добавками природных редкометалльных модификаторов), повышение эффективности глиноземно-алюминиевых производств за счет добавок в шихту литиевых минеральных концентратов и т.д. Накопленные (лежалые) и текущие техногенные образования, в отличие от исходного сырья, представляют собой возобновляемые ресурсы, не требующие затрат на добычу, дезинтеграцию и транспортировку, обусловливающих основные издержки горнопромышленных производств. Они характеризуются повышенной извлекаемой ценностью за счет концентрации сопутствующих наиболее ценных полезных компонентов, представленных неизвлеченными редкими, благородными и некоторыми цветными металлами или, наоборот, молотыми нерудными минеральными компонентами — полевошпатово-нефелиновыми, полевошпатовыми, различными слюдяными, кварцевыми и др. Для хвостов обогащения в целом характерна концентрация попутных микрокомпонентов, которые после извлечения главных промышленно ценных приобретают значение ведущих. Доля меди и цинка в суммарной извлекаемой ценности обогатительных и металлургических ресурсов предприятий Урала составляет примерно 30%, в то время как преобладающие 70% представлены сопутствующими особо ценными и токсичными микрокомпонентами (Cd, Co, Ge, Ga, Bi, Tl, In, возможно, Re и др.). При этом максимальная стоимость Re, In, Ge, Ga существенно превосходит уровни мировых цен на Te (в 3–10 раз) и особенно на Se, Bi, Rl, Cd (на 2 порядка).
При химико-металлургической переработке минеральных концентратов происходит перераспределение элементов–«попутчиков» в промпродуктах, отходах и конечной профильной продукции, то есть в различных узлах технологических схем и «элементопотоков». Шлаки, шламы и газопылевые выбросы как объемные отходы черной и цветной металлургии, содержащие повышенные концентрации полезных и токсичных макро- и микрокомпонентов, рассматриваются и должны оцениваться как техногенные химико-металлургические ресурсы.
В России накоплено более 800 млн т шлаковых отвалов черной и цветной металлургии, которые занимают площади более 2,2 тыс. га. Ежегодно образуется порядка 100 млн т шлаков, среди которых преобладают шлаки доменного, сталеплавильного, литейного и ферросплавного производств. Все они обладают поликомпонентным составом, который определяется спецификой перерабатываемых минеральных концентратов, и существенно различаются содержанием полезных и токсичных микрокомпонентов, сопутствующих Fe, Ti, Al, Cu, Ni, Zn, Pb как профилирующим видам металлургической продукции.
Среди научных организаций систематические разработки новых технологических решений применительно к различным видам комплексного минерального сырья и техногенным ресурсам преимущественно осуществляются научными специалистами центральных институтов РАН (ОИВТ, ИПКОН и др.) и «Росатома» (ВНИИХТ), а также региональных отделений РАН (ИХТРЭМС и др.). В системе МПР и экологии РФ технологические исследования осуществляют единичные институты (ВИМС, ВНИИГЕОЛНЕРУД). Однако последние, как правило, склонны к изучению применимости ранее разработанных обогатительных способов и схем к новым объектам геологоразведки, количество которых значительно сократилось. Координация развития инновационных направлений в изучении состава и технологии переработки природного сырья и техногенных ресурсов осуществляется Комиссией по технологической минералогии Российского минералогического общества (РМО), объединяющей и анализирующей разработки центральных и региональных НИИ и вузов.
Научная общественность достаточно активно, особенно в последние годы, стремится привлечь внимание государства и бизнеса к назревшей необходимости решения проблем рационального недропользования, повышения эффективности производств, перерабатывающих минеральное сырье, и вовлечения в промышленное использование техногенных ресурсов. Помимо ежегодных семинаров Комиссии РМО по технологической минералогии проводятся специализированные международные и всероссийские конференции, публикуются их материалы и научные статьи прикладного характера в центральных и региональных журналах РАН, Минприроды и экологии РФ, геологических и технических вузов, осуществляются издания монографий, посвященных рассматриваемым проблемам, и т.д. К сожалению, за редким исключением к проведению таких конференций, особенно вузовских, не привлекаются представители горнопромышленных и сопряженных с ними перерабатывающих предприятий, химико-металлургического и топливно-энергетического комплексов, специалисты которых в настоящее время представляют отраслевую науку. Обнадеживающим исключением явилось проведение в июне текущего года представительного конгресса «Фундаментальные исследования и прикладные разработки процессов переработки и утилизации техногенных образований» научными, образовательными и производственными организациями Москвы и Урала в г. Екатеринбурге при активном участии и поддержке Уральской горно-металлургической компании УГМК[2]. В последние 2–3 года появились признаки обеспокоенности федеральных органов власти и некоторых корпораций ситуацией с накоплением отходов сопряженных производств ГПК, ГМК и ТЭК (Минэнерго, Минприроды и экологии, Госдума РФ).
Единичные примеры разведки и эксплуатации рудных техногенных ресурсов представлены Ковдорским ГОКом в Кольском регионе, организовавшим переработку хвостов обогащения и выпуск 0,4 млн т апатитового концентрата и 1,8 тыс. т бадделеитового, а также Джидинским в Забайкалье, который доизвлекает минералы вольфрама из хвостов обогащения молибденово-вольфрамовых руд. С другой стороны, на предприятиях корпорации «ФосАгро» накоплены отходы обогащения апатито-нефелинового сырья в объемах до 1 млрд т (ОАО «Апатит») и отходы сернокислотной переработки апатита на фосфатные удобрения в объемах от 40 млн т (ООО «БМУ») до 130 млн т. В них установлены промышленные содержания Ti, V, Ni, Ta, Sr, TR, Ga, Rb (с Cs), которые не извлекаются ни на каких стадиях переработки исходного сырья, хотя и учитываются балансами запасов РФ[3]. Указанные потери редких металлов усугубляются экспортом апатитовых концентратов со стронцием и редкими землями (ОАО «Апатит») и бадделеитовых концентратов с танталом, гафнием, скандием, торием (ОАО «Ковдорский ГОК»). Подобная ситуация сложилась и на меднорудных ГОКах и медеплавильных заводах Урала, товарная продукция которых и отходы производства обогащены попутными рассеянными редкими, благородными и цветными металлами. При этом порядка 50% этих микрокомпонентов относится к категории лимитируемых с техноэкологических позиций, включая такие суперэкотоксиканты, как Hg, Cd, As, Tl и др.[4, 5]
Поликомпонентные анализы хвостов флотационного обогащения медно-цинковых руд, отобранных с нескольких уральских месторождений в лаборатории ИМГРЭ в 2012 году, свидетельствуют о существенно различном содержании в них как главных полезных компонентов (меди и цинка), так и сопутствующих микрокомпонентов[9]. Обращают на себя внимание максимальные содержания меди и цинка в отобранных пробах хвостов обогащения руд с Сибайского и Юбилейного месторождений и более низкие — с Александринского и Майского. В то же время первые из них заметно обогащены Co, Mn, Ti, P, Zn, Y, а вторые — Pb, As, Ag, Bi, Sb, Tl. Содержание In, Ga, Ge, то есть наиболее ценных рассеянных редких металлов, среди выявленных 30 элементов в хвостах обеих групп месторождений сопоставимы друг с другом и невелики, так как в основном извлекаются из руд в составе сфалерита (Cd, In, Ga), халькопирита и минералов блеклых руд (Cd, Ge), а также пирита (Cd, Te). Приведенные данные заставляют обратить особое внимание на соответствие экологическим требованиям высокого содержания мышьяка в товарной продукции во избежание рекламаций со стороны металлургов в случаях аномальных концентраций. Для этого суперэкотоксичного элемента необходимо оперативное составление поминерального баланса распределения, что наиболее актуально для сырья новых месторождений и их горизонтов. Очевидно, что организация опережающего минерало-геохимического картирования рудных горизонтов на все особо ценные и токсичные микрокомпоненты до их отработки позволит геологам, обогатителям и экономистам осуществлять многоцелевое прогнозирование специфики поликомпонентного состава руд.
Особое внимание следует уделить оценке перспектив попутного извлечения рения из возгонов и продуктов сернокислотной промывки отходящих газов медеплавильных заводов Урала, которые перерабатывают концентраты традиционного медно-цинкового сульфидного сырья, а в ближайшей перспективе будут перерабатывать сырье медно-порфировых месторождений, обогащенных рением[7]. Создание рекомендуемого для уральских ГОКов научно-производственного комплекса позволит осуществлять регулярный мониторинг за спецификой химического и минерального состава обогащаемого меднорудного сырья с различных рудников применительно как к сопутствующим наиболее ценным компонентам (Re, In, Bi и др.), так и к лимитируемым с экологических позиций (As, Cd, Hg, Тl и др.). Тем самым появится возможность предупреждения потерь потенциально ценных «попутчиков» и одновременно негативных экологических «сюрпризов», обусловленных, например, недопустимо высоким содержанием элементов-суперэкотоксикантов (As, Cd, Hg, Pb, Тl и др.) в сырье, поступающем на фабрику и соответственно в выпускаемых товарных концентратах.
Специального внимания заслуживает проблема оценки извлекаемой ценности и экологичности рудообразующего складируемого пирита, который не только является минералом-концентратором Fe, Сd, Au, но и других полезных и токсичных компонентов. Меднорудными ГОКами Урала в хвостах обогащения уже накоплено 50 млн т пирита. При этом содержание пирита в рудах составляет 60–80%, в хвостах — 90–95%. Потребителем пиритных огарков в настоящее время является только цементная промышленность, где железо пирита используется для формирования вяжущего алюмоферрита кальция. Задача использования пиритного сырья в качестве комплексного источника металлопродукции поставлена с конца 30-х годов прошлого столетия.
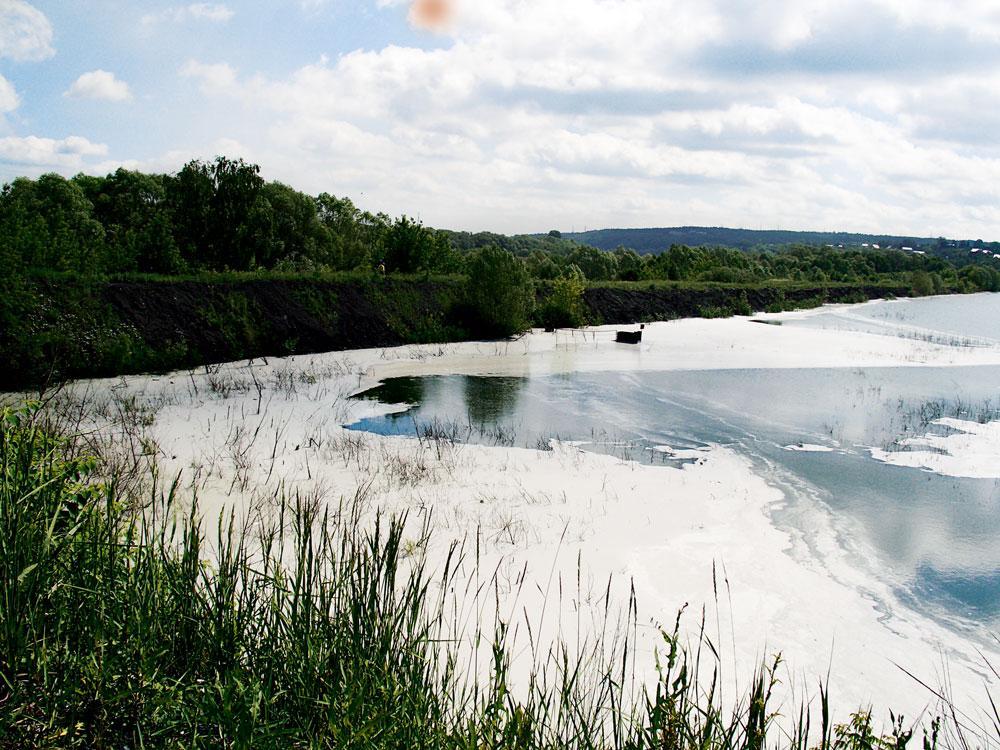
Скопление Si-Al-микросфер на поверхности отстойника шлакозольных отходов Каширской ГРЭС как готовый к промышленному использованию особо ценный продукт (Московская обл.)
Согласно исследованиям А.И. Заболоцкого (2007–2013 годы) пиритные огарки содержат 1,1–2,1 г/т золота, 20–30 г/т серебра, 0,3–0,4% меди, 0,7–1,0% цинка и 40–50% железа, а с их поставками на цементные заводы ежегодно утрачивается 0,5 т золота. В частности, за 50 лет на Новороссийские цементные заводы в составе пиритных огарков отправлено до 10 т золота. Применительно к освоению новых, в первую очередь глубоко залегающих, месторождений горно-химического (фланги Хибин) и меднорудного уральского сырья (Новоучалинского и Левобережного УГМК, Томинского РМК) крайне актуальной представляется организация их детального погоризонтного минералого-геохимического картирования в ненарушенном залегании на широкий комплекс полезных и лимитируемых компонентов с использованием дубликатов проб эксплоразведки. Такое опережающее прогнозирование специфики поликомпонентного состава сырья с последующими изысканиями оптимальных способов и схем его глубокой переработки позволит повысить эффективность использования сырья и одновременно снизить или устранить экологические риски.
Объективная комплексная оценка поликомпонентного природного сырья и особенно техногенных ресурсов, как текущих, так и лежалых, должна прежде всего осуществляться методами детального минералого-геохимического картирования месторождений и хранилищ складируемых отходов ГПК, ХМК и ТЭК. Результатом авторского минералого-геохимического картирования явилось не только оперативное решение актуальных производственных задач, но и разработка методики опережающего геохимического прогнозирования специфики минерального состава рудных горизонтов, вскрываемых при разработке месторождений с использованием типохимических характеристик рудообразующих и акцессорных минералов. Эффективность этой методики, применимой и для расшифровки природы геохимических аномалий при площадных поисках и эколого-геохимическом картировании, а также при разработке передельно-обогатительных схем, доказана конкретными примерами ее использования[3].
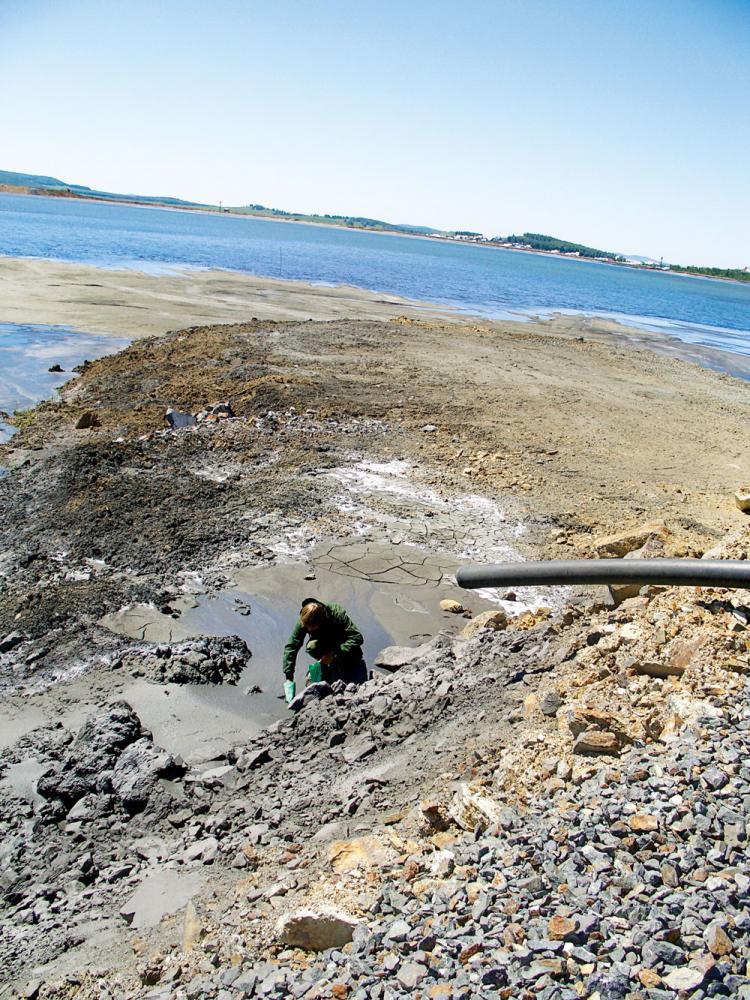
Хвостохранилище Учалинского ГОКа - отходы обогащения медно-цинковых сульфидных руд (Республика Башкортостан, Урал)
Не менее важным этапом комплексной ресурсно-экологической оценки качества разведуемого, эксплуатируемого и резервного сырья является составление поминеральных балансов распределения профилирующих и сопутствующих особо ценных и лимитируемых компонентов для каждого из выделенных при картировании типов руд. Такие балансы, составленные в свое время автором для различного редкометалльного и нерудного пегматитового сырья на Белогорском ГОКе в Восточном Казахстане и для редкометалльных уртитов Ловозерского ГОКа в Кольском регионе, явились основой дифференцированной паспортизации типов руд, необходимой для выбора оптимальных режимов обогащения сырья, разработки инновационных технологических решений и организации мониторинга за отходами производства. Большое значение составление балансов распределения особо ценных и токсичных компонентов приобретает в связи с назревшей необходимостью изучения закономерностей их распределения в материальных потоках действующих горнопромышленных и химико-металлургических крупнотоннажных производств — железорудных (Au, Ag, Tl, As, Pb и др.), горно-химических, медно-никелевых и медно-цинковых, полиметаллических, глиноземных, топливно-энергетических и других, а в ближайшей перспективе, после 25-летнего перерыва, и редкоземельно-редкометалльных.
В связи с известными затруднениями, возникшими к настоящему времени в традиционном физико-механическом обогащении «упорных» видов сырья (руды кор выветривания, субвулканических образований и др.) и техногенных ресурсов, не поддающихся обогащению традиционными методами, определяющее значение в их освоении приобретают разработки прямых обогатительно-передельных схем с использованием физико-химических методов переработки исходного сырья, промпродуктов и выделенных концентратов. В связи с этим в ОИВТ РАН особое значение придается разработкам и использованию термохимических способов обогащения и глубокой переработки редкометалльного, горно-химического и топливно-энергетического сырья, а также отходов их промышленной переработки. Арсенал этих методов представлен модификациями ликвационной плавки флюсованной шихты, пиролизных и плазменных технологий, которые в необходимых случаях комплексируются с теми или иными традиционными способами обогащения, активирования шихты и гидрохимических переделов. С этих позиций положительно оцениваются перспективы промышленного освоения уникального Томторского месторождения на Северо-Западе Саха-Якутии железисто-алюмофосфатно-редкометалльных руд, не имеющего аналогов в мире, перспективы комплексной переработки и обезвреживания отходов фосфогипса с получением кондиционного гипсового продукта, извлечением редких земель и стронция, а также перспективы переоценки традиционного углеводородного сырья и альтернативного — природных битумов в качестве источников сопутствующих редких металлов.
Согласно нашим исследованиям[8], геохимическая специфика изученных углей определяется устойчивыми концентрациями Ti, Mn, P, Ba, Sr, Zr, B и РЗМ, а мазута Ni, V, Ti, Ba, Zn, Pb, Cu. Следовательно, для угольных аномалий в качестве индикатора загрязнения среды обитания может быть использован мультипликативный показатель Ti ∙ Mn ∙ P ∙ Ba ∙Sr, а для «мазутных» — Ni ∙ V ∙ Zn ∙ Pb ∙ Cu, которые позволят оконтурить и расшифровать соответствующие источники химического загрязнения на территориях и акваториях селитебно-промышленных зон как в пределах инфраструктурно-производственных, так и урбанизированных комплексов и площадей. Сравнение среднего содержания микрокомпонентов в опробованных углях и ШЗО свидетельствует о том, что максимальная, шестикратная, их концентрация в отходах углесжигания характерна для Ge и Ga среди редких металлов и Ni, Co, Pb, Zn, Sn — среди цветных, а также бария; меньшая, в 4–2,5 раза, характерна для Ti, Mn, V, P, Sr, Mo, Cu; минимальная, в 1,5 раза, — для B, Zr, Nb, Sc, РЗМ. При переработке золы экибастузского угля по технологической схеме ОИВТ РАН достигнута концентрация галлия до 60–90 г/т, что в 2–3 раза превышает содержание в его традиционных промышленных источниках — бокситах и нефелинах. При цене 500 долл./кг стоимость попутного галлия составит 750 тыс. долларов, или примерно 22,5 млн руб., то есть порядка 20% от стоимости полученного глинозема.
В мировой практике переработки отходов ГПК, ХМК и ТЭК, получившей широкое развитие с 60-х годов прошлого столетия, используются все ресурсные, техноэкологические и экономические возможности производства нерудных материалов для стройиндустрии, металлургии и энергетики. Переработка и использование горнопромышленного техногенного сырья за рубежом достигли 85–90% (США, Зап. Европа). Этому способствовали дефицит и высокая стоимость земель, санкции за загрязнение среды, система контроля за использованием земель и недр, в том числе из космоса, а также поощрительные платежи. С этих позиций оценка потребностей промышленно развитых стран в природном сырье стала проводиться за вычетом объемов возможного производства необходимой продукции из техногенных источников. Промышленное использование «отходов», которые в Европе с 60-х–50-х годов оцениваются и используются как ценное сырье, возрастает каждые 10 лет на 10–30%.
Тем не менее, их количество в расчете на душу населения ежегодно увеличивается на 4–6%, что превышает скорость роста населения в 3 раза. Данные таблицы наглядно иллюстрируют преимущества зарубежных производств широкого круга цветных, рассеянных редких и благородных металлов из различных медно-сульфидных руд сравнительно с получением на предприятиях Урала исключительно профильных медных и цинковых продуктов, иногда сопровождаемых извлечением золота и серебра. Обращает на себя внимание разнообразие форм организации и переработки техногенного сырья за рубежом[1]. Отходы обогащения и металлургических переделов служат объектами эксплуатации как крупными предприятиями, так и мобильными мини-заводами, которым в последнее время отдается предпочтение. Так, например, в ЮАР перерабатывается 18 млн т отвальных хвостов золотодобычи в год (50 тыс. т/сутки) при содержании золота 0,53 г/т, урана 40 г/т и серы 1,04%). Такой комплекс, созданный в Испании, перерабатывает ежегодно 2 млн т хвостов с извлечением золота, серебра и выпуском удобрений, сырья для домен и т.д. В других странах созданы 110 установок кучного выщелачивания золота из отвалов и бедных руд производительностью от 0,1 до 3,5 млн т горной массы в год. США этим способом увеличили в течение 10 лет (1980–90 годы) производство золота в 10 раз. Отвальным, кучным и подземным выщелачиванием с использованием модифицированных сернокислотных методов производится извлечение меди, цинка, свинца, серебра, урана и ряда других полезных компонентов из отработанного или бедного сульфидного сырья и рудничных вод. С применением этих способов США за последние 10 лет увеличили производство меди в 8 раз, которое достигло 0,5 млн т/год при суммарных затратах на 1 фунт меди 0,2–0,4 долл. Ряд европейских компаний осуществляет получение металлопродукции из привозного техногенного сырья: например, Германия — из пиритных огарков Финляндии (Cu, Zn, Pb, Fe), Франция — из штейнов Новой Каледонии, Англия — из канадского никелевого сырья (Cu, Co) и т.д. В 70-е годы за счет вторичной пирометаллургической переработки отвальных шлаков оловоплавильных заводов Таиланда, Малайзии, Индонезии и других стран, накопленных за 100 лет, производство тантала составило 60% его мирового выпуска. В Китае переработка шлаков с заводов черной металлургии сопровождается выпуском ванадиевой продукции, а в США, Англии, Японии, ЮАР и других странах — Cu, Zn, Au, Ag, Pb, Sn, As, Hg, Bi, Cr, Ni. В США, Китае и некоторых европейских странах доказана рентабельность доизвлечения угля из отходов его обогащения. Так, во Франции с 1973 года стали отрабатывать отвалы Северного угольного бассейна, накопленные за 250 лет: за короткий срок здесь было получено 5,5 млн т товарного угля. Китай использует отходы угледобычи на малых теплоэнергетических установках и т.д.
Главный эколого-экономический эффект от вовлечения техногенных ресурсов в комплексное промышленное использование заключается в их инновационно-техноэкологическом потенциале. Примеры отечественных техноэкологических инноваций, остающихся пока невостребованными[6], создают основу регулирования техногенных нагрузок на среду обитания с использованием принципа наилучших доступных технологий производственных процессов, установок и режимов их эксплуатации. Эта новая стратегия, используемая как базовая в экологизации производств, получила известность и признание в Европе как Best Available Technology (Bat). В отличие от традиционно репрессивных способов регулирования экологической деятельности предприятий, оцениваемой «на конце трубы» с применением весьма условных ПДК, ПДВ и ПДС, современная экологическая идеология предусматривает предупреждение экологических нарушений, а не нейтрализацию их последствий. Таким образом, эта идеология становится инструментом инновационного развития, которое по своей сути представляет собой непрерывный процесс самоорганизации и качественного совершенствования.
Очевидные перспективы широкого внедрения рассматриваемых инновационно-технологических методов комплексной гидро- и пирометаллургической переработки различных техногенных ресурсов и бедных руд, не поддающихся обогащению традиционными методами, а также их комбинирование друг с другом в сложных технологических схемах свидетельствует в пользу развития инновационно-техноэкологического предпринимательства как важного элемента государственной научно-технической политики в регионах и России в целом. В передовых промышленно развитых зарубежных странах, в отличие от России, до 80% ВВП представлено конечной высокотехнологичной продукцией, в том числе получаемой за счет глубокой переработки как природного, так и техногенного сырья. При этом более 50% наукоемкой продукции в США создается малыми предприятиями, что в пересчете на 1 работника в 2,5 раза больше, чем на крупных предприятиях. Поэтому создание в нашей стране инфраструктуры малого и среднего инновационно-технологического предпринимательства, кооперированного с крупным бизнесом или самостоятельного, представляет собой исключительно актуальную задачу, требующую целевого объединения усилий и средств всех уровней государственной власти, крупных ФПГ, предпринимателей и представителей академической, отраслевой и вузовской науки. В последние годы прослеживалась тенденция противопоставления базовому минерально-сырьевому сектору экономики России высокотехнологичных направлений ее развития. Авторы этой парадигмы, по-видимому, не представляют себе масштабы обеспечения исходным сырьем, которым традиционно богата наша страна, как перерабатывающего сектора экономики, так и его высокотехнологичных отраслей, на создание и развитие которых нам потребуется не одно десятилетие. Об этом, в частности, свидетельствует фактическая ликвидация развитых в советское время редкоземельных и редкометалльных производств при наличии собственной минерально-сырьевой базы редких металлов. Cвоевременными и уместными должны быть призывы, рекомендации и, главное, конкретные действия по интенсификации деятельности ГПК, ХМК и ТЭК за счет создания условий для их инновационного развития. При этом освоение техногенных ресурсов может и должно сыграть роль «спускового механизма» в технической модернизации всего сырьевого сектора, который остается в нашей стране базисным относительно всех остальных.
Список литературы:
1 Техногенные ресурсы и инновации в техноэкологии. / Под ред. Е.М. Шелкова, Г.Б. Мелентьева. – М: ОИВТ РАН, 2008. — С. 352.
2 Мелентьев Г.Б. Инновационный потенциал и оценка техногенных ресурсов. // Материалы Конгресса с международным участием и элементами школы молодых ученых «Фундаментальные исследования и прикладные разработки процессов переработки и утилизации техногенных образований Техноген-2014», 2–6 июня 2014 г. – Екатеринбург: Институт металлургии Уро СО РАН, 2014. — С. 14–17.
3 Мелентьев Г.Б. Научно-методические основы и результаты комплексной оценки месторождений природного и техногенного сырья. // «Значение исследований технологической минералогии в решении задач комплексного освоения минерального сырья». // Материалы 2-го Всеросс. семинара по технологич. минералогии, 14–16 июня 2007 г., г. Петрозаводск. П.: Институт геологии КарНЦ РАН, 2007. — С. 35–58.
4 Мелентьев Г.Б. Техногенные ресурсы редких металлов, их оценка и технологические инновации как альтернатива экстенсивному недропользованию. // Материалы 2-й областной научно-практической конференции «Новые методы геоэкологического изучения, добычи и переработки руд цветных, редких и благородных металлов», 16–17 ноября 2006 г. — Челябинск: ЧДУ, 2006. — С. 34–40.
5 Мелентьев Г.Б., Малинина Е.Н., Овчарова Е.С. Перспективы организации комплексного извлечения цветных, рассеянных редких и благородных металлов из нетрадиционного природного и техногенного сырья Урала. // Экология промышленного производства. — 2007. — Вып. 3. — М.: ФГУП ВИМИ. — С. 41–51.
6 Мелентьев Г.Б. Инновационная техноэкология и новые задачи технологической минералогии. // Экология промышленного производства. — 2009. — Вып. 2. — С. 40-51. — Вып. 3. — С. 13–29.
7 Мелентьев Г.Б., Трошкина И.Д., Зубков А.А. Ресурсно-экологические проблемы создания производств рения в России и перспективы их решения. // Экология промышленного производства. — 2011. — Вып. 4. — М: ФГУП ВИМИ. — С. 104–113.
8 Мелентьев Г.Б., Малинина Е.Н., Самаев С.Б., Букарь В.П., Степанова Е.Ю. Геохимическая индикация потенциальной ценности и экологичности поликомпонентного угольного и мазутного топлива тепловых электростанций (ТЭС). // Экология промышленного производства. — 2014. — Вып. 3. — М.: ФГУП ВИМИ. — С. 60–70.
9 Горбатова Е. А., Мелентьев Г. Б., Овчарова Е.С., Вдовина О. К., Емельяненко Е. А. Особо ценные и экологически лимитируемые компоненты в хвостах обогащения уральского меднорудного сырья. // Материалы межрегиональной юбилейной конференции ЮУр ГУ, ОИВТ РАН «Комплексное освоение и переработка техногенных образований с использованием инновационных технологий», 13–15 ноября 2013 г., г. Челябинск.
10 Делицын Л.М., Власов А.С., Рябов Ю.В. Инновационная технология глубокой и полной переработки зольных отходов угольных ТЭС как альтернатива традиционному накоплению и складированию. — Там же. — С. 103–108.
11 Мелентьев Г.Б., Ельчин Д.С., Попова А.Н., Каримова И.И., Стулов В.Г. Минеральные новообразования в техногенезе. — Там же. — С. 135–141.
12 Мелентьев Г.Б., Вдовина О.К., Малинина Е.Н., Каримова И.Г., Попова А.Н. Научно-методические аспекты эколого-гидрохимического изучения и оценки воздействия горнопромышленных комплексов на среду обитания. — Там же. — С. 123–130.
Текст: Гелий Мелентьев
- 23 апреля 2025 ОТ «ОБОРОНКИ» ДО СПОРТА: КАК СКАНДИЙ МОЖЕТ ПЕРЕВЕРНУТЬ РОССИЙСКУЮ ПРОМЫШЛЕННОСТЬ
- 18 апреля 2025 ОТ ХАЙПА К ДЕЛУ: КАК РАЗВИВАТЬ РЗМ-ИНДУСТРИЮ В РОССИИ
- 9 апреля 2025 ВЫИГРАТЬ ВСУХУЮ: О НОВЫХ ПОДХОДАХ И ТЕХНОЛОГИЯХ В ОБОГАЩЕНИИ ПОЛЕЗНЫХ ИСКОПАЕМЫХ В ЯКУТИИ
- 26 марта 2025 Арктическое пророчество
- 26 февраля 2025 ПОЯВЛЕНИЕ ЖУРНАЛА “РЕДКИЕ ЗЕМЛИ” ОПЕРЕДИЛО ВРЕМЯ НА 10 ЛЕТ - АКАДЕМИК РАН ВЛАДИСЛАВ ПАНЧЕНКО
- 14 февраля 2025 Редким землям России нужен ТРАМПлин
- 6 февраля 2025 РЕДКИЕ ЗЕМЛИ ЗА СТОЛОМ ПЕРЕГОВОРОВ
- 3 февраля 2025 РАЗДЕЛЯЙ И ЗАРЯЖАЙ
- 26 января 2025 ВЛАДИМИР ВЕРХОВЦЕВ ОТМЕЧАЕТ 70-ЛЕТИЕ
- 27 декабря 2024 МЕЖДУ МИРОМ И ВОЙНОЙ: ЯДЕРНОЕ ОРУЖИЕ ДЛЯ РАЗРУШЕНИЯ И СОЗИДАНИЯ
- 27 октября 2024 ДЛЯ ГЛАВНОЙ НАУКИ БУДУЩЕГО ЧЕЛОВЕЧЕСТВО ДАЖЕ НЕ ПРИДУМАЛО НАЗВАНИЕ
- 13 октября 2024 Форум «Микроэлектроника 2024» – без высокочистых редких металлов никуда
- 23 сентября 2024 ОТ ВОЗРОЖДЕНИЯ МАГНИТНОГО ПРОИЗВОДСТВА К СОЗДАНИЮ НОВОЙ ИНДУСТРИИ В РФ
- 14 сентября 2024 "Задачи будут решены" – О беспилотниках из первых рук
- 31 августа 2024 ВИКТОР САДОВНИЧИЙ: «ЕСЛИ БЫ НЕ МОСКОВСКИЙ УНИВЕРСИТЕТ, РОССИЯ БЫЛА БЫ ДРУГОЙ»